Prerequisite #1: Basic Metalsmithing Tools
Lesson 1 from: Explorations in Metalsmithing: Hollow FabricationMegan Auman
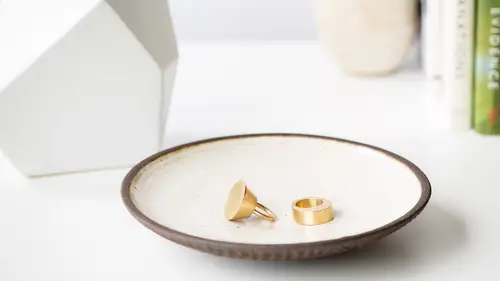
Prerequisite #1: Basic Metalsmithing Tools
Lesson 1 from: Explorations in Metalsmithing: Hollow FabricationMegan Auman
Lesson Info
1. Prerequisite #1: Basic Metalsmithing Tools
Lessons
Prerequisite #1: Basic Metalsmithing Tools
18:08 2Prerequisite #2: Tools for Soldering
14:21 3Prerequisite #3: Soldering Basics
21:14 4Class Introduction
07:42 5Design Considerations: Making Paper Models and Thinking Three Dimensionally
14:40 6Creating Non-Soldered Forms: Bending and Folding
18:38 7Creating Non-Soldered Forms: Dapping and Sinking
17:19 8Pendant Preparation & Soldering Basic Forms
22:56Creating a Soldered Cone
06:29 10Hollow Fabricated Ring: Sizing and Making the Internal Ring Band
09:05 11Hollow Fabricated Ring: Making the External Shape
37:59 12Hollow Fabricated Ring: Constructing the Ring Part 1
22:05 13Hollow Fabricated Ring: Constructing the Ring Part 2
38:06 14Hollow Fabricated Ring: Finishing the Ring
04:18 15Variations on the Hollow Fabricated Ring
05:02 16Building a Locket
08:06 17Making a Tube Rivet Hinge
11:45 18Creating a Hinge & Clasp from Tubing: Part 1
14:26 19Creating a Hinge & Clasp from Tubing: Part 2
21:32 20Adding a Pin Back to a Hollow Fab Form
14:32 21Finishing Your Hollow Fabricated Jewelry
07:59 22Turning Your Hollow Fab Projects into a Cohesive Jewelry Line
07:54Lesson Info
Prerequisite #1: Basic Metalsmithing Tools
Hey everyone, I'm Megan Auman; designer and metalsmith. And in this lesson, I want to show you guys all of the tools that you need to get started in metalsmithing. I know that one of the biggest misconceptions is that you need a ton of tools or maybe even a torch to get started, and that is totally not true. In fact, all of the projects that you see here were created using just the tools that I'm going to introduce you to in this lesson. Now, if you happen to purchase or RSVP for one of my hands-on classes, you will also get a PDF with links where you can buy all of these tools. But for now, I just want to show you guys so that you're really familiar and comfortable when you start working with them. I'm gonna show you some basic tools first and then I'll show you a few extra things if you want to dive in and get a little bit more creative. But as I mentioned, everything here you can create with just the tools I'm about to show you. So let's go ahead and get started. Now, the first thin...
