Creating a Hinge & Clasp from Tubing: Part 2
Lesson 19 from: Explorations in Metalsmithing: Hollow FabricationMegan Auman
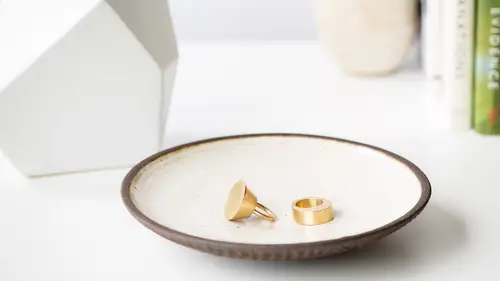
Creating a Hinge & Clasp from Tubing: Part 2
Lesson 19 from: Explorations in Metalsmithing: Hollow FabricationMegan Auman
Lesson Info
19. Creating a Hinge & Clasp from Tubing: Part 2
Lessons
Prerequisite #1: Basic Metalsmithing Tools
18:08 2Prerequisite #2: Tools for Soldering
14:21 3Prerequisite #3: Soldering Basics
21:14 4Class Introduction
07:42 5Design Considerations: Making Paper Models and Thinking Three Dimensionally
14:40 6Creating Non-Soldered Forms: Bending and Folding
18:38 7Creating Non-Soldered Forms: Dapping and Sinking
17:19 8Pendant Preparation & Soldering Basic Forms
22:56Creating a Soldered Cone
06:29 10Hollow Fabricated Ring: Sizing and Making the Internal Ring Band
09:05 11Hollow Fabricated Ring: Making the External Shape
37:59 12Hollow Fabricated Ring: Constructing the Ring Part 1
22:05 13Hollow Fabricated Ring: Constructing the Ring Part 2
38:06 14Hollow Fabricated Ring: Finishing the Ring
04:18 15Variations on the Hollow Fabricated Ring
05:02 16Building a Locket
08:06 17Making a Tube Rivet Hinge
11:45 18Creating a Hinge & Clasp from Tubing: Part 1
14:26 19Creating a Hinge & Clasp from Tubing: Part 2
21:32 20Adding a Pin Back to a Hollow Fab Form
14:32 21Finishing Your Hollow Fabricated Jewelry
07:59 22Turning Your Hollow Fab Projects into a Cohesive Jewelry Line
07:54Lesson Info
Creating a Hinge & Clasp from Tubing: Part 2
And now we need to go ahead and attach this to the other side. So, a couple of notes here. Obviously, I'm kind of just doing this as a sample. So, in your real one, these edges would meet. You may even wanna put a deck on your locket and trim that off like we did here. So, know that you probably do a slightly neater job than we're doing in this moment. But I just kind of wanna demo the process for you guys, and again, get your wheels sort of spinning. So, we soldered these on here but now what we need to do is insert a piece of wire through here that attaches to our other side. So, there's one little concern that we have as we're doing that which is that there is a potential for the solder on this little piece of tubing here and here to wanna reflow while we're soldering to this other piece. So, there's a nice little trick that you can use which is actually just to get some white-out, some Liquid Paper and actually paint that right on your solder seam. And so this acts as an inhibitor.
