Finishing Your Metal: Choosing a Finish and Polishing
Lesson 14 from: Foundations in Metalsmithing: Statement EarringsMegan Auman
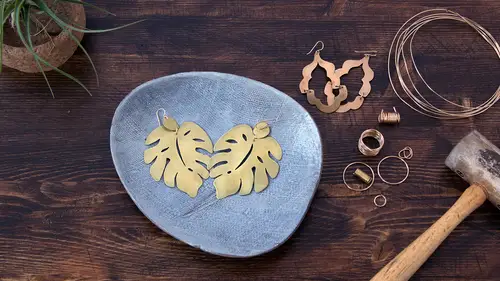
Finishing Your Metal: Choosing a Finish and Polishing
Lesson 14 from: Foundations in Metalsmithing: Statement EarringsMegan Auman
Lesson Info
14. Finishing Your Metal: Choosing a Finish and Polishing
Lessons
Prerequisite #1: Basic Metalsmithing Tools
18:10 2Project Overview: Statement Earrings
07:55 3Designing Your Statement Earrings
24:03 4Choosing the Right Metal for Your Statement Earrings
16:12 5Transferring Your Earring Design to Your Metal
10:39 6Sawing Basics: Putting the Blade in the Saw Frame
10:54 7Sawing Basics: Bench Pin Setup and Hand/Body Position when Sawing
13:04 8Troubleshooting & Student Hot Seat
10:18Drilling Holes and Cutting Interior Shapes
09:11 10Drilling Holes for Jump Rings and Ear Wires
04:22 11Proper Workflow for Cutting Out Your Statement Earrings
30:02 12Finishing Your Metal: Filing the Edges
09:46 13Finishing Your Metal: Sanding the Surface
18:40 14Finishing Your Metal: Choosing a Finish and Polishing
08:23 15Finishing Your Metal: Sealing Brass and Copper to Prevent Tarnish
05:27 16Making Jump Rings to Connect Your Metal
06:31 17Making Ear Wires
09:05 18Assembling and Evaluating Your Statement Earrings
13:34 19Alternative Step: Soldering a Post onto Your Statement Earrings
14:16 20Adjusting your Workflow for Soldering & Hot Seat
08:46 21Taking Your Earring Design to the Next Level
06:13Lesson Info
Finishing Your Metal: Choosing a Finish and Polishing
So, now that we're working through our sanding process that you actually get to make a decision about whether or not you want this matte or shiny, and there are lots of different variations of matte or shiny to work with. There are a lot of ways to achieve a matte finish, so like I said, just going through your sandpaper gets you a nice matte finish, so what I personally do is I work my way up through about 1,500 on my sandpaper and then I usually just hit it with my pink abrasive cloth just to give it a little final juj, if you will. So, that I usually kind of do a little circular... And so I'll just do that and for me, that's what I like. I'm not a high shine girl, I like a nice matte finish. That's a really simple way to do it. Steel wool is another great way to get a matte finish, so you can sand up through probably only really with steel wool if you're going for that nice brushed, steel wool finish. You only might have to sand up to about 800 and then you can just kind of hit it w...
ith your steel wool, give it a little circular rub. That gets you a nice matte finish. The same thing, you can use a Scotch-Brite pad if you literally are thinking of Scotch-Brite that's on a sponge. Yeah, you can just get the Scotch-Brite part. Same thing, you can use that to get a matte finish. Again, your flex shaft attachments, depending on how far you want to go, and if you have a tumbler, which looks like those rock polishing kits that you had as a kid, and we talked about that in that pre-req video. You can also use a tumbler to get a matter finish. I use a plastic media, and so it gives it more of a satiny finish that a metal media with high polish. So those are some options for matte finish. For a shiny finish... So, if you're really looking for a true shine the only way to achieve that, or the best way to achieve that, are with buffing wheels and polishing compound, and I'm not gonna get into that here just because it's super messy, but that's something that you can do either on a big buffing wheel or on your flex shaft. So if you're interested in... You're like, "Megan, I want it to be "like high, shiny, fancy," get your sandpaper, sand all the way through, get all those scratches out and then hit it with a little muslin buffing wheel with a little bit of rouge on it and that's gonna really get the shine. I don't have the patience for that, which is why we're not doing it here. But as you guys saw, you can start to get a nice shine with some of these flex shaft attachments as well. So, basically what you want to do is go to your jewelry supplier, look for finishing and just look for things that put on polish that you can use in a flex shaft. And again, your tumbler is an option as well. So if you use metal media in your tumbler, if you have steel shot and you throw your piece in the tumbler for a while, and by a while I mean four, six, eight hours, so a while is really a while, with your steel shot that'll give you a shiny surface. It's not gonna be a perfect high polish like you would get with the rouge and the buffing wheel, but it'll still give you a nice shine and the bonus of the tumbler is that it'll work hard on your piece. So if you're using a softer metal like copper or silver a few hours in the tumbler is gonna make it a little bit stiffer. So, another question that I know people might have is about liver of sulfur or surface oxidation. So, that is a long topic that we're not gonna get into in this class. In fact, there are whole entire classes that people teach on color on metal, so there's a lot of different options there. So, the easiest one is something called liver of sulfur, and liver of sulfur is... It is sulfur, so it literally smells like rotten eggs, and you can get it in either chunk form, and I was gonna bring mine and realized I didn't. So, you can get it in chunk form or you can get it premixed in liquid. It's better to buy it in chunk form because it lasts longer, and then what you'll do is you'll just take a couple of chunks, you'll dissolve it in water, and then liver of sulfur