Proper Workflow for Cutting Out Your Statement Earrings
Lesson 11 from: Foundations in Metalsmithing: Statement EarringsMegan Auman
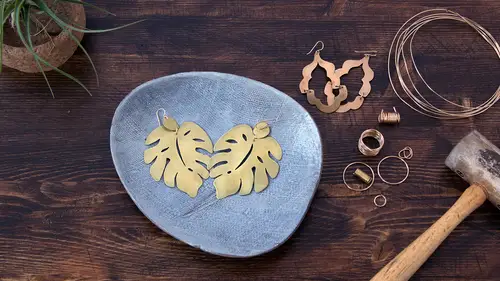
Proper Workflow for Cutting Out Your Statement Earrings
Lesson 11 from: Foundations in Metalsmithing: Statement EarringsMegan Auman
Lesson Info
11. Proper Workflow for Cutting Out Your Statement Earrings
Lessons
Prerequisite #1: Basic Metalsmithing Tools
18:10 2Project Overview: Statement Earrings
07:55 3Designing Your Statement Earrings
24:03 4Choosing the Right Metal for Your Statement Earrings
16:12 5Transferring Your Earring Design to Your Metal
10:39 6Sawing Basics: Putting the Blade in the Saw Frame
10:54 7Sawing Basics: Bench Pin Setup and Hand/Body Position when Sawing
13:04 8Troubleshooting & Student Hot Seat
10:18Drilling Holes and Cutting Interior Shapes
09:11 10Drilling Holes for Jump Rings and Ear Wires
04:22 11Proper Workflow for Cutting Out Your Statement Earrings
30:02 12Finishing Your Metal: Filing the Edges
09:46 13Finishing Your Metal: Sanding the Surface
18:40 14Finishing Your Metal: Choosing a Finish and Polishing
08:23 15Finishing Your Metal: Sealing Brass and Copper to Prevent Tarnish
05:27 16Making Jump Rings to Connect Your Metal
06:31 17Making Ear Wires
09:05 18Assembling and Evaluating Your Statement Earrings
13:34 19Alternative Step: Soldering a Post onto Your Statement Earrings
14:16 20Adjusting your Workflow for Soldering & Hot Seat
08:46 21Taking Your Earring Design to the Next Level
06:13Lesson Info
Proper Workflow for Cutting Out Your Statement Earrings
So what I actually want to talk about now is workflow and how we handle the fact that we have this giant chunk of metal and a design that's not so giant. So first off, let's talk about the order of things. Now we're actually really ready to work on your project. So first thing that we did is we went ahead and put our design on our metal. Now if you're using a large sheet which most of you probably are to begin with. I recommend cutting out some general outlines. I'm gonna demo that in just a second. So we're gonna do big chunks first. Then we might separate those into slightly smaller chunks. Then I recommend center punching and drilling holes for all your jump rings. Any center pieces you might want to cut out. We actually are gonna do that before we do all of our final cutting. And the reason is it's easier to hold on to a big piece of metal to do that. Then a small piece of metal. But again, there is sort of a balance between that so I'm gonna cut this chunk out first. Then drill my...
holes, then cut out my details. So from there we'll actually but out our interior shapes. So general rule of thumb is that you want to cut out interior shapes before you cut out exterior shapes. Because again you have more metal to hold on to but obviously in this state I can't but out this interior shape right now. Because I'd run into the back side of this. So we're gonna cut the chunk out then cut out our interior shapes. Then finish cutting out our exterior shapes then we're gonna take our paper off. Because remember we don't want to leave this on here any longer than we have to. So I want to show you guys kind of how I do this process of cutting out. Just so you can see sort of how I make decisions. Because even though we want to practice sawing really we don't want to cut anymore than we have to. We want to avoid making lots and lots of giant cuts through our metal. So in this case and this is what I'll often do in my studio as well. I'll sometimes prep multiple things on one sheet so that I can really get my layout. Maximize my material and then go in and work from there. But now what I'll do is I want to kind of figure out what the smartest way is to sort of chunk this out of here without dealing with this running into the backside problem. So, in this case I think I can get kind of this way a decent amount. And I can go this way. So I'm gonna start by sort of freeing these two pieces. So I'm just gonna come in here. (sawing) And if your paper is starting to peel up a little you can just throw a little more glue in. We're just kind of pressing down. So I'm gonna cut into my edge and now I'm cutting this out of my metal but I'm not gonna cut away from it. Right, I'm actually gonna cut on my design as much as I possibly can. (sawing) But now when I get to this high point here. Clearly I've got a decision to make. Cause if I start to come back in here at some point the back of my saw is probably gonna hit this. So what I'll do is sort of split the difference. I'm gonna follow this down but at some point I'm gonna kind of shoot over this way. (sawing) And then I'll just rejoin my line. Some times I'll do a little peak just to make sure we're not running into the actual. You know, this is the problem when you can't see your bench pin cause you got this big sheet. So I'll just kind of check to make sure I've got my barrings. (sawing) And now at this point I'm basically gonna cut this until I can't cut it any further. Until my soft ring says nope, can't do it. So, I'm gonna turn this. (sawing) And you can see what's happening there. Running into that and now I'm just gonna back this up and you can see I can actually. I just gave this metal a little flex here and made it easier to pull my soft ring out. And then I'm gonna come over here and I'm gonna cut. And in this case what I'll probably do is. This is a lot of sideways cutting and since I