Threading a Bobbin and Sewing a Stitch
Lesson 2 from: Singer ONE™ Sewing Machine - Fast StartBecky Hanson
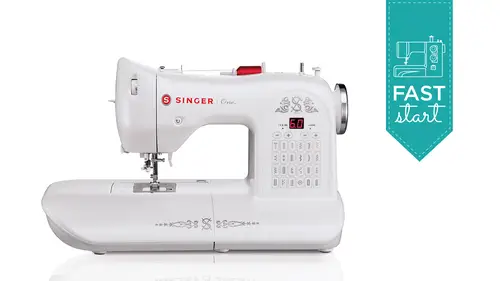
Threading a Bobbin and Sewing a Stitch
Lesson 2 from: Singer ONE™ Sewing Machine - Fast StartBecky Hanson
Lessons
Machine Overview
09:44 2Threading a Bobbin and Sewing a Stitch
23:12 3Basic Needle Styles and Threads
20:00 4Stitches Examples and Button Holes
14:39 5Ribbing and Elastic Insertion
16:29 6Blind Hem Stitch and Applique
26:37 7Hemming Techniques
18:01 8Free Motion Techniques and Flower Stitcher
26:05Lesson Info
Threading a Bobbin and Sewing a Stitch
As I said, you get a few bobbins with your machine there's one in it and three that were in tray, but sometimes you feel those up with some colors and you want to get some more bobbins for other colors of thread that you're going to use and I want to show you what to look for when you go to the store because bobbins are not all alike, and I know some folks don't even realize that there is a big difference between them just depending on machine siri's. So here are your machine uses what we call a class fifteen j bobbin so right here, if you look all these say singer at the top and bobbins air pretty much available anywhere where sewing notions are sold, but they all say singer at the top and they all say bobbins, but there's a number here there's fifteen fifteen j sixty six if you look a little more closely at thes and what you want to make sure you do is always used the exact same bob in style that comes with your machine. Oh, you don't substitute and go well, I like metal bobbins bett...
er, so I'm going to put a metal bob and in there um you have to use the same style of bob and that your machine comes with and the reason for that is because machines are calibrated the the whole threading assembly and bob in case assembly is calibrated for that style in that weight of that bob in and when you substitute bobbins you can create stitching problems for yourself so you want to look for exactly the same bomb and so here obviously these are metal, so those go away and then at a glance you have these other bobbins that still look very similar to the one that comes with your machine but what we wanted we see right here this says class sixty six don't want that one cause minds fifteen j here you see fifteen j and fifteen and you might see these on the shelf and go well, fifteen is fifteen what does the j mean? I'll just get the fifteen but they actually are different when you see them side by side and to touch and feel them you can tell they have a slightly different shape to them and so if you were to use a fifteen in your fifteen j sewing machine again, you could have stitching problems. It doesn't fit properly in the bob and assembly. So you want to look for the class fifteen j when you go shopping for additional bobbins for your machine and I'll bet I solved a few problems for a few folks right there, okay, so let's go ahead and wind that bob and so I'm going to press this bob and release cover again remove my bob and from the machine and I'm gonna put some thread on the top let's slide that on this spool pin and I'm going to use this medium size cover for this particular spool. Now, up here, I like to hold my thread kind of it's kind of like when you floss your teeth kind of hold it with two hands like this, and you're gonna bring it in front in front of this silver guide, so just bring that in front and then slight see this diagram right here. This diagram actually shows you that you slide this thread and, like it's, like kind of like flossing your teeth, just make sure you feel that slide in there. I'll do that again for you just bring it in front of that silver guide and then just let slide that and they're like so and then for the bob and you see this picture of this diagram, it looks like a little cursive letter e so you're going to bring that arone this bob and winding attention disc like so, and then we're going to come on over and put the threat in the bobbin cut this thread it's getting a little long. Now, what you don't want to do is put your bob and on here, wrap your threat around here like this, and then push it over and go, because what you can do is start threading the bobbin unevenly, and if it ruth shreds unevenly or sloppy that's going to affect your stitching, you may have poor quality stitching. You might have a bit of a mess when you try to sew it might not even so it all. So you want to thread you're bob and properly the way it shows you in your quick start guide and in your manual, and what we'll do here is we're going to come in from the center, through the hole on the bobbin, so you come in from the middle, go from middle, outward like that, and then hold the thread end and then slide the best this bobbin onto your bob and winding spindle and make sure it goes all the way down if you have it's sticking up a little bit, what probably will happen is as you get winding, and when you push this over and start winding, the thread can start winding underneath your bob and and you'll just have ah, a bit of a mess to clean out from under there, so make sure that's all the way down when you get ready to wind this and then we're going to push it over to the right to engage the bob and wind er and step on the foot controller to get started and let it go just a few revolutions, you'll stop momentarily to trim that thread tail out of your way, and then you can resume threading know when the bob and gets pretty full pretty much full, it will be the threat itself kind of rubs up against that bob and winding stopper and the be bob and will stop turning and you can push it to the left and take your bob and off. You don't have to fill the bob, and if you only want a little bit on there, you can stop any time. I'll probably feel this about a little over half full for what we're going to do today, because I'll be changing off to some others I've