Choosing the Right Metal for Your Statement Earrings
Lesson 4 from: Foundations in Metalsmithing: Statement EarringsMegan Auman
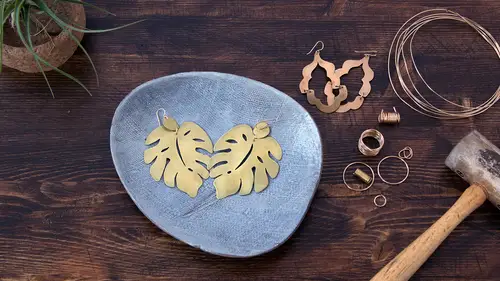
Choosing the Right Metal for Your Statement Earrings
Lesson 4 from: Foundations in Metalsmithing: Statement EarringsMegan Auman
Lesson Info
4. Choosing the Right Metal for Your Statement Earrings
Lessons
Prerequisite #1: Basic Metalsmithing Tools
18:10 2Project Overview: Statement Earrings
07:55 3Designing Your Statement Earrings
24:03 4Choosing the Right Metal for Your Statement Earrings
16:12 5Transferring Your Earring Design to Your Metal
10:39 6Sawing Basics: Putting the Blade in the Saw Frame
10:54 7Sawing Basics: Bench Pin Setup and Hand/Body Position when Sawing
13:04 8Troubleshooting & Student Hot Seat
10:18Drilling Holes and Cutting Interior Shapes
09:11 10Drilling Holes for Jump Rings and Ear Wires
04:22 11Proper Workflow for Cutting Out Your Statement Earrings
30:02 12Finishing Your Metal: Filing the Edges
09:46 13Finishing Your Metal: Sanding the Surface
18:40 14Finishing Your Metal: Choosing a Finish and Polishing
08:23 15Finishing Your Metal: Sealing Brass and Copper to Prevent Tarnish
05:27 16Making Jump Rings to Connect Your Metal
06:31 17Making Ear Wires
09:05 18Assembling and Evaluating Your Statement Earrings
13:34 19Alternative Step: Soldering a Post onto Your Statement Earrings
14:16 20Adjusting your Workflow for Soldering & Hot Seat
08:46 21Taking Your Earring Design to the Next Level
06:13Lesson Info
Choosing the Right Metal for Your Statement Earrings
So now that we have our design, let's talk about choosing the right metal for your statement earrings. Because there are lots and lots of options as well here. And so, for me, one of the things that's really, really important is that you guys feel comfortable making these decisions when we're not here. I could tell you, "Hey, go buy a sheet of 24 gauge brass, and you could make a pair of earrings," but that's not going to serve you well in the long-run, right? So I want to help you guys understand a little bit about the different kinds of metals, and why you might choose one over the other. So, first let's talk about the kinds of metals that we're actually talking about. So, traditionally in jewelry making, what you'll find is that you're dealing with non-ferrous metals. And non-ferrous just means does not contain iron. If you know anything about chemistry, I believe iron is FE, which is from Latin, I think. I'm going to look to Tawney, because she's scienc-y. Right? So yeah, basically...