have to cut this anyway. I'll come straight in here. Maybe. (sawing) So I'll go ahead and start cutting out this shape just because it's the smartest line. (sawing) And then I'll just cut across to this guy. (sawing) And I think we may run into trouble here. I don't think I'm gonna make this turn. So we'll find out. (sawing) Let's see. (sawing) Yeah, see so. My lines didn't quite meet. So we're just gonna shoot out here for a little bit. That should be good. And then we'll just come back in here. So you'll find things like this happen. It's not a big deal. Just kind of cut it out. See if I can get that in there. So now I've got this chunk free. And then we're gonna do the same thing to get this guy free. I'll just kind of follow this line, up around. Cut into this this way and get this free. So I wouldn't actually cut this here. I would not cut from here to there. I would actually cut all the way up to that line. So once we've got. We have a question or are we good? We're good right now. Alright, so once I've got this piece free. Now I can go ahead and center punch for my center cut outs and do my jump ring holes. And I'm just gonna do this all in one. In one step. So we'll go ahead and again I'm gonna pick a spot in the center. Center punch. So because I'm confident in my ability to turn these tight corners. I'm just gonna put one hole in here. If you were cutting this shape out and it made you nervous. You could actually put like say a pilot hole on each side. That way if your saw broke halfway through you wouldn't have to start all the way back from the beginning. So I'll go ahead and center punch my pilot holes. Center punch. Jump rings. And of course you guys can see how in our design example where this was two separate pieces. We would just connect by jump rings. We would stack those like this and it would actually be even be faster to cut out. But I wanted to show you guys how to cut some things out of the middle. So I've got these center punch. I'm gonna come back here. It's my flex shaft. Let's put this on the wood and not on the metal. (drilling) Drill my holes. (drilling) It's really crooked in there. (drilling) Oh, that's interesting. That is not something that I have ever had happen before. So just like drill bits or soft blades. A drill bit can break. This one is now broken and in the end of my bench pin. That's why we wear safety glasses. And so now in this case you can make a decision. Obviously it was easier to drill these pilot holes when I have this big piece. But I think in this case I would probably cut this out. Like cut one of my sides out before I cut the center out. Just because again. You can't always do this. This little test, right. Am I gonna make the corner. Am I gonna be able to turn and so I would cut that out. So we'll do that. Do you guys have more questions about this while we're cutting a few things? When we're talking about the paper and how long you can leave it on there. Like is there. You're good up until. I can see myself tracing out all this stuff and realizing uh oh. I have too much to saw. And then when am I gonna get back in here to do this? So like you said at the start that one of your shapes had been. Like it's been a month and now it's too dry. So is there an optimum time to leave the reversement on there? I would say no more than a couple of days. A couple of days. Yeah, so I would try to kind of keep it so that you know. Okay, in a couple of days I'm gonna either get this cut out. So don't get too excited and glue all the things and then it's a month later and you're like oh. I never cut those out. So yeah if you kind of think about it as either I'm gonna do it in the weekend or I'm not gonna glue it is a good rule of thumb. A question we had from earlier is how long did you leave, this is from earlier, the patterns and the glue? Usually I would say it takes like five to ten. So in my own studio I'll go let it sit. I walk away five to ten. Sometimes the other thing that I'll do is like I'll prep different pieces of metal at the same time. So I'll do my tracing, prep it. Put the rubber cement to dry. Let is set aside and then I'll work on the next one for the next piece of metal. So I'll work that way as well. So yeah and you kind of visually see. It's shiny when it's wet. It'll look more matte when it's dry. So that's the best way to tell. Cool and while you're working on that. Another question from Laurie Jacobson would like to know. Do you wait for your saw blade to break or will you change it after a certain number of cuts to make sure your always using a sharp blade? That's a great question. So what I find it that most beginners. Their saw blade will break long before it gets dull. But there is a point of diminishing return. So you will eventually get dull. So if it seems like it's not cutting really well. Or it's like really dragging or the noise just doesn't sound right. It may literally just be that it's dull and you can check that by running your fingernail on it. It starts to feel smooth then you've actually worn down your saw blade and you should go ahead and change it. The other thing that I will occasionally find with a saw blade is that they're manufactured and they're not perfect. So actually sometimes the teeth are not totally straight and so if you start to saw and the sound. It just feels wrong and the sound is like rghh, rghh. It's probably a little bit funky and sometimes I just take that out and pitch it and get