Soldering Wire to Sheet to Create Bangles
Lesson 16 from: Foundations in Metalsmithing: BraceletsMegan Auman
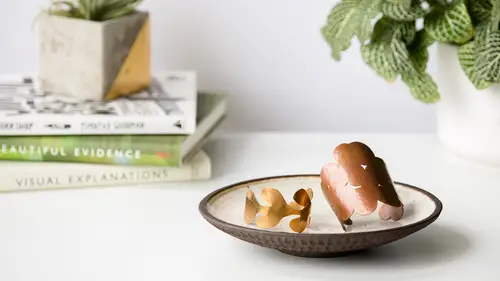
Soldering Wire to Sheet to Create Bangles
Lesson 16 from: Foundations in Metalsmithing: BraceletsMegan Auman
Lesson Info
16. Soldering Wire to Sheet to Create Bangles
Lessons
Prerequisite #1: Basic Metalsmithing Tools
18:08 2Prerequisite #2: Tools for Soldering
14:21 3Prerequisite #3: Soldering Basics
21:14 4Class Introduction
09:39 5Design Considerations for Bracelets
10:33 6Choosing Your Materials
16:12 7Sawing Bracelet Blanks
26:47 8Forming Cuff Bracelets in Wire and Sheet
21:41Determining the Length of a Riveted Bangle
08:11 10Creating a Standard Rivet
16:26 11Creating a Tube Rivet
09:25 12Making a Hinged Bracelet
21:02 13Drilling Holes Cutting Interior Shapes And Finishing Your Clasp
10:33 14Soldering A Basic Round Or Oval Wire Bangle
28:56 15Soldering Other Shaped Wire Bangles
35:17 16Soldering Wire to Sheet to Create Bangles
08:44 17Soldering a Basic Round or Oval Bangle from Sheet
14:09 18Soldering Other Shaped Sheet Bangles
05:59 19Pickling Metal After Soldering
05:42 20Filing, Sanding, and Basic Finishing of Bracelets
11:50 21Patinas: Achieving a Dark Finish with Liver of Sulfur
08:37 22Patinas: Creating a Heat Patina
05:21 23Patinas: Green and Blue Liquid Patinas
08:56 24Sealing and Finishing Patinas
08:35 25Taking Your Bracelet Designs to the Next Level
03:45Lesson Info
Soldering Wire to Sheet to Create Bangles
So that same idea of what we just did with our jump ring, we can also use to think about soldering sheet to wire. So we're going to transition a little bit here where before we were just doing wire and now we're gonna go ahead and think about doing fancy things like this. Where we could actually solder a piece of wire to a piece of sheet and start to create multiple shapes. I'm gonna let you ask me the question you asked me about stamping on the other bracelets. Ask me that about this here. Could you use dye stamps to stamp words onto that metal? Absolutely. So for those of you who have those letter stamps at home, this is a great application for that. I would stamp this before we do the soldering operation in this case and actually even before I bend this one. So if you have stamps or things like that, you could use something where instead of making the whole cut you could do a little plate here and solder wire to it. And so in this case, we have two pieces here. This one is bent ...
and then this one is flat. So again, they kinda give you a different aesthetic. This is definitely kind of a more modern vibe with a sort of flat geometric. And then this one I feel like has a little bit more of like a traditional bracelet feel because it sort of matches the curve. So the most important thing when we're doing this kind of soldering, also just for reference, I would probably not use a piece of sheet this thin for this This is 22 gauge. It's because it was what I had sitting around in my studio but if I was really making something like this, I would probably use 20 or maybe even because this feels a little bit thin in comparison to my 14 gauge wire. So that's just a little bit of an aesthetic choice that I probably wouldn't make if I wasn't making a demo sample but it just so happened that I had this was the gauge of bronze sheet I had sitting around to go with my bronze wire. So with both of these, it's really important. Let's see if we can see. That we get that fit right. So you can see this one was filed, the ends were filed to the flat. It's a little bit hopefully easier to see in this guy. So you see how now these are filed a bit more of an angle? Because I've curved this wire. So I went ahead and filed those so that that's got that tight fit on it. We'll set this guy up for soldering. We will actually get this one to work. So same thing. I'm gonna set this up here in my cross locking tweezers. And in this case, I wanna kind of pay attention to where this is. Obviously, I wanna kinda center this. If you are a person who likes things to be really precise, what I would recommend is I would not recommend drawing on this with a sharpie because the sharpie's gonna make your metal dirty. Instead, I would get a scribe. So scribe is basically like our center punch but a little bit sharper and pointier. And actually like scribe like a little X where you want that to be so you know where it's gonna be. Instead of doing what I'm doing and just eyeballing it. I'm just gonna eyeball it. Looks good enough for me. And the same thing with this, you know, this wire to sheet, kinda combo as with our other pieces. So the one thing I didn't do here and now I'm sort of regretting that decision is I probably should've taken just a little bit of sandpaper to the bottom of my sheet where we're gonna solder this to make sure that it's clean and grease-free so they have my fingers all over it. But now, it's all covered in flux. So we're gonna give it