Making a Tube Rivet Hinge
Lesson 17 from: Explorations in Metalsmithing: Hollow FabricationMegan Auman
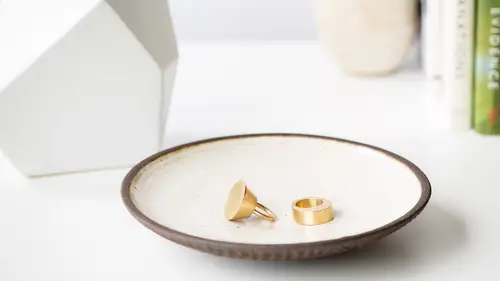
Making a Tube Rivet Hinge
Lesson 17 from: Explorations in Metalsmithing: Hollow FabricationMegan Auman
Lessons
Prerequisite #1: Basic Metalsmithing Tools
18:08 2Prerequisite #2: Tools for Soldering
14:21 3Prerequisite #3: Soldering Basics
21:14 4Class Introduction
07:42 5Design Considerations: Making Paper Models and Thinking Three Dimensionally
14:40 6Creating Non-Soldered Forms: Bending and Folding
18:38 7Creating Non-Soldered Forms: Dapping and Sinking
17:19 8Pendant Preparation & Soldering Basic Forms
22:56Creating a Soldered Cone
06:29 10Hollow Fabricated Ring: Sizing and Making the Internal Ring Band
09:05 11Hollow Fabricated Ring: Making the External Shape
37:59 12Hollow Fabricated Ring: Constructing the Ring Part 1
22:05 13Hollow Fabricated Ring: Constructing the Ring Part 2
38:06 14Hollow Fabricated Ring: Finishing the Ring
04:18 15Variations on the Hollow Fabricated Ring
05:02 16Building a Locket
08:06 17Making a Tube Rivet Hinge
11:45 18Creating a Hinge & Clasp from Tubing: Part 1
14:26 19Creating a Hinge & Clasp from Tubing: Part 2
21:32 20Adding a Pin Back to a Hollow Fab Form
14:32 21Finishing Your Hollow Fabricated Jewelry
07:59 22Turning Your Hollow Fab Projects into a Cohesive Jewelry Line
07:54Lesson Info
Making a Tube Rivet Hinge
So then let's talk a little bit about how to do some different kinds of hinges. We're gonna start with what should be a fairly easy hinge. Which is think of using a tube rivet as a hinge. So, what's nice about a rivet is if we only use one it acts as a pivot point, and the reason I recommend a tube rivet as a hinge instead of a regular rivet made out of a piece of wire is twofold: one, it's a little bit more surface area on the rivet in terms of your pivot point so it's actually a little bit stronger. But two, it automatically gives you a hole where now you can hang the locket from it. So it's like two birds one stone. So, what I'm going to do here is as I said, you can do this with two halves that are domed just to make our life easier I'm going to go ahead and do this just with a flat sheet that I've cut essentially to match, and if you were paying attention you'll notice, again, I like to write on my metal so I know what's happening. (laughs) So I labeled this. This is the inside. T...
his is the rivet side. This is my catch side. So, what I'll do just to make my life as easy as possible, and actually, I'm going to put an R on this side and an R on this side so that I remember that that is in fact the side that my rivet is going on. So what I'm going to do now is I'm going to come back to my favorite tool, my painter's tape, and I'm actually just going to tape this guy together so that it can't move. So, I'm just going to throw some tape on here. And I've got a little case where this is not perfectly the same size. My outside ring, or not ring, but my outside flat piece is a little bit bigger than the piece that has the dome on it. I'm not so worried about that because if I need to once this is all together and my rivet is set I can actually go ahead and saw or file that down. I can clean it up if I need to. So, I'm just throwing a whole bunch of painter's tape on here so that hopefully it doesn't move. You can also see here the same thing. This one is a little bit bigger than that one. It's fine. I'm gonna get my rivet set, and then I can come back in there with my saw and clean it up. Alright, so, because this side is smaller it would definitely be easier to drill from this side. But I want to make sure that I'm centering it in the smaller piece not the bigger, so I'm going to work from the wrong side. It'll still work for me. So, the first thing that I need to do is obviously, drill a hole for my tube rivet. So, for starters it means I have to pick a size tubing. So I've got some brass tubing, and there's no rule that says that you have to use tubing that's the same materials as what you're using. So, if you want to do an accent you could certainly put a sterling silver rivet or a copper rivet or whatever you wanted in there. If you wanted it to contrast instead of matching. So I've go a drill bit here that's pretty close to the size of my tube rivet. But what I'm going to do is I'm actually going to drill a smaller pilot hole first, just because I don't want to have to go through all that metal with this big drill bit. So, first things first, I'm going to center punch this guy if I can find my center punch. There we go. So, again any time we're drilling we always want to center punch first, and I do not recommend for doing rivets, I don't recommend our friend the whole punch pliers because they're not designed to go through two thicknesses of metal. They're really only designed to go through one, and when you're doing rivets you need to drill through everything together so that it's perfectly lined up. So, like I said, I'm going to drill a smaller pilot hole first. And it's just because that rivet is just a slightly bigger piece and I don't want to take that much material out. It kinda makes me a little bit nervous. It just wants to catch, so I just drilled that little hole. Now I'm actually gonna go in. Honestly if I wasn't using a flux shaft at home I might actually have a real drill press. And my real drill press I would probably just drill it. It's not such a crazy-big hole. But the flux shaft always makes me a little more