So, it's a little bit nasty. It smells a little bit bad when you're soldering it. And there are actually products that do this better. So, Rio Grande makes a product, I believe it's called Stop-Flow. It's green. We used to use it like crazy in undergrad. It was like the magic that kept your solder from flowing. It's definitely better but it's also more expensive and you kind of have to buy like a big bottle. So in pinch, I run out to the store, I grab a bottle of Liquid Paper, and we're good to go. So, I'm just gonna paint that on my hinge so that I don't have to worry about accidentally re-flowing that when I go to solder that in. All right, so now what I wanna do is actually make the hinge by putting some wire through here. So, I'm just gonna cut a length of wire that fits through my tubing. I'm not worried about this being like a perfectly tight fit. It's a little loose through my tubing. That's okay. If we were doing a traditional three knuckle hinge you'd want a piece of wire that fits really snugly through your tubing because you actually set a three knuckle hinge like a rivet. But in this one, we're just bending it around. So, all I'm doing here is just straightening it so that as it runs through my tube it's actually straight. Som then I'm gonna thread this through here. Now, I need to just bend it in a way that I can get it to come around and solder it to this. So, I'm just gonna go ahead. I like kind of a crisp bend. Actually, I'm gonna take my thinner nose pliers here and just kind of bend this around so that I've got a little bend here. I could have done that first one not in the tubing but obviously once it's in the tubing can't do the second one that way. So, I'm just gonna bend them both there. So, I'm just gonna bend this over so I've basically got essentially what looks like a little staple. And then I'm gonna hold this guy up and figure out what kind of bend do I need to make to now get this to match on there? So, I'm gonna go ahead and mark this. You know, when you're working in your studio, when you're designing things for the first time, when you get to the point where you're not following a step-by-step project this is really how that workflow goes, right? It's thinking about how is this gonna work? What do I need to do next? Okay, here's where my bend is. Let me mark that. You know, let me try to get that bend right. So, a lot of this is really that kind of experimentation to sort of figure things out. Yes, there are certainly kind of standard processes but there's a lot of this trial and error, putting things together. So, I think my life would be so much easier if I actually just grabbed some pliers that were round to begin with and did a little bit more of a bend in here. So, I'll bend that. I'll bend that. And then try to match this guy up here. So, a this point you can decide where is it that you want this to match? Where do you wanna solder it? You know, in a perfect world I could kind of finagle this so that the solder point was a little bit closer up, was sort of like up here. But at this point, I'm kind of gonna take what the form is giving me. Let's see if I can find a good spot. And so, I'm kind of looking like if I cut it down here it's gonna give me a nice long connection point. And we're gonna assume that that's the back of our locket. The one thing that we didn't do in this process thus far is if we were gonna hang this, we haven't put any kind of bail on it. But with something like this what I would probably do is get this soldered on and then come back and use wire or something to create just a bail soldered off of here, just like kind of we're doing. I'm gonna go ahead and cut these down. And you could do a lot of different things here with these ends. You could actually hammer them a little bit so they were a little flat, if you wanted kind of that. Most of that, again, is just aesthetic decisions. You know, do you want them flat? Do you like them a little round? So, I'm gonna go ahead and do that. And actually, since I just wire cut these, I'm just gonna go ahead and just file the ends of them so they look a little nicer. You may decide that you actually wanna file these into some kind of taper. You could actually file them into a taper so they almost sort of faded in. And you could even do that after so that we could kind of leave them the way they are now, solder them, and then come back in and sort of solder them to taper. So, they almost sort of fade into our dome if you wanted. So, there's a lot of things you can do here. So, what I'm gonna do now is just sort of get this lined up where I need it to be. And since this flips at this point, I'm not gonna worry about cleaning or fluxing. What I wanna do now is actually just get this binding wire into place so that nothing is gonna move around on me. And this is one of those where binding wire is a little bit tricky cause it's gonna wanna twist and slide. This is where I love that tube rivet hinge cause I can just painter's tape it. Can't do that when we're about to put fire on it. (laughs) Unfortunately. If there was fireproof painter's tape, I would be in heaven. So, I'm just going to binding wire this in place. Just so that it's can't go anywhere. And I don't need it because I'm not trying to actually solder this seam. It doesn't have to be perfect. It's really just about kind of keeping things in alignment. So, now I'm gonna go ahead sand my surface. And I did a pretty terrible job with this. So, I'm not so worried about gas building up cause there's a lot of places where air could escape in this one. If that was a really big concern, you could solder this in place with the locket open instead. So, you