a new one. Cause they're not perfect. Cool and ready for some more? Yeah. Okay great. Ms. Wimms would like to know could you use a pair of wire cutters or flash cutters to cut out the large shapes first around the metal areas? So you're not gonna use wire cutters. Now there are metal sheers that you can use. The problem with metal sheers is that they actually deform the metal and they can evenly scrape. So I have some metal that I was trying to cut out some circles to make some holes for raising. And I was like I'm just gonna use these metal sheers real quick. And it was like these zig zaggy scratches on my metal that then you have to actually file out. So one of the things that you'll find over time is that you'll get faster at sawing but there are certain things. Like sanding out scratches that it's impossible to get faster at. And so while it's really easy to want to look for the shortcuts in the sawing process. I totally get it. This is actually the thing that you want to get good at. Just be able to do it cause it's actually gonna save you a lot of finishing steps later on. Which we'll talk about. Great and then. Well actually, let me add one thing to that. I will say that if you are cutting up a lot of things in a perfect world there are desktop. What are called bench sheers. A lot of them are guillotine so they actually have a handle that swings down and chops your metal into pieces. If you are really into using a lot of sheet metal. They're a couple hundred dollars. They're kind of heavy but they can be a good investment because they'll cut cleanly. That's how actually the order of your metal is cut. Oh now, guillotine sheers. So that is a piece of equipment. It's not a beginner tool but something maybe to dream of in the future. Great and is there any noticeable additional resistance when cutting with the paper and the rubber cement? The metal versus just cutting the metal. Having marked with a Sharpie. So there's a tiny little bit of resistance but not enough that it's really gonna bother you. Where you might see it is actually if you didn't glue it down properly. So like I know I was trying to experiment with gluing some paper on the back just to keep the back side from scratching. But there were some gaps in my glue and I think I didn't wait for it to dry. So the paper kept coming loose and that's when you'll actually get that kind of resistance. That's why I like tracing paper. It's so thin. I think if you were using the sticky adhesive printing paper. It might hae a little bit more resistance again but it's hardly noticeable. Great and Ahratti from London would like to know. Can we use spray mount or something similar to stick the paper to the metal? I have not used spray mount I believe would probably work pretty similar. And do you think it could clean off as? Yeah, I would probably use the same rule of thumb. Like the sooner you can get it off of there the better it's gonna be. Just cause of the way that stuff tends to dry but yeah. There's no reason that that couldn't work as well. Cool. Awesome. Alright, so let's do a little bit more cutting here while you guys can think about if you have other questions. But again I'm just gonna kind of follow this around here. (sawing) So the other thing that you'll notice is that I actually left what's probably a two millimeter gap between this. As you're cutting skills get better you can nest things closer and closer together. So that they're literally the width of a saw blade apart. So there's no reason really for this gap other than that I was drawing quickly. Especially if you're using silver and you've got more material. So I think in this case. If I tried to go this way I'm gonna bump into this back edge here. So I'll actually just. I'll take this line. I might bump into it this way too. (sawing ) But we'll find out. (sawing) Just in case. So as you can see the more you do this the easier and more natural it gets. So I'm gonna go ahead. I'm gonna cut this out but I just realized we have this tiny little point here from when I couldn't quite get my saw blade to reach. So I'm gonna go ahead and actually take that off now. And you can see when I'm trying to cut an edge like this if I let this hang out here. It wants to really flex so again I'll slide it back in my bench pin as far as possible. And just cut that off. (sawing) So when we get to the next segment. We're gonna talk about cleaning up little burs or things like that that you have from filing. But ultimately your goal is to become the best sawer if that's how what we can call it. The best sawer possible so that you actually have to do as little filing cleanup as possible. So we want to get really good at cutting out our lines. So I'm gonna go ahead and cut out my interior here. And you can see how as you get comfortable with a saw this project really should not take you. I feel like my saw, ah ha. I see what's happening here. So, I was feeling like this is really hitting the bottom and what you can see here ideally is that this has actually slid really far out of this clip. And so that will happen sometimes. So I'm actually just gonna put it back where it belongs. The other thing I have found is that depending on who you buy your saw frame from. What you'll see with a lot of tools is that they come with a lot of oil on them. They do that to keep it from rusting when it's in storage and whatever warehouse it's sitting in. But depending on how much oil. I've seen