basically takes either your silver or your copper and turns it that really dark, almost black. So, copper tends to be a little bit more browny, silver pretty much gets back. So if you wanted that nice, dark metal effect you can do that with liver of sulfur. That is not a permanent coating, so if you put that on something and someone is touching it or rubbing it, eventually that will rub off. So that's something to keep in mind. It's not such a big deal for earrings, though I do know people who play with their earrings a lot and rub their finish off, but it's definitely a consideration if you're making necklaces or rings or bracelets because it's not a permanent solution. There are also lots of other ways to oxidize or patina your metal, and basically what I would do is if you're like, "Megan, I don't "love the color of this brass." If you don't love the color of the brass I wouldn't work with the brass to begin with, but if for some reason you want something else I would just search for your metal plus the word "patina" and you'll find lots of other options. Most commercial jewelry suppliers sell different things. So for instance, liver of sulfur doesn't work on brass, but there's other oxidizers for brass that do the same job. So, really that's... We're not gonna cover that because that could be a whole other class, maybe we'll do that in the future, but there's a lot of different options that you can do in terms of adding color. But I always recommend starting with metal colors that you love to begin with. So, you guys have any questions about finishing in that regard? I do. Yes. So, the tumbler, would that be after you've done all the sanding or is that instead of some of the sanding? That's a good question, so after the majority of the sanding, because the tumbler is not gonna take out those deep scratches, so you want to still get it to a point where you've got out any of those deep scratches, kind of more of a matte finish, and then throw it in there, yeah. So, you'd take it... So you'd go through like, 400, with the sandpaper and then... I would probably... So, I would do a few experiments to see what you like and what the result is, but I would- Sure. If you can get away with it, I would go 400, make sure all the scratches are out, throw it in the tumbler, see if you like that result and because the point of the tumbler is to avoid as much sanding as possible, but we have to get those deep scratches out, so I would say go to your 400, do a couple tests, see what you like. Yeah, and the tumbler is never as ideal... Tumbler is much nicer for things made out of wire, like chain... Tumble all day, it's beautiful. If you have really big surface area it's never gonna look great, so I would also do a test piece before I would do your finished project, because some... You might not like the consistency of it on a big piece of flat metal, so I would do some tests first. So that's why I personally... I love my tumbler for chain and wire. I don't necessarily love it for sheet, but it's an option. Did you... I forget, at the very start you had that horizontal scratch. Yeah. Did you scratch with that with the... Yes, my first grit I scratched with that. What if you have different direction scratches happening? You may just need to go a couple different directions with your 150 grit until you get it all out, yeah. So that your 150... You may end up going two or three directions if you find you've got really deep scratches. Okay. Yeah, yeah, you want to try to avoid putting deep scratches in your metal if you can. That was why, you know, someone had asked about like, "Can you use metal shears?" Metal shears always leave awful scratches on your metal, so that's why I like to avoid them, but sometimes they're just inevitable. Or sometimes, depending on where you're buying your metal from, you get metal that just has scratches in it. A couple of things to keep in mind when you're storing your metal, like if you buy a lot of sheets of metal, put pieces of paper in between them. Do things that keep them from scratching against each other because then it's gonna save you a lot of time. I'm always so bad and then I pick my metal up and I'm like, "I shouldn't have just thrown that "in the box when I was done with it," right? So, take a little bit of care in storing your metal so that you end up with less of those deep scratches if you can. Okay. And that's another one, too, when you always center punch when you drill because if you don't center punch when you drill that's when it skates across the metal and that's a horrible scratch to have to take out.
Class Materials
Free Bonus Material
Bonus Materials with Purchase
Ratings and Reviews
user 1398976626171314
One of the most special things about Megan, is that though she is a creative, she is extremely good at business. Her organized way of thinking and presenting material, and her genuine joy when empowering her students with the tools needed to be successful, is charming and so much fun. Somehow there is such seamlessness and flow to her class structure and explanations, that I can absorb what she says and easily retain it. I really can start a jewelry line just with this class. She is amazing and LOVE her style!!!
user-172aa6
I really enjoyed this class! Megan provides a great foundation for using metal sheets to design/make jewelry and using wire to make unique findings. This was a great class for learning the fundamentals and sparking inspiration for new projects
Vernell Bevelander
I LOVED this class! Megan is such a detailed teacher. She leaves no stone unturned. So much fun! Can't wait for my next class!