g that you're gonna need is a saw frame. And this is really the most important tool for creating all of this work because it lets you cut out all of these shapes. Anything you can imagine you can do with a saw frame. Now, saw frames come in a couple of different depths. So this is a three inch saw frame, this is a four inch saw frame. And really the only difference is how deep you can cut into your metal. I think when you're starting out, unless you want to make something completely giant, and let's face it, you're probably not gonna make something any bigger than the earrings I'm wearing here, you can get away with a three inch saw frame. It's gonna give you a lot of control. So this is our most important tool, but it doesn't work without our saw blades. So saw blades are tiny. They come in usually these little packs of and they come in a lot of different sizes. So the way that our saw blades work is they're numbered. They go up from zero to, I don't know, something prety high like eight, and in those cases the higher the number, the thicker the saw blade. But they also go down from zero in something that's labeled one slash zero, which is actually pronounced one aught. Don't worry if you've never heard that before, but now you know. If it's one slash zero, it's one aught. If it's two slash zero, it's two aught. So from there they get thinner the further you go down. So an eight aught is gonna be much, much thinner than a one aught. Now, most of what you see here was created out of either 20 or 22 gauge metal. So we're working with a fairly thin gauge of metal here. And we'll talk about that more in the classes because choosing the right metal really depends on the project that you're doing. But for all of these kinds of projects, I usually recommend about a one aught saw blade. What you're looking for is something that's not gonna break too easily for you, but you also don't want it to be so thick that it's hard to make these really delicate shapes. So something like this, you want a thinner saw blade so that you've got room to maneuver. Now we're not gonna get into actually how to saw here but I do want to talk about how to put your saw blade into your saw frame so that you're not totally clueless. So we've got our saw blade here and you can't see this because it's tiny and actually quite frankly holding it up to my face, it's pretty hard to see as well. But if you run your fingernail down your saw blade, you can feel that it's directional. Our teeth actually point in a direction. And what I want are for these tiny little teeth to point down, which means when I run my fingernail across it, I'm not catching. If I were upside down, my fingernail would catch and it would do horrible things to my nails. So I'm gonna make sure that my teeth are pointed down and then when I'm putting it in my saw frame, I'm gonna make sure that they're also pointed out. So down and out. Then I'm just gonna go ahead and put this here into the top piece of my saw blade. Now if you're watching this and you've tried to saw in the past and you've broken a lot of saw blades, it's probably because you had the tension wrong. So before I tighten the second half, I like to make sure I've got a little bit of room here to flex my saw blade. So this doesn't hit the end of this piece. I've got about maybe a little under half an inch there. So then what I'll do is I'm gonna go ahead and I'm gonna lean on this a little. What I like to do if... Some people put them right against their sternum and that hurts. So I like to hold it in my hand and actually then push my sternum against my hand. Push this in here and get it nice and tight. If you feel like it's not tightening for you, we can our pliers, which we'll get to in a second, and just give it a tiny little turn. Now what I'm looking for is if I hit it with my fingernail, I've got this nice little high-pitched ping. That means we're all set up and ready to go. Alright, now to actually make your saw frame work, you are going to need a bench pin. So there are lots of different kinds of bench pins and in a jeweler's studio you might find that it's actually mounted in the table. But I like a clamp on bench pin because you can use it anywhere. So this is one example of a bench pin. It's got a nice little metal plate for it; saves you some time. The one thing with this one is we really want a V notched into out bench pin because that's going to allow us to get in and make those intricate cuts. So if you get a bench pin like this, you'll just need to take this to a band saw and put a notch. But I've got a second bench pin set up here on our table and you can see this bench pin, which is very inexpensive is also pre-notched and then just clamped right to our table. The most important thing when you're getting set up to saw is that you want to try and put your bench pin at a table so that you're sitting about chest height. And the reason for this is that we are actually going to saw vertically. I actually had someone tell me that the first time they tried to saw they were sawing like this. We don't want to do that. We're gonna hold this nice and vertically. And again, we're not getting into how to do that in this video but if you've got your bench pin mounted chest height, a counter, a bar, something like that. Or just make your chair lower. Now we're all set up and ready to saw. Now two more things that we're going to want for sawing. First of all, we're gonna want a lubricant. I like Bur Life. There's Cut Bur. There's all kinds of different things that you can use. Or in a pinch, I like to steal a bar of soap from my hotel room. So that'll work in a pinch, but these actually do work a little bit better because it's what they're designed to do. If you find that you're sawing and it seems like you're having to do a lot of hard work, just give this a little swipe and that's gonna be really easy. The other thing I always recommend for