could just open it up, lay it flat, and do that as well. I'm not so worried about bad things happening cause there's a pretty ginormous gap in our locket at this point. All right. What I'm gonna do now is I've got, again, my white out on there so that I don't have to worry so much about this re-flowing my previous seam. So, I'm gonna come in here. And this is one of those where I should without a doubt fight every urge I have to put a lot of solder on here. Cause it's just gonna bite me in the butt later in terms of a lot of clean up. So, what I'm gonna do, I'm gonna use easy in this case because while we might need it again on this other side it's fine. I wanna use something that's maybe a little less than what we did on the other half of the locket. Actually, I'm lying to you. I'm gonna use medium. And the only reason I'm gonna do that is because those pieces are much smaller than those ... Like I used every small piece of the easy in one of our previous steps. (laughter) So, I'm gonna use our medium because it's significantly smaller. And that's gonna make our life easier. So, I'm just kind of putting a couple pieces in here. This isn't a perfectly tight fit. But if I need to, just like I did when we put that piece of tubing on for a hinge, if I just need to kind of press down on this a little when our solder is flowing, I will do that. And I said I was gonna fight my instincts and now I'm not. (laughter) Do as I say, not as I do. And I wanted to put that one on the outside. Tell us when and where you choose to wear your safety glasses or not to wear your safety glasses. So, my decision-making on the safety glasses is there's something metal that's gonna break and fly into my eye. So, with a saw blade it's that. With a drill bit it's that. So, those are generally the two places. I'm not so worried about it on soldering because even if the solder pops it's not going that far. So, that's usually how I make that decision. You can certainly err on the side of caution and wear them more often than not. I am not a glasses wearer, so I cannot actually stand to wear glasses for that long. So, I put them on when I know I wanna be concerned about the safety of my eyes. But I don't wear them throughout the day in my studio. But if that makes you feel better, you certainly could. Thank you. All right. We can turn the lights down. And again, I'm gonna kind of keep ... I'm gonna do my visual sweep, nothing flammable. I'm just gonna keep my solder pick and even my tweezers handy in case I kind of need to push things down a little. And because I'm sort of fighting gravity on this, I'm also gonna heat a little bit slowly. And most of my solder is kind of tucked up under these so it's a little bit hard to see. Hopefully, we've got a couple pieces. I see it wants to slide. Don't do that. Sometimes you just have to talk to your solder also. (laughter) When I was in undergrad, we would have a little ... I don't even know what it was, it was like our little solder god altar. And there was like a little statute with Dapt disc underneath. And if you were soldering something really tricky, you would like pay the solder god with a piece or two of solder before your started just to be on the safe side. (laughs) You know, whatever you gotta do to get the solder to flow. There's no wrong way there. Oh, come back. And if you gotta move solder that's escaped, you move solder that's escaped cause I don't wanna have to clean that up from the middle of my locket later. So, let's put that somewhere productive. Same thing over here. Let's move that guy back into place. And so, hopefully get some solder to flow. That guy went. I think we lost all our solder on that side. It kind of fell down a little. So, in this case, we may not have actual solder on this guy. I can't tell. No, there we go. We might have gotten it. If not, at this point we've kind of passed our point of no return. So, we'll go ahead and quench and pickle. You can turn the lights back up. Just cause there's potential for some steam to spit out, I wanna pickle that really slowly. Or quench that really slowly I should say. And actually, I'm gonna take my binding wire off over that just in case there's a ton of water that got stuck in there. So, moment of truth. Let's find out if that worked. Ta-da! (audience oohs and ahhs) So, we've got a little ... Everyone's like, "Wow, it worked!" So, we've got a little hinge now. So, that is another option for your locket. Now, in terms of clasps. I'm not gonna go ahead and pickle this cause I'm just gonna talk us through what we can do with our clasp here. And then we're also gonna come back and talk about a slightly different style of clasp for our tube rivet locket. So, what we can actually do with this one is use kind of a similar principal to this to do a clasp, but instead of actually soldering it down, what we can do is take wire and create a little loop or a little hook, and then solder another little piece in here. So, what that would actually look like. Let me grab some wire. I could take a smaller piece of wire here, thread that through, and a lot of times what you'll see is kind of a little shape that looks something like kind of this with a little loop on the end. And a little loop on the end. This is all gonna make sense in a hot minute. (laughs) I'm gonna cut off this excess. Hopefully, this is all gonna make sense in a minute. So, what we would do then, is actually if you guys can see this here, this would get soldered right at that point which we would file and fit and get nice. And then you can actually give this, if this was soldered together ... Let's just use our imaginations for a minute. We can