already won't for some of the techniques will do, but now we're ready to remove the bob, and so we're going to push it to the left, lifted off the bob and winding spindle. Use your scissor to trim that thread, and then we're going to place it in the bob in case now, when you lay lay this in your bob, in case you want to make sure you put this incorrectly or again, you could create yourself since stitching problems. You want to put this in drop it in and as you pull this thread you should see the bob and turning against the clock like seoul okay if you drop this in here and you have him pull your thread so it's going clockwise again you could run into some stitching problems in fact it could even work itself out of the threading path I'm going to show you in a moment and you won't have any tension on your bob in at all and that creates other issues so you want to make sure that you threat you're bob in so that when you lay this in here it's going against the clock and if you notice there's a little diagram right here on the free arm of your machine that shows you that the bob and should be turning that direction so that's a good little double check and that's also on your quick start guide then you have according to this diagram I'll show you on the diagram and then I'll show you here there's a little notch that the thread slips into bring it around and then bring it to the back and right here is where that little notches so we're gonna lay the thread in this notch and then like so okay, I'll do that again for you so you drop your bobbing in there's a little guide right here you slide your threat in there and then back like so and you've got your bobbing in there correctly. Now this machine has a feature called the drop in so bob and features so on other machines I've been showing up to this point we leave the tail loose like this until we've threaded the upper thread and then we draw the bobbin threat up and you can certainly do that with this machine, but on this one there's a past that's cut away on the needle plate with a little thread cutter back here so you can actually after you threaded you're bobbing in the bombing case lay the threat in this thread path, bring it around and trim the end, and then when I after I thread the upper thread, I can just begin sewing it stages the thread for me, so I don't have to draw the bob and thread up to start sewing so that's a real convenient feature for you there time saver. Now we're going to thread the upper part of the machine, and so here we're going toe you know we don't need that bob and winding tension disc anymore. We're going to still put our thread in front of that silver guide, we're going to bring it into our pretension area up here and in machines I've been showing up to this point you'll notice that I had a thread path where I went down around, up, over a take up liver and then back down again, but you'll notice this machine has one simple thread path, so all I need to do with this machine is just bring my threads straight down, and then I'm going to put it around my, um, uh, thread guide down here, lower my presser, foot lifter and there's, a threading mechanism that I'm going to use over here. This is going to automatically thread the eye of the needle for me, so you'll stage your threat under this. It looks like two little fingers like this. Stage it on this thread holder, and when you press this lever down and release it, he's left my thread tail a little longer there. Okay, take it out of this one. Here you go. I put the tension down on it to hold it a little firmer. You could see that rick needle should be in its highest position. That's probably what was happening there gets a needle in your highest position that automatic needle threat er just threads the eye of the needle for you, and you're good to go. Make sure that so you don't have happened. You what just happened to me, I did not have my needle in the highest position, so it couldn't engage into the hole so just unusual hand wheel over here to raise the needle to its highest position and then you press that threading lever and threads the eye of the needle for you I don't have to do it manually okay so we are ready to start sewing so I'm just going to grab a piece of fabric here and so a seam I got some lavender just kind of kona cotton and you put your fabric underneath the presser foot lifter and our foot controls plugged in everything's threaded were on straight stitch when you turn them she na nicholas automatically to straight stitch and we'll talk about your stitch panel in just a little bit and we step on the foot controller again I don't have to drop that bob and thread I can just start sewing thanks to that drop in so bob and feature and then as you more you step on the foot controller the faster the machine goes so you completely control that yourself stops with the needle in the opposition and then when you're finished sewing you can either cut your threads manually or you can use this threat or hear that that this is thiss way where we stage the thread for threading it's also a thread cutter and the reason I like to to use that is it keeps my thread tales nice and long when you're done sewing what I often see especially beginners do is cut the threads really close to the presser, foot and there's there's nothing wrong with that, except for just the fact that when you start to so again, you're probably going to have your thread come out of the eye of your needle, and you're constantly re threading the needle, so if you trim them long enough or trim the manually long enough, you won't have that happen for you. So where do you let me just talk about reverse to there's a reverse button up here? So, so far, what we did was we just soda straight stitch, but if you're really sewing a scene, you want to lock the stitches with your reverse, so you'll so forward a couple stitches to three stitches, then this is your rivers