non-ferrous means does not contain iron, so we're not dealing with steel, we're not dealing with iron, we're dealing with other types of metals. So, the most common non-ferrous metals that you're going to see for jewelry are: brass, bronze, copper, sterling silver ... You may start to hear this term "argentium silver" thrown around, so argentium silver is something that's just come on the market fairly recently. It's basically a type of silver that has a slightly different content in terms of what's in it, and it doesn't tarnish as much. So actually, the earrings that I'm wearing are made of argentium silver. They're a little bit whiter, and they don't tarnish. And then, of course, gold is a non-ferrous metal, very typical for jewelry. You're probably not going to use gold for this project, but it is an option. And then you might also hear of something called "gold filled," which is actual gold over a coating, usually of brass. Right? So it's layered together. So that's an option as well. So, really, there's a lot of different choices, and I want to show you guys kind of what some of these look like, but the thing to understand is that most metals are not pure metals, they're actually alloys. So, an alloy is when you take a pure metal and you add another metal to it and create something specific. So, copper ... I'll actually show you guys some examples here. Hopefully we can see the difference. So, copper is actually going to be closest to a pure alloy. Most copper is usually 99 point something percent copper. Right, and if you know what a penny looks like, you know what copper looks like. But then we have brass and bronze, and brass and bronze are actually both alloys of copper and other metal. So one has tin in it, one has zinc in it, and that's what makes it yellower. Because they're alloys, what you actually get is a huge range of colors. So, you can see here ... I've got ... This is pretty traditional brass in terms of what the industry would define as brass. It's very, very yellow. You might also hear a term called "nu gold," or "jewelers brass." You can see this is still technically brass, but it's actually a much warmer color. It's going to look a little bit more like actual gold as opposed to the very ... Like, you don't ... You think that brass is pretty gold looking until you put the nu gold against it, and then you can see it's a little bit different. And just for anyone who's doing a Google search, nu gold nu is spelled N-U. I don't know why, it's just how it's spelled. So, if you're looking for that ... And then you have bronze, which is actually warmer than even nu gold, and bronze personally is my ... One of my favorite metals to work with, and it is also the most frustrating alloy, because every time I order bronze, I swear it's a different color, right? So this ... I believe this sheet is also bronze, and this one starts to look a lot more copper-y. So, just heads-up with bronze, when you order it, you may or may not get something that's a little bit different. But so ... And then our other option, of course, is that you can work with silver, and this is a piece of, I believe argentium. So, one of the things to keep in mind is that you probably don't want to start with silver, because it's a little more expensive. It's not horribly expensive, especially when we're buying thinner gauges like we're going to talk about. But, I would recommend choosing something from brass, bronze, or copper, just to do your first project in, and we'll talk more about that in a minute. I also want to talk just really quickly about some metals to avoid, and there's two that I want you guys to just throw out, and the first one is nickel. Now, technically nickel is a non-ferrous metal that's used in jewelry, and people use it because it has a silver color, but it's cheaper than silver. But, having taught many a student who wanted to use nickel because it looked like silver, I do not recommend it, because it is a bear to work with. It's very hard. It does not saw well, it does not solder well, and a lot of people have nickel allergies, so a lot of people can't even wear it. So, it's one of those where if you really want a silver color, just bite the bullet and buy silver. At the time we're filming this, silver is actually very inexpensive right now, I can't promise you that if you're watching it in the future, but for now, silver is fairly inexpensive. The other metal that you want to avoid is aluminum. And the reason you want to avoid aluminum is that it's actually a contaminate for all of your other metals. So, aluminum melts at a much lower melting temperature than anything else we're talking about here. And while, if you're not using a torch, it's not super critical. What happens is even if you get a tiny little bit of aluminum, like a little filing on a piece of silver, and you go to say, heat up your silver, it's going to melt a hole right through it. So, any tool that you use that touches aluminum can never touch anything else. So, in theory, aluminum would be great for earrings, because it's a really lightweight metal, but because it's a contaminate, we don't want to use it in our studio. So if you're going to work with aluminum, that's its own thing, its own set of tools, you want to kind of treat it like quarantine. Alright, so, really it's just better to avoid that. Alright, so let's talk about actually choosing the metal for your project. So, you have a couple of choices, and the first one is just straight up color preference. Right? You might like bronze, or you might like nu gold over brass, or I kind of personally happen to really