actually give this a little bit of a pinch. It's a little bit awkward to do. So, if I pinch this guy in, and I pinch this guy in ... Nope, I wanna do it the other way My brain decided it couldn't figure out how to use these pliers that I use every day of my life. So, we can kind of give that a little pinch and it gives us a little loop here. Does that make sense? And then if we take another little bit of wire, we can form that into a little loop as well. And again, there's a lot of versions of this so you can kind of play around and make stuff up. But if I make a little tiny loop of wire ... So, I've made this little tiny loop, and if I cut it shorter. These are my old wire cutters. And they are definitely not as sharp as the new ones that I left sitting at home in my studio. So, we could make a little hoop here that gets soldered on. And then, this I pinched a little tight. But you can change that so that it would flop right over. Like a basic clasp. Does that make sense to everybody? Perfect. And any of this ... So, like this, if you needed to you could open this up to solder it. And you could actually use your cross-locking tweezers and your third hand to hold that little guy in place. Does that make sense when I say that? Perfect. All right. So, then the other thing, back to our first example here with our tube rivet, is you could certainly do a similar kind of clasp to that. But since this is something that slides, we can also do a little bit of a friction clasp. So, in order to do that I need to make this tab just a little bit shorter. So, what I'm gonna do here is come over to my bench pin. And I kind of pre-marked this just because I sort of had an idea of what I wanted to do before we got here. I'm gonna cut this piece just a little bit shorter but I'm still gonna kind of keep a little bit of a curve to it if can. All right, so I've got that guy cut there. And now what I'm actually gonna do, is I've got my lower flange that's a little bit longer. I'm gonna fold that over so it becomes a little spot for this to fix into. I'm gonna start with some nice flat pliers and kind of bend that up. I'm gonna leave a little bit of a gap cause I know I have to overcome the thickness of my metal. So, I'm gonna bend this over. And what this is gonna kind of look familiar is, remember, at the beginning of the day when we were just folding that all over and hammering it, yeah, we can do the same thing here. So, now that I've started this fold I'm gonna come in here. I might need to cheat it a little bit more. Let's see if I can get it on the edge. All right, so I can kind of come in here hammer this guy down. Start to sort of get it to fold over. And if it doesn't wanna fold with the hammer you can kind of push the angle a little bit more here. Then I'm gonna slide this guy back in cause I wanna make sure I've left room. It's getting a little crooked there. So, I'm gonna kind of pinch that. I'm gonna pinch slash hammer is basically the name of the game here. So, I'm just folding. I've had this worked so well in my practice sample at home. And now it doesn't quite wanna fold as well as it did. When in doubt, hit it with a metal hammer. There we go. Then you can kind of adjust the tightness. But you want this to sort of be ... You want it to be a little straighter than I made here in this one. (laughs) But the idea is that you want this to be pretty tight so it slides in, and just kind of clicks into place. So, all it is is like a nice little ... Again, try to make it a little neater than I made it. (laughs) But the idea is that it just slides in there. And then at this point with this one, you know, I would come in here, and I would trim off this little excess with my saw here. Just cause that's a little sloppy. I would probably do a little bit more trimming and filing of that so that it was nice and even. Obviously, this needs a trip in the pickle. And then it'll need a trip in the hyper pickle. So, I can kind of get it cleaned up and looking a little nicer. But that's the basic idea behind those two different types of lockets and the clasps. So, any questions about that? Yeah? Could you make a hinge similar to that Wonder Woman cuff bracelet? Do you think that would work for that? Yeah, so you could absolutely. The biggest challenge ... So, those of you who don't know what we're referring to, if you did not watch our bracelets class, in that class we talked about doing a folded hinge on a bracelet. The only thing with that kind of hinge that you sort of wanna keep in mind is you're having to make it a much smaller space generally for a locket. Unless you're making giant lockets which I 100% approve of. So, if you wanna make something that looks like Moana would be wearing it, like you're totally good there. So, that's the only thing. You kind of have to play with the scale. But you could absolutely do a bent ... So, basically what that means is you make a tab and then it gets bent around through an opening to make a hinge. So, you could do that as well.
Class Materials
Bonus Materials
Bonus Materials with Purchase
Ratings and Reviews
user-d7f7ae
After watching Megan solder in this class, I felt like it was something I could take on. There's a lot of soldering in this class! But there's also a lot you can do without soldering that's covered. I have a better understanding of how jewelry is made from this class. I'm looking at things that I own and thinking that I now know how to recreate them!
Silvia Rossi
I liked this course, Megan explains a lot of things about techniques and materials and it's simple follow all the operations to create these types of rings. I think I'd purchase other classes of her.