Finishing Your Hollow Fabricated Jewelry
Lesson 21 from: Explorations in Metalsmithing: Hollow FabricationMegan Auman
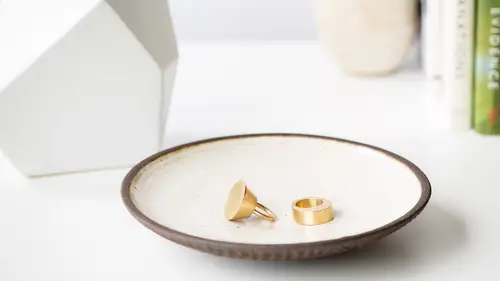
Finishing Your Hollow Fabricated Jewelry
Lesson 21 from: Explorations in Metalsmithing: Hollow FabricationMegan Auman
Lesson Info
21. Finishing Your Hollow Fabricated Jewelry
Lessons
Prerequisite #1: Basic Metalsmithing Tools
18:08 2Prerequisite #2: Tools for Soldering
14:21 3Prerequisite #3: Soldering Basics
21:14 4Class Introduction
07:42 5Design Considerations: Making Paper Models and Thinking Three Dimensionally
14:40 6Creating Non-Soldered Forms: Bending and Folding
18:38 7Creating Non-Soldered Forms: Dapping and Sinking
17:19 8Pendant Preparation & Soldering Basic Forms
22:56Creating a Soldered Cone
06:29 10Hollow Fabricated Ring: Sizing and Making the Internal Ring Band
09:05 11Hollow Fabricated Ring: Making the External Shape
37:59 12Hollow Fabricated Ring: Constructing the Ring Part 1
22:05 13Hollow Fabricated Ring: Constructing the Ring Part 2
38:06 14Hollow Fabricated Ring: Finishing the Ring
04:18 15Variations on the Hollow Fabricated Ring
05:02 16Building a Locket
08:06 17Making a Tube Rivet Hinge
11:45 18Creating a Hinge & Clasp from Tubing: Part 1
14:26 19Creating a Hinge & Clasp from Tubing: Part 2
21:32 20Adding a Pin Back to a Hollow Fab Form
14:32 21Finishing Your Hollow Fabricated Jewelry
07:59 22Turning Your Hollow Fab Projects into a Cohesive Jewelry Line
07:54Lesson Info
Finishing Your Hollow Fabricated Jewelry
Lastly let's talk just a little bit more about finishing. So I'm not going to belabor kind of the point of finishing because if you've been in any of our other classes pretty much everything we've learned about finishing still applies. So if you want to put a patina on it, you can put a patina on it. Generally the first thing that you wanna do with any of these, again we talked about with our hollow-fab ring, that we want to pickle it if it's brass and it's kind of a funky color then we want to hyper-pickle it. So you want to do all of those kind of finishing steps, and then you can go through all our traditional sand paper steps. So we can start with whatever we need on our hollow-fab rings. Where we've got a lot of file marks we probably need to start with our 150. And remember sandpaper, the bigger the number the finer it is. So with something like your hollow-fab ring where you're doing a lot of cutting around it, you're probably gonna need to start with and work your way up. With...
something like our locket where maybe we didn't have to do as much filing, on this I could probably get away with starting, except for here where I have to file off all my excess solder that I said I shouldn't put on there, I might start more with 400 on this side. Maybe just use my more aggressive sandpaper on here to get my file marks out. Then just like we've talked about in any of our other classes, you know you can think about do you want it to be matte or do you want it to be shiny. So, there's a couple of different ways to get a matte finish. One of them is to just take your sandpaper up until it's whatever finish you want. Most of what I do is a combination of sandpaper finishing. Let me get out my bag of polishing and finishing tricks here. So most of what I do is just a combination of sandpaper finishing and then our micro finishing papers. So with our example ring here all I did was I worked my way through a couple of sandpapers and then this is also great if, I'm looking for some scissors here, if you can see our brass gets a little dirty, I can come back in here with my microfinishing papers. So this one's a little bit more aggressive then what I have on here but I can use this. Kinda come in, maybe clean off some tarnish. So this is gonna give me a more matte finish. And then as I work my way up through, just like with our sandpaper, these micro finishing papers, and these are linked on that pdf, I love them so much I put the link on 'cause I basically use them to finish everything. I think they're magic. I don't know, I think we all end up finding our ways of finishing that work best for us and for me it's always these papers. I just kind of use them all the time. So then as I go through finer and finer papers you can see it gets a little bit shinier. And the nice thing about thinking about hollow fabrication is you can actually treat every surface differently if you really wanted. So this is kind of started just from hanging out in the studio for the last couple of days. It started to tarnish a little bit but I can actually see there's a really interesting thing happening where this is a little bit deeper and then this is starting to get a little bit shinier, like I'm almost starting to get a little contrast on there. So I could actually push that to my advantage if I wanted. I could give this a little bit of patina and then clean off maybe just the front surface, or clean off part of it and start to play with a little bit of that contrast. So, this is a really great finishing