button here infront it's very convenient right in front, you hold that down for us long as you want to sell in reverse and then release it and then so forward again, when you come to the end of your scene, you'll simply touch that reverse button again to do the same thing at the end that will back up those stitches, and what it does is it just locks the scene if especially if you're a new solar, I'll explain that if here I just had a seam, I just sold but if I lock the stitches than my, my seem won't come undone, so that's real important to lock your scenes and look for your garments and home to court projects and so on. So again, if you are new to sewing and you don't know some of this terminology, this is your seem, and this area from the scene over to the edge of the fabric is called your seem alone's and various projects. When you download projects, when you read sewing instructions, whether they're from blog's or commercial patterns, or from our project on our singer website, there will be a recommended seem allowance for the project that you're doing. And so how do you know where to guide your fabric? According to your on your needle plate, there are seem guide markings that indicate half inch, five eighths inch and so on, so that you can use thelancet on the needle plate for guiding the edge of your fabric, so you would have keep the edge of the fabric lined up as you so with one of those markings now, particularly for new sewers that's a little, they don't know quite how to do that yet, and what what you'll often see happening is a new sewer will put the foot down and start sewing, and they tend to just kind of watched the needle and you really don't need to do that is so much because the needle's going to do what the needle's going to do, what you want to do is kind of watch the needle, but watch where you're guiding the fabric to keep this seem alone straight if you're just staring right at the needle and not paying attention of this, you're going to be kind of veering all over the place and you're not going to have a nice level even seem seem allowance and one of the things you can do to help you as you're getting used to sewing, especially when when you're nuer is you can use a masking tape or a painter tape and you can put that tape on your needle plates so it's a little more visual for you and as you so keep keep the edge of that fabric lined up with the edge of that tape and that sometimes being a little more enhance because it's a brighter color it's a little more visible really helps you to do that. I've been showing the other groups this week and I'll show you a cz well, we are going to be launching thie end of this year, you'll probably be able to acquire one of these is a what we're going to call us so easy foot and what would happen is you would just simply take off your regular, press her foot and snap on this so easy foot and what that will do then instead of using something like a tape, is it's going to give you an actual physical edge against which you can guide the fabric and you might find that really helpful as well? Whether you're a new sewer or not, you might just really find that helpful, and so you could be looking for that near the end of the year it's going to be called this so easy foot scw so easy foot hazel will put our regular presser foot or general purpose foot back on the machine, okay? And I want to talk a little bit now about thread tension. Um, it's me through this one away and I'll start with this one, so we're going to soar seem again and you'll notice when I turn this over, I have no I have a white thread in the needle and a white thread in the bob, and if you would do this at home and you want to test your stitch, you might try putting a colored thread in the needle and a different colored thread in the bobbin as you get to know what your stitches supposed to look like, but here, when you look at my stitch, it looks perfectly even on the top perfectly, even on the bottom. And I have a slide that I'm going to show you on our monitor, and this is an example of what stitch should look like. And I'm just going to walk up to the monitor to show you what to look look for here on the piece that we just showed we have nice, even stitches on the top and nice, even stitches on the bottom and again, if you try this at home, try two different color so you can really see how they intermarry but the stitches actually, um, lock in between the two fabrics. This is the top fabric, and this is the bottom fabric, the underside of your fabric. And this is what a nice balance stitch looks like. If your needle thread tension is too tight, you'll notice something like this picture here, where the needle thread almost looks like it's a straight line across the top. The bottom side might look totally normal, but what's happening is the needle thread is so tight. It's actually pulling some of the bob and threat up to the topside. And even if you ran your finger over the top of this, he would almost feel like little beads. That's a new indication that your needle thread is too tight you'd almost be able to take that needle thread and even pull it right out because it's, almost like those are little loops and the needle threads there and you could just slide it right out. That's your needle through attention is too tight, and you need to back down on that just a little bit. We'll show you how to do that on the on the face of the machine, there were the tension wheel is here's an example of where the needle thread tension is too loose? Looks pretty normal on the topside, but on the bottom side is where you have that sort of beating effect. Where it's it's way too much thread in the stitch and the bob and thread it looks like it's pulled tight and you'll have just the opposite effect, and in this case, you would need to increase your upper thread tension on a top drop in bob and machine like this, you don't really need to