a go. And if it doesn't work, well, we know why it probably didn't work, right? Keep that in mind. So something to think about is that you do wanna make sure it's clean. Obviously, as we're filing the ends of our wire, that's removing any grease, any dirt, any oil so those are gonna be clean. But our little piece here not so much. Probably should've given a file. And in this case, I'm gonna put like three pieces of solder in there because it's a slightly thicker gauge wire and I've got a little bit more surface area in the sheet. I'm just putting some solder in there. And this is one of those processes that, you know, you can watch me do it and hopefully as we keep doing it over and over again over this lesson, you start to get a better sense of how it works. But really, until you do it for yourself, it's a little hard to kinda understand. But the more you do it, the more you start to see like oh, this is the color change. We can go ahead and turn down our lights. Oh, this is the color change that our flux goes through and oh, you know, this is what this looks like. Oh this is the color of the metal right before I accidentally melted it. So you start to get kind of a sense for what's happening. You can see how my flux wants to bubble a little bit there because it is very liquid-y still so I'm just trying to give that a second to dry here. So you know, that's why I really encourage you guys to kind of just get this stuff and play around so that you can actually, you know, kinda see what's happening. Test it out for yourself. Again, start with brass bronze or copper because they're so much less expensive and if something goes really wrong, you have just melted $40 worth of silver. So start with those kinds of metals but just kinda don't be afraid to get in and play. You can see how the end of this sheet is getting really hot. See how it kinda floated there? Wasn't even paying attention and it worked. Hopefully, it worked. That looks pretty good. So you know, get this and play around. And then I think it's one of those things where I mean, if I were you, when I was just starting out so we got actually float in there pretty nicely. You know, when you go back and try this for yourself, then if you have bought this class you can come back in and watch the videos and some of this just makes so much more sense after you've tried it yourself. So that's something to keep in mind as well. I want you guys to kinda come in and try and experiment and then hopefully come back and sort of feel like, oh, that's what she was talking about. Because as much as we can watch, look, that one actually worked. As much as we can watch lots of videos, there's something about doing the process for yourself where you really start to learn things. Alright, so questions about that one? That one went so much better where, apparently, where I wasn't thinking about it so hard and I was talking about other stuff. Makes me a better solder. Just a quick question. Not sure if this is the right time but I'm gonna ask anyway. Do you use boric acid and de-naturated alcohol before soldering brass and bronze? I do not. I usually just, I'm sure that that's a way that people say it gets it cleaner. Probably makes the surface a little more receptive to the solder. I usually just sand stuff and use it. Great. Thank you. And I should also mention, you know, I talked about this in a previous class, there is not one right way to solder. So my grad school professor, all of us graduate students taught intro metal smithing classes and she used to say that she could tell whose the student had had as their intro teacher based on the way they soldered because every grad student coming from a different program had learned to solder a slightly different way. Like I know some people who will pre-ball all of their solder and then they'll put into little balls and then in the middle of the soldering process, they will pick it up with their soldering pick and place it on in the middle of the soldering process. That's so not me. I don't know how you do that magic. Not my skill set. So you might see things online or in forums where people are talking about I do it this way and I do it that way. That doesn't mean that they're wrong or I'm right or that I'm wrong and they're right. There are really a lot of different ways to solder. Some of it is just about finding what works for you. I like to pick things up with my tweezers instead of my solder pick. So kinda feeling free to play around and see what works best for you.
Class Materials
Bonus Materials
Bonus Materials with Purchase
Ratings and Reviews
user-d7f7ae
This is a great addition to Megan's metalsmithing series. She makes the topic really approachable. Bonus that metal patinas were added in to the class. I loved the class!
a Creativelive Student
I really enjoyed this class! It was very informative and gave me a lot of ideas for expanding a jewelry line to include a variety of bracelets and finishes.