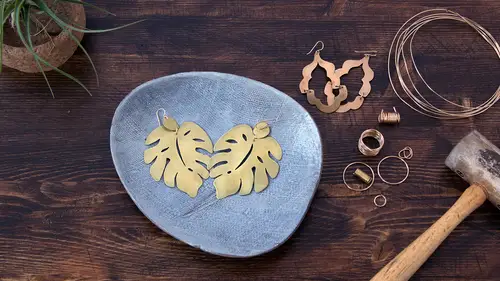
Lessons
Prerequisite #1: Basic Metalsmithing Tools
18:10 2Project Overview: Statement Earrings
07:55 3Designing Your Statement Earrings
24:03 4Choosing the Right Metal for Your Statement Earrings
16:12 5Transferring Your Earring Design to Your Metal
10:39 6Sawing Basics: Putting the Blade in the Saw Frame
10:54 7Sawing Basics: Bench Pin Setup and Hand/Body Position when Sawing
13:04 8Troubleshooting & Student Hot Seat
10:18Drilling Holes and Cutting Interior Shapes
09:11 10Drilling Holes for Jump Rings and Ear Wires
04:22 11Proper Workflow for Cutting Out Your Statement Earrings
30:02 12Finishing Your Metal: Filing the Edges
09:46 13Finishing Your Metal: Sanding the Surface
18:40 14Finishing Your Metal: Choosing a Finish and Polishing
08:23 15Finishing Your Metal: Sealing Brass and Copper to Prevent Tarnish
05:27 16Making Jump Rings to Connect Your Metal
06:31 17Making Ear Wires
09:05 18Assembling and Evaluating Your Statement Earrings
13:34 19Alternative Step: Soldering a Post onto Your Statement Earrings
14:16 20Adjusting your Workflow for Soldering & Hot Seat
08:46 21Taking Your Earring Design to the Next Level
06:13Lesson Info
Making Ear Wires
So then our next step is now we actually have to make our ear wires. And, again, just like with our jump-rings, we can certainly buy commercial ear wires. And I'm not gonna lie to you guys in my production business, I buy commercial ear wires. Because that's a lot of ear wires to make, but I think it's still a useful skill to have, because it let's you experiment with a lot of different shapes. The other thing is that I have found, and this is probably just a pet-peeve, because I've been making jewelry for so long, but it's so easy to spot a commercially made ear wire. Right, there's like those little tell-tale balls, or those wrapping things, and you just... You've just gone through all of this trouble to make a special pair of earrings, why stick a commercially made ear wire on it, that is gonna be like, oh well did she actually make this? Like, that's a junky ear wire that anyone could get. So, that's one reason, but I also just like that you can have all of these options, so you ca...
n see, as I'm putting a couple up here, on our little screen, when you know how to make an ear wire, you have a lot of control over the shape. So you can play with the shape, you can play with balance, you can even create designs, where say it hangs further down from the ear, so being able to make your own ear wires really gives you a lot of options. So if you were doing, say a more geometric design, you might end up deciding you wanna make a more geometric ear wire that goes along with it, instead of something so soft and round. So, we get our jump ring dowrod out of the way. So the first thing you're gonna do when you're making your ear wires is that you're gonna start with wire that's specific for ear wires. And I always recommend, if you can, buying half hard wire for your ear wires, instead of dead soft, so you'll find when you're buying wire, especially when you're buying silver... Oh that's really tangled... When you're buying silver or gold filled, that it comes in dead soft or half hard. For ear wires, start with half hard, because it means they're gonna be sturdier in your ear. So actually a lot of these samples here, I think I made... It's pretty good, I made it out of brass, but it was a little softer, so you can see it's pretty, it's pretty squishy, and so I like half hard. The other thing is, I would recommend using either silver or gold filled for your ear wire wire, because people aren't gonna be allergic to that. Most people don't wanna stick brass or bronze or copper in their ears so I usually either use silver, if I'm working with silver or I use gold filled wire if I'm working with brass and bronze. But if you're just making your ear wires for the first time it's not a bad idea to use a cheaper wire to practice with... Let's find our 20 gauge down here... So I'm just gonna practice with a little 20 gauge brass. And I recommend 20 gauge for ear wires. The general rule of thumb is that you can get away with anywhere between like 19 and 21, but I find that 19 gauge is a little bit thick for most people, they find it uncomfortable, and 21 starts to get a little thin where it actually... Thin is bad too because it can really tug on your ear. Especially if you've got somethin a little heavier, you don't wanna really thin gauge wire that's gonna pull their ear. So 20 gauge seems to kinda be the sweet spot. And then as I mentioned, we wanna use half-hard wire. The other option is if you don't have half-hard wire, after you've made the earrings, you can tumble them to work-harden them. You can also hit em with a hammer a little bit, but I generally find, let's just start with our half-hard wire and it bends a little nicer too, it's a little easier to work with. So then the other decision is thinking about how far do you want the earring to hang from the ear? Do you want it to be a little loop, where it hands really close? Do you want it to be a longer loop, because that's going to determine how long you need to make your ear wire. So, generally, what I recommend, is just kind of starting somewhere, making a sample, seeing how you like it. And then deciding if you like it enough to use it, or if you wanna try something else. And so, because of that, you always wanna start by measuring and making notes about how long your ear wire needs to be to start. I've found that maybe two inches is a good