adjust your bobbing through attention. It's it's precept at the factory so you do pretty much all your adjustments with your upper thread tension. An exception for that exception for having stitches be balanced would be for when you do decorative machine stitching and here this shows you the top side of the fabric. This is the bottom side of the fabric, and here I deliberately do loosen the upper thread tension just a little bit s o that my upper thread my needle thread does show a little bit on the bottom side because I don't want to see any of the bob and thread at all on the top side of my fabric I just want to see those pretty decorative stitches, so that would be an example of when you would deliberately loosen your upper thread tension now here you've probably had had something like this. I think at some point in all of our sewing life we've had something like this happen where it looks perfectly normal on the topside your sewing along and why does it sound like it's a little load and you turn it over and you look like the fabric on the underside looks like it has a big bird nest of threat underneath it it's all loopy and messy looking and you're like, what is that? And folks often say, oh, something's wrong with my bob intention that actually has nothing to do with your bob intention believe it or not, as counterintuitive is it sounds, that means u didnt thread the upper thread correctly and so the best thing to do there is to simply trim your upper thread, remove the thread, make sure the presser foot lifter is up and re thread the machine. Ok, so let me just show you that I'll show you a little test you can do to make sure that you have your machine threaded correctly when you have threaded your machine here's a little test you can do, I'm just going to grab the needle thread, so before you put it underneath the presser foot, you just have the needle threaded and you'll notice the presser foot lifter is up, right? So when I pull this thread, you notice how just freely I can pull this thread. I'm just easily pulling that thread through the thread path when I put the presser foot lifter down to sew and then I pull this thread, I should feel resistance on this thread see how I'm just pulling with the same amount of pressure, but the threat isn't pulling through it's actually tugging the needle that means I've got resistance on my thread. It means I have tension on my threat if my presser foot lifter is down like this and I'm still able to pull that thread really freely like I did a moment ago when it was up, that means I'm really not in my tension. And the best thing to do is just cut your thread, pull it out, make sure you're pressing foot lifter is up and re thread your machine and then do yourself that little thread tension test again. And if you feel when you put the presser foot lifter down, if you feel a little resistance than you know, you've threaded correctly and that will eliminate that bird nesting on the underside of your fabric. Okay, so cut your threat up here and make sure you lift your press a foot left before you begin. Actually, when you thread your your upper thread, no matter what type of thread you threat on the upper threat, the very first step before you do anything in your thread path should be to raise your presser foot lifter because it makes the machine able to receive the thread. If you're presser foot lifter is down, chances are you're you're you're not going to get your machine threaded correctly always, always, always, always, always, always lift the presser foot lifter before you begin threading, and that should eliminate that bird nesting that you have there to try that little tension test and you'll know that's how you'll know before you even start stitching, ok, so let's talk a little bit, then about and this is your tension well up here, and I've I told you, I would mention that so there's a little range and here called otto, its kind of colored in a gray color, and for most of your sewing, you can just leave it in that auto range. Don't be afraid of your tension, though people get really afraid of attention on a sewing machine, and I think it's just not knowing how to how to work with your selling machine, but that tension test I showed you that that will eliminate that bird nesting issue we talked about, but different threads. You work with different needles, you work with different fabrics you so you may be adjusting this for the look you want and for the thickness of your fabric for that thickness of your thread to get the look of stitch that you want. So this is really like a fine tuning device, so to speak, for the look of your stitch, so don't be afraid to use this place. Like I said earlier for decorative machine stitching, I might loosen it down a little bit off of auto to relax that upper thread deliberately, but I go back to sewing a construction seem, and I'll put it backto auto, um, a place you might tighten it up is if you're going to maybe do some easing of a sleeve, capturing the arm sigh of, ah a blow blows pattern on the sleeve, and you might want to have that just couple little bit and do it. Do a stay stitching you might increase the tension a little bit to help it cup ah, little tete to sew it into the body of your blow, spitter. So their use it as your friend. Don't be afraid of it, okay?
Ratings and Reviews
Zahulie
Great Class and fantastic to learn all the awesome things this Machine can do. Becky explains everything very clearly and was a very enjoyable class.
Kelly_H
I'm not an expert at sewing, but I feel like I could sew anything after watching Becky Hanson's class. Another great class, another great instructor brought to us by Creative Live!
WilliamM
I was watching the course free and was so impressed with what I was learning that I purchased it at the break. I like it very much. Now I would like to know what "extras" will be provided and what "student work" will be asked for.