sawing are safety glasses. In a second we're gonna talk about drilling because sometimes we have to put holes in things, but I like to wear them also when I'm sawing because occasionally your saw blade breaks and the last place we want it is in our eye. So speaking of drilling. You'll notice that in some of these projects we have holes that are cut right out of the center. Even if you're not planning on piercing designs out of the center, you can see that these are all connected with jump rings and I had to drill a hole in those as well. So at some point you're gonna need to make a hole in your metal. Now the best thing to use is anything you can drill with and then actual drill bits. And these guys are tiny because we're drilling pretty small holes. But you can see I've got some drill bits here, right? Some nice, tiny little drill bits that are gonna do the sized holes that we need. So in order to use our drill bits we're either going to need a drill or something like a Dremel. So if you already have a Dremel on hand, you can totally use that. Or the other tool is a Flex Shaft, which is basically a fancy jeweler's Dremel. It's got a little bit more power and that's why people like it. So with this, I can simply mount my drill bit in here. Use my Chuck Key, tighten it up, and now I'm ready to drill. So when you drill with the Flex Shaft, even though it can be held at any angle, you always want to hold it vertically like a drill. And again, always with the safety glasses. So when I'm using my Flex Shaft as a drill, I like to just go ahead hold it vertically and you just want to drill into wood. Conveniently your bench pin is made of wood. So we can just drill that right in there. So when you're drilling, whether it's with a Flex Shaft, or a Dremel, or a drill, you will also need to make sure that you're center punching your metal. We need to make a tiny little divot in our metal in order to make that happen. So in order to center punch, you're gonna need a center punch, which is basically any kind of piece of metal that's ground to a point here. And the center punch gets hit with any kind of hammer and you're going to want to that on a steel block. So I would put my piece of metal that I wanted to drill, put my center punch and give it a little tap with my hammer. That's an essential step when you're drilling. So that's why you need these tools as well. Now that said, I'm all about getting you guys started quickly. So if you don't have a drill, or a Dremel at home and you don't want to make the investment in a Flex Shaft, you can also just get these little hole punch pliers. They're really inexpensive. They cost maybe six or seven dollars and you can use these to put holes in. And actually most of these holes truthfully were done with these pliers because it's so quick and easy. Now that said, they only work up to about 22 gauge. So if you're using heavier metal, you are going to want to find something to drill with. But if you're just getting started, and you don't want to spend 100 dollars on a Flex Shaft, these six dollar hole punch pliers will do the job. But with everything else that we're doing, safety glasses because little bits of metal could fly. Alright, so a couple more tools that I like to have on hand just for finishing and working. I usually keep just a raw hide mallet handy. It's great for bending, it's great for forming. Again, you don't need one but it is just a nice little tool that we can use to do a little bit of hammering. Once we've got our metal cut out, we will need to do some filing and some finishing. So in addition to your saw frame, we are gonna want to get a few files. I like a nice, big, half-round file. It's called half-round because it's flat on one side and half round on the other. This is great for going around our edges and really shaping our metal. You're also going to want to get a set of needle files. So they come in a lot of different shapes. This guy looks like a square. We've got a little flat one. Usually they come in a set of ten so you don't have to make decisions about this. But what these are for are for filing and cleaning up the inner shapes of our designs or any little details that we might have. So you'll need a set of those as well. Then additionally, you'll also want to have a few pliers, wire cutters, things like that handy. If you've already been doing any kind of wire work, you probably have these. I use my pliers a lot so I'm a big fan of these kind of fancy parallel pliers. You can see these are narrow. These are a little bit wider. Really what you're looking for in a good pair of pliers is that this little piece here is flat and not serrated. Because if it has those little ridges in it, it's going to mar your metal. So what I love about these is that I can use them to grip a piece of metal and it's not gonna leave any texture in it. I also like a pair of either round or these are round and flat on one side because they're great for bending wire and just making little curves. And finally, you should also pick up a pair of wire cutters. That's what we use when we make, say, jump rings and ear wires, and anything where we're cutting our wire. So a couple last tools that you're going to need. Here you can see I just like to keep some dowel rods in a variety of sizes. These are perfect for making jump rings. So all our little jump rings here made on a dowel rod. Or you can even use them to bend shapes like these cute little hoop earrings that we've got. So you can even make these hoop earrings with just what we're doing in this class. And finally, the last thing that you're gonna want is some sand paper. And this is what we're gonna use to finish our metal. This is gonna take that rough, scratched up metal that you've been working on and turn it into not super shiny, sand paper doesn't do that, but a nice, even matte finish. So in addition to all our basic tools for working, I also want