option. For a lot of people, like I said, I like a matte finish 'cause it's a lot easier to upkeep. Shiny is hard to keep Shiny. If you really want something to look super shiny, there are a couple things to thing about. You can use things like buffing wheels or the flex shaft. So I think, I knew we had some. You can get these little tiny buffing wheels. I have those, I have these somewhere. I have these kind of bristle disks that you can put in the flex shaft. We talked about these in the statement earrings class, they can work it up to a slightly shinier finish. If you go to Rio Grande or any jewelry supplier, you'll find lots and lots of different options for ways to make things shiny. You can also, even if you've just worked your way up to pretty fine with micro finishing papers, this is something called a Sunshine polishing cloth. And I believe Sunshine might be spelled differently because it's a brand name, but it's basically just a little polishing cloth. So you can see if I put this on here it gets a little bit shinier even still. So, even just hitting it with that polishing cloth it's not a true high polish because we can see all the matte texture in there, but it gives it just a nice little shine if that's what you're after. And you can buy this from Rio Grande. And actually if you sell things that are high shine, you can get little, they call them like single serve versions of these that you can actually tuck into orders for your customers. So it's a nice way if you have something that's shiny or something that tarnishes and you want to give your customers an option to clean it. You can buy "individual servings," of these to hand out with orders. I mentioned this before but I think it really bears repeating, we've talked a lot in other classes about the tumbler and I don't recommend the tumbler in hollow fabrication. One of the reasons for that is just if you have any kind of big hole So let's say I decided I was gonna throw this locket in here, into the tumbler, and for some weird reason, and weirder things have happened when you're bouncing around in media, let's just say I had it closed, clasp comes open, a little bit of shot gets in there, somehow closes again, now that shot wants to ding from the inside. It could actually distort your form. So I don't recommend using the tumbler for that reason that even on something like this, you could cause damage to the form. So I think for things like your hollow-fab, it's really better to hand finish them. The other thing is that most of your hollow fabrication, because of the warp you're putting it through, doesn't need to be work hardened in a tumbler like a lot of other stuff does. So even though this ring has been soldered a bunch of times, it's technically annealed metal, it's thin, it's 22 gauge, this is a really strong, sturdy ring. So it doesn't need the work hardening of a tumbler, it's going to be perfectly fine for everyday wear. So generally if you're spending all this time on hollow-fab take the little extra time, do your hand finishing or do your flex shaft finishing. Don't try to stick it in the tumbler. The other thing that's important to note is of course that any metal containing copper, which is copper, brass, bronze, even sterling silver, will oxidize or tarnish over time. So you may want to decide to actually seal these. I made the decision on these couple of rings not to seal them and I've just been sort of cleaning them back off. It's not a lot of surface so it doesn't bother me. And some people don't like sealing things. But if you do want to seal, and if you're sending them out into the world it's probably better to seal them, 'cause not everyone's customers wanna have to clean their jewelry all the time. I don't mind doing it but of course I pretty much clean jewelry for a living right. So, the two that I recommend, and if you have been in any of our other classes, these are gonna seem really familiar to you, Renaissance wax, which is a wax you just buff on, kind of buff off, or the Sculpte Nouveau clear guard. Comes in spray, it comes in paint, I think the spray is easier, and it comes in a low VOC version so you can not stink yourself out of your studio. It's worth the extra dollar for that. But really again, any of the finishing techniques you know or are familiar with, you can definitely apply to your hollow-fab projects.
Class Materials
Bonus Materials
Bonus Materials with Purchase
Ratings and Reviews
user-d7f7ae
After watching Megan solder in this class, I felt like it was something I could take on. There's a lot of soldering in this class! But there's also a lot you can do without soldering that's covered. I have a better understanding of how jewelry is made from this class. I'm looking at things that I own and thinking that I now know how to recreate them!
Silvia Rossi
I liked this course, Megan explains a lot of things about techniques and materials and it's simple follow all the operations to create these types of rings. I think I'd purchase other classes of her.