like the yellowness of the more industrial brass better than nu gold, because I think it's kind of fun. So just, what color do you like? Do you like the copper, do you like the silver? And that's a totally valid way to choose your metal. I think this color's pretty, I want to work with it. The same thing when kind of thinking about aesthetics. I think certain metals tend to feel more towards one aesthetic than another. Silver generally feels kind of sleeker or more modern, unless we're doing something like oxidizing it, and then it can look a little bit more, maybe Boho or a little bit more rustic. Copper tends to generally look more rustic than brass, again tends to look more modern, so you can think about what vibe are you going for? If you're using a really geometric design, you're probably not going to cut it out of copper, because the two just don't always seem to go so well together aesthetically, right? You're probably going to cut that really geometric design out of brass or silver. And then, of course, cost is a concern. So, brass, bronze, and copper are all fairly affordable. You can get a small sheet of any of those for, you know, 10, 20 bucks depending on size, so there's really no affordability cost between those metals. Silver is going to be more pricey, so you want to think about, you know, is that an investment you want to make? Again, I recommend learning on brass, bronze, or copper, and then once you've kind of got the hang of it, then you can get your silver. The other thing is malleability. So, that's a fancy word for saying how easily you can bend the metal. Some metals are softer than others. So, copper is very soft, and silver is generally very soft. And fine silver is the softest, argentium silver is the next softest, sterling silver is a little bit harder, but they're all softer than brass and bronze. And the reason we care about that, is if you're cutting out a lot of little detail, you want to make sure that the piece is not going to bend when you're done, right? So, if I have this piece here, and it's thin gauge and it's got a lot of little detail, I don't want to have to worry about, like, is it going to bend or smush, and so something like bronze or brass is going to be better for this than copper, because copper is going to stay really soft. Now, there are ways to work-harden it, and we can talk about that later. You can throw it in a tumbler, and that's going to tumble it up and make it a little bit harder to bend, but in general, if you've got a lot of detail, or a lot of little pieces, you want to stick with your harder metals like brass or bronze rather than say, your argentium silver or your copper. And then, finally, upkeep. So, certain metals tarnish, and you have to think about is that something that you want to deal with? Now, you can seal things to keep them from tarnishing, and we'll talk about that a little bit later, but in general, any metal that contains copper is going to tarnish overtime. So, copper's going to tarnish over time, brass, because it's an alloy of copper, it's going to tarnish over time, and bronze, because it's also an alloy that contains copper, will tarnish over time. And some of them will tarnish fairly quickly, depending on the climate that you're in, the humidity level, things like that. So, you may find that you like the look of the raw metal, but you end up having to clean it back a lot. That's why a lot of jewelers are switching to argenium silver, because it's engineered to not tarnish as quickly. Sterling silver contains copper, which is why it tarnishes too, over time. So then, our other consideration, besides ... Once we've chosen our type of metal, is we also have to pick our gauge of metal. And gauge is simply a way of saying "metal thickness." And you will often see gauge abbreviated as GA. So if you see 22GA written somewhere, that's your metal gauge. So, metal gauge is a little bit backwards, so the smaller the number, the thicker the metal. So, a 14 gauge metal is going to be very thick, a gauge metal is going to be very thin. So, for your statement earrings, you really want to choose the thinnest gauge metal that still allows for structural integrity, and what I have found is that somewhere in the 22 to 24 gauge is where you want to be. And it's almost sort of backwards, like, the bigger the earring, probably the thinner the gauge you're going to use, because again, we're trying to deal with that weight. So, when I'm cutting out these really big shapes, I want to use 24 gauge, but you'll notice I'm also using brass, because it's a harder metal, right? So, I can use 24 gauge brass, and it's actually ... Its got a little bend to it, but it's not going to like, smush. But, if I'm doing something a little bit smaller with a little bit more detail here, like this, the piece is fairly small, so I was able to use 22 gauge. 