to talk really quickly about design tools because when we're in this class I'm not just gonna teach you guys how to copy one of my designs from start to finish, I'm gonna teach you some design skills so that you can create earrings, necklaces, or whatever jewelry you want that matches your aesthetic and your design vision. So a few things that you're gonna want to have on hand are a ruler; always good to have. Really does not matter. Any nice straight edge ruler is going to do the trick for you. But I also like to have some dress maker's tape. Just something that's a little bit flexible. It's really great if you're working with wire. I like this kind that rolls up so that it's not a big mess of measuring tape on my bench. You're also going to want some tracing paper. And I realize some of us haven't used tracing paper in a while but in jewelry it has a really specific purpose because what you're gonna do is draw out your designs on tracing paper, usually with a Sharpie, and then we're going to rubber cement them to our metal. And that's what's going to allow us to follow along with a pattern as we're cutting. All of the jewelry that you see here can be made with just these basic tools. But now I want to go ahead and introduce you to just a few more tools that'll even help take your jewelry designs to the next level. So now I just want to show you a couple more nice to have tools. Again, everything I just showed you is all you need to create all of the jewelry that we've got here. But a few more little things that you might want. You can get yourself a sheet and wire gauge. So this guy is just really helpful if you've got different gauges of sheet and you don't remember. This will actually measure them for you. Handy little tool to have. A few other things that you might want are a ring clamp, which is perfect for holding small pieces. You can see I can put this guy in here, clamp it up, and now I don't have to hold it with my hand. I can hold this nice thing. Great for filing edges, finishing, things like that. So the other thing that you may want to get are these little things called cup burs. And I know it's really hard to see, but in here the reason they're a cup bur is because we've got a little hollowed-out shape. And what they do is that they actually ball the ends of wire. So if you can see here on an ear wire, we want to give it a nice rounded edge. And you can certainly do that with your files but the cup bur works much faster. So what we do is we just take one of these cup burs, we mount it in the end of our Flex Shaft. You can see here we just run the edge here and it's gonna round our edge really quickly and we're done. The other thing that you may want to get if you've invested in your Flex Shaft, is there are all kinds of different little wheels; buffing wheels, finishing wheels, polishing wheels that you can get. So if you get a Flex Shaft, you can start to dive in and find some of these things, which will make it so that you don't have to necessarily manually sand or finish things. Now, speaking of finishing, the other tool that you may want to have is a tumbler. Now we don't have one here because I flew from the other side of the country and I was not about to bring one. But you can see from this image that this is what a tumbler looks like. If you think about those old rock polishers when we were kids, same thing. There's a couple different styles but they all work the same way. So basically what a tumbler does is it mass finishes your piece. So in our barrel we can put different kinds of media. The green that you can see is actually plastic so it gives you more of a matte finish. So you can use it for a nice, soft, matte, easy finish or, more commonly, people use steel shot. And what steel shot does is it gives you this really nice kind of shiny finish without having to do a ton of polishing. So this cuff bracelet here, that was finished with the tumbler. So that's a great tool to invest in if you're doing a lot of work because not only does it make it shiny, but it also work hardens. So sometimes your metal is gonna be really soft. You could see that if I hadn't work hardened this, it would want to kind of bend right here at this spot. So by tumbling it, now it's work hardened. I don't have to worry about it bending where it's not supposed to when I use it. Alright, a couple more just little things that you might want are some forming tools. So you can get mandrels. I have a wood one because metal ones are really heavy to carry in your suitcase. But I have a wood one and this is actually for bracelets. So I can take my flat bracelet, take my raw hide mallet, bend it right around here. They also make mandrels for rings. So if you're shaping rings, you can buy mandrels for these as well. And one last little thing if you are working with copper, or brass, or bronze, which are metals that can tarnish over time, you may want to get something like Renaissance Wax and that's gonna seal and coat your metal so that it doesn't tarnish. So that's it. That's really all you need to get started. So now that you've got your tools, if you want to learn how to take those tools and turn them into projects just like this, make sure you turn into all my hands-on classes here on CreativeLive.
Class Materials
Bonus Materials
Bonus Materials with Purchase
Ratings and Reviews
user-d7f7ae
After watching Megan solder in this class, I felt like it was something I could take on. There's a lot of soldering in this class! But there's also a lot you can do without soldering that's covered. I have a better understanding of how jewelry is made from this class. I'm looking at things that I own and thinking that I now know how to recreate them!
Silvia Rossi
I liked this course, Megan explains a lot of things about techniques and materials and it's simple follow all the operations to create these types of rings. I think I'd purchase other classes of her.