place to start, we'll use that as a kind of a guideline, and then we'll assess our ear wires from there, and see how we like it. So I'm a huge fan of using dress-makers tape measures in my studio because I work with a lot of wire and it's so much easier to measure wire with a flexible tape measure. And I also am a huge fan of using the retractable ones, because they're way less messy on your bench. So I've cut my two inch piece of wire here, and now I'm just gonna go ahead and cut a second one. So for ear wires we need to then go ahead and round our ends so that they're nice going through people's ears. So you actually have three options, in terms of rounding the ends. The first one is literally just to take your flat file, your flat needle file, and just file these guys right at the bench pin. Totally acceptable. The next one is to use something called a cup bur. And they're called a cup bur, I'll put one in our little guy here, I don't know if you can see that but they're called a cup bur because they literally have a little cup at the end of the bur, or at the end of the bit. So they go in the flex shaft and they just round the end of the wire. Now if you don't have a flex shaft, you can also get just these little tiny wire rounding tools. And you can put them in a jig or you can literally just take this here, and I'm just gonna twist this little guy. I think this thing is like, six bucks or something, if you're makin a lot of ear wires, it's a nice investment of your six bucks. I actually find I use this more, that my cup bur because I always have something else in my flex shaft, like I always have a drill-bit, or I always have, usually I have a drill-bit in there, and I never wanna change it, so I'm like oh I'll just grab this little guy. So you can see this is a problem with our, not half-hard wires, I'm kinking it as I'm using it, so half-hard wire stays a little better. So I'm just gonna go ahead and round these ends. And if it seems like it's really funky I might take a file to it but... Basically what we're doing is we're going for something nice and just rounded, that's not gonna stab somebody in the ear when they put it in. And I do both ends, even though only one is going in your ear because it make it look more finished. So now what we'll do... A lot of little jumperings happening here, get these guys out of our way, wow that was all still in my hand. So now what we'll do is you can see any ear wire is gonna have the loop part that's gonna go through it. The loop part, by that I mean the part that goes through your material, then its gonna have a loop that goes through your ear and then it's usually gonna have some kind of little juj at the end to keep it from coming out of yourear. So this is where I am personally a big fan of a nice pair of flat parallel pliers, but really any kind of flat plier will work here. And so I'm gonna start just by going... I usually go about, let's see what we wanna call it, about half an inch down from one end. And I'm just gonna make a bend like an L. So you guys can see our little L, and so this is gonna be the part that's gonna turn into our little loop, make sense? Then we need our big loop that goes through our ear, and I usually just grab a dowel rod for this, but pretty much anything round. And I'm just gonna bend it around. So you can see clearly here we're making tiny little hoops. So I'll bend that around, and then I'll take my flat pliers and I'll bend it up. So now I've got everything but that little loop on the end. And now, you'll notice I did this together, so I bent both of them at the same time, that way they're the same. But then the last step is that I'll take, just a pair of round nose pliers, and now I'll bend up my little hook on the end and I'll do that one at a time. So clearly the proportions of this guy were a little probably not exactly what I was going for. But you get the idea that as you just kinda play around, play with proportions, and get the shape that you want. So if I were doing this again, I would say okay, two inches, clearly a little shorter than I wanted, let's see what happens if I go two and a half or three and go in there. In my own studio, what I do is I actually just have a piece of wire that's pre-cut and it lives on my bench, and it's just that's my earring pattern. And every time I have to make ear wires I cut it out from there. Make sense? It's one of those thing that's like, again, you could buy them but it's kind of fun, simple, and gives it a little more personality.
Class Materials
Free Bonus Material
Bonus Materials with Purchase
Ratings and Reviews
user 1398976626171314
One of the most special things about Megan, is that though she is a creative, she is extremely good at business. Her organized way of thinking and presenting material, and her genuine joy when empowering her students with the tools needed to be successful, is charming and so much fun. Somehow there is such seamlessness and flow to her class structure and explanations, that I can absorb what she says and easily retain it. I really can start a jewelry line just with this class. She is amazing and LOVE her style!!!
user-172aa6
I really enjoyed this class! Megan provides a great foundation for using metal sheets to design/make jewelry and using wire to make unique findings. This was a great class for learning the fundamentals and sparking inspiration for new projects
Vernell Bevelander
I LOVED this class! Megan is such a detailed teacher. She leaves no stone unturned. So much fun! Can't wait for my next class!