24 would have felt a little bit thin. So, at the end of the day, it's kind of a judgment call, but I would say, if you're planning on working really big, go with 24, if you're going to keep it a little bit smaller, in my world these are small earrings, right? If you're going to keep it a little bit smaller, then I would go with 22. So, then we have to talk about actually, how to purchase your sheet metal, so where does it come from? So if you guys RSVP'd for this class, you got a supply list, where I mentioned a couple of different vendors. But, depending on the type of metal that you're buying, it's either going to come in standard sizes, or you're going to order it to size. So, something like ... I believe this is nu gold, this is our bronze. A lot of times you'll see things come in like, a 6 by 6 inch sheet, or a 6 by 12 inch sheet, or even a 12 by 12 inch sheet. Obviously if you are not in the US, your standards are going to be a little bit different. But, you'll typically find that it's not like you can buy brass or bronze for a specific size to your project, you're just going to get a big sheet of it, which is perfect, because you guys are practicing. I do not recommend buying anything bigger than a 6 by 12, because you've probably bought a small saw frame, and you can see what happens as we're cutting in, we're cutting in ... Boom. Right? So, I can't get very far into this. 6 by 12 works, because if I've got this three inch deep saw frame here, I can get in from either side, which means I can probably get my piece to cut out. If this was 12 by 12, now I'm starting to awkwardly cut into corners, and of course, if you do buy bigger sheet metal, you can buy deeper saw frames, but then you have to sacrifice some control. This is easier to control when you're cutting than something that's like, this deep, right? So, I would not order anything bigger than about a 6 by 12 if you're ordering your sheet. Now, silver comes in much smaller dimensions, so I like to buy my silver from a place called Rio Grande, but there's lots of other suppliers, and that usually comes by the inch, so I believe this is ... You can get whatever this dimension is, three inches by an inch, two inch, three inch, four inch, five inch. So, the best thing to do when you're ordering silver is actually sit down, get your design figured out, figure out the smallest amount of metal that you possibly need to cut your design, and then order what you need. The other thing that you want to do when you get your metal in is that you always want to mark it with the gauge. So, when you get your metal in, typically it's going to show up just like this guy, right? It's not ... Well, this has markings, cause I drew on it. It's not going to have any markings, and then suddenly you're going to be in your studio, and you're going to be like, "What? What was this one?" Now, there is a handy tool that you can get, it's called a sheet and wire gauge, and it literally just slides on, we've got some numbers here, so if I put this on, this look like ... And usually what you'll find is that it's the one that fits kind of snugly. So this, it looks like is ... 22 gauge here. So this is 22 gauge, so I know that, even though it's a little tight, I happen to know that it's 22, because ... It's not 21, they don't sell them in odd numbers, so ... Technically it fits in my 21, but I know it's 22. So, you can check this, but if you don't have one of these, the smartest thing to do is when your metal comes, just label it. 22 gauge. And if you really want to be sure, you could say ... Let's see, what is this? This is our nu gold, so I might say, "22 gauge ... ... nu gold." And if I really want to know things, and this is a lesson I've learned after digging out piles of metal, and then trying to remember where I bought them, I might also write that I ordered this from Rio, because sometimes I buy my metal from multiple places, and then I'm like, "Oh, I really liked that color. Was that Rio, was that McMaster Carr, was that?" So, the more you can label, the better, and of course, if you're cutting off of this sheet, I always work from the non-marked side and then relabel if I have to. So you always want to do that so that you know what you're dealing with in your studio. So do we have any questions about metal types? I'm kind of wondering ... So when you're cutting out all of these shapes ... Waste, I'm thinking about waste. Yes, that's a great question. So, you don't want to ever throw away your scrap, because it's actually valuable. So, what I do is, I keep a couple of containers for my scrap in my studio, so silver in particular is the most valuable, right? So, we always want to save our silver scraps. So, any little piece of silver, it gets saved. And eventually what you can do is, you can sent that back to any metal refinery, and they'll either give you more metal, or they'll give you money. Yeah. Okay, cool. So, I also personally keep my brass, bronze, and nu gold, because those can go to a copper refinery. Where I live, it's pretty industrial, so we just keep ... My husband and I just keep buckets, and then every so often, we make a scrap yard run, because he also works on cars, so we have ... We have a lot more scrap than the average person. So, you can keep that as well, but it's really the silver that you want to save for sure.
Class Materials
Free Bonus Material
Bonus Materials with Purchase
Ratings and Reviews
user 1398976626171314
One of the most special things about Megan, is that though she is a creative, she is extremely good at business. Her organized way of thinking and presenting material, and her genuine joy when empowering her students with the tools needed to be successful, is charming and so much fun. Somehow there is such seamlessness and flow to her class structure and explanations, that I can absorb what she says and easily retain it. I really can start a jewelry line just with this class. She is amazing and LOVE her style!!!
user-172aa6
I really enjoyed this class! Megan provides a great foundation for using metal sheets to design/make jewelry and using wire to make unique findings. This was a great class for learning the fundamentals and sparking inspiration for new projects
Vernell Bevelander
I LOVED this class! Megan is such a detailed teacher. She leaves no stone unturned. So much fun! Can't wait for my next class!