nervous for drilling probably because I was always trained in studios that had cute little jewelry drill presses, and they were like, don't use the flux shaft for drilling. Use the drill press! So it always has made me a little nervous. I'm just checking to make sure that's in there nice and even. So I, you know, wanna kinda hedge my bets when I'm drilling. (light drilling) Alright, perfect, so that is drilled. So now our next step with a tube rivet is to actually cut our tubing, and this is where it gets a little bit tricky, because we're cutting a pretty tiny piece. So, I recommend about one and a half times the thickness of you metal. So that means this is pretty teeny tiny here- what we're gonna cut, and you can certainly use a tube cutting jig which is this fancy little tool here to actually put this in and cut, but the thing with the tube cutting jig is they're kind of expensive and they're such a specialty tool You can totally do this without it. So, our frame is not in, and my saw blade is not in my frame. Come one! Oh, there goes our table. Alright, now we can cut. So, I'm just going to come in here. I'm keeping this fairly short. (light sawing) And like I said, if you were in our class before I like to keep a finger on this. (light sawing) So that, up, I dropped it on the ground anyway. I'm not even gonna try to find that. I'm just going to cut a new one. I can see it. Okay, I can't so one of you can come pick it up. That could actually be our one from yesterday, too. Maybe not. Nope. We're just gonna cut a new one. It's usually not worth it. The only thing that's worth digging for in this studio when it's that tiny and you drop it is a gemstone or a piece of gold, and in both of those cases your best trick is to get out the dust pan. You're never gonna find it by looking. As soon as you start sweeping, there it is. Alright, take two. (light sawing) It did it that time. Didn't even try to pick up my finger, just slid it along. Alright, so for a tube rivet we want to actually do this in our vice so that we can flare it. So, what you need are actually two things that flare. So, center punches especially fat center punches like this, work really well, but the other thing if you did happen to get one of our nice sets of dapping punches, one of these small dapping punches also works really great for flaring a tube rivet. So I'm actually going to- where did our piece go? There it is. I'm actually going to use that. And because this time I'm not gonna be stubborn, someone come up here an do a little holding for me. Who wants to be brave? Just come on up. Who's got steady hands? (laughter) So what I'm going to ask you to do, is once I get this slid in here, and hopefully we can do this. We're kind of standing out of the way. I'm going to ask you to just hold the locket itself, but I have to move this 'cause we're not the point perfect. So if you could just hold that in there. Come on. Great, so you just hold. It's like sticking in my finger. So I'm just holding that part. Yeah, so you're just kind of holding the whole locket steady because there's a lot of material, and I'm just going to wiggle this up a tiny little bit. So what I'm doing now, I'm just going to grab whatever hammer I can find. And I want to start to flare out our rivet. So, I'm just hitting on the point. (light tapping) And on the ball pean here. (light tapping) And actually hold on a sec I'm just going to flip this, it's still going to fall out so let go of that for just a second. Put that one there. Alright. Actually, I think were good. I'm gonna let you sit down now. Hopefully, if I just spin that- there we go. I was like, I know there's a way to do this in one hand. (light tapping) So, really the most complicated part of this is just getting it flared enough where it's not going to fall out any more. So, you can see here now we're starting to get this guy flared out, or even if it kind of slips it's not falling out of our hole any more. (light tapping) So, my goal in this step is that I'm actually just trying to spread this out. Now I can come back in here to my steel block, and I want to kind of keep this centered on here, so I'm going to add some little stackers just to give me a little space. You can see how it actually is flared out a little bit now. So now I can come in and start to hammer my edges down. And then I'll flip this and I can actually work on the edge here, let's just do that. (light tapping) Flip that around, and then I'll come back and just kind of work from side to side. (light tapping) Until that's kind of looking pretty nice in there. When you do it right it looks really good. When you drop it on the floor and loose it it doesn't really work. So now if we take this apart. I'm really aggressive in my taping. Now you can see we've got a little locket based on that hinge there.
Class Materials
Bonus Materials
Bonus Materials with Purchase
Ratings and Reviews
user-d7f7ae
After watching Megan solder in this class, I felt like it was something I could take on. There's a lot of soldering in this class! But there's also a lot you can do without soldering that's covered. I have a better understanding of how jewelry is made from this class. I'm looking at things that I own and thinking that I now know how to recreate them!
Silvia Rossi
I liked this course, Megan explains a lot of things about techniques and materials and it's simple follow all the operations to create these types of rings. I think I'd purchase other classes of her.