students get soft rings where it's like. There was so much oil that it's actually slick in between these two little plates. So you can go in if you're feeling like your saw blade is really slipping out. You can go in and just get a little paper towel. You can clean that out. Or even if you're really desperate. You can take a little bit of sand paper in between these two little plates and actually rough them up. So if it feels like your saw blade. Or your saw blade is not staying in your soft frame. Just check to make sure that it's nice and oil free I there. Nice and clean and maybe even get a little bit of a tooth. But yeah, so you just want to kind of be mindful of things like that. Like oh, I thought that there was more gap in my soft frame than this. Oh, let me check to make sure my blade is where it needs to be. So I'm gonna go ahead. I'm gonna ignore the one I dropped on the ground. And use the other half. Cut out my center. Do we have anymore questions coming in? Taking a peak now. That's my whole table nose. I'll answer the question where are the cute wooden trays from? They're from Amazon.com. (laughing) And let's see. Just a lot of kudos here. (sawing) I think we're good for right now. Perfect. So I just want to go ahead and cut out this center shape. (sawing) And again this is a case where I think a lot of people would want to cut into these corners. But I like to just make these turns. (sawing) And I'm gonna give our studio audience full warning now. I think that we have time to hot seat somebody else. I want somebody else to try it and I want to have someone do an interior cut. So I'm gonna let the remaining four of you mentally think about who wants to be brave while I cut this one out. (sawing) So it's really in those corners. It's just all about keeping your saw blade moving. Keeping it nice and easy. (sawing) But you also don't want to feel like you're rushing. Cause that is another time where you will break blades. (sawing) And I just cut my shape out. So you guys can see once you get good at this it doesn't take that long. It's not such a big deal. I mean if you're doing a ton of piercing obviously the more intricate, the more detailed. The longer it's gonna take. But you guys can really knock these earrings out really quickly. Alright, who wants to be brave and try an interior cut? Tonya already tried so someone else needs to go. You should just. You should do it. And I'm gonna find the one that fell on the floor while you're coming up here. So you get the magic safety glasses. Oh I have glasses. I have readers. If you're more comfortable wearing those then grab those. Well that way if I mess up you will be safe too. My eyes are also protected. Here we go. Okay. So you're gonna cut this guy. We're gonna cut the middle piece. So it's already loose there. I won't make you put the top piece in but I'll just let you thread that on. Okay, okay. Just like before. I'm gonna come to the front of the table so I can lean in against this while you're. Wait. (laughing) First things first. We want to make sure our design goes up, yep. So this is where I. This is where you kind of lean against the table, yep. And really get that nice and tight. And Megan can you remind us what blade number we're using? We are using a one ot which is written like 1/0. Thank you. And is this action. Is it actually pushing that together so that when you? Yeah, so you're actually pushing so you wouldn't actually push. Like compress the soft ring a little. These together. Yeah. Okay. So yeah. And if you have a hard time with this slipping you could also do this in the V of your bench pin. I can see that it's not. How's that sound with your little fingernail? That definitely sounds loose even with that on there. So let's go ahead and try that again. So go ahead and just unloosen that. I'll pull back on the table while you do that. So yes, you actually want to give that a little bit of a press so that you can actually see this sort of bending. So this should slide down a little bit when you do that. Yeah I didn't see it really do that. This looks. Give it a little muscle. This is a lot harder than it looks. It also doesn't help. Hey Tony, can come push on the back side of this table really quick. Doesn't help that our table has got a little bit of a roll to it. That looks better. How's that sound? It's hard to tell with this on here. But that's better for sure. Alright. Let's give it a go. Put a little bit of lubricant on there. Okay. And okay. Did I mention that I was a total beginner. That's what we want to see. I want people to see what it's gonna look like for them. So just start up and down, nice and easy. So one of the things that's easier to do. So what happens is so you're kind of cutting straight and so when you get to your line you're gonna have to make a 90 degree turn. And you don't want to do that. So cut it in an angle and sort of ease your way into that. It'll make your life easier. (sawing) So we're gonna go just a little bit more vertical on you so stay nice and straight and just kind of a little bit easier. Don't try to force it forward so much. I want to though. (laughing) I want to just go. You want to let the saw blade do the work. Okay. (sawing) How were you so good at this? Wasn't she? (laughing) I feel like Tawny has a leg up in that even though she hasn't sawed before she doesn't work with a lot of tools all the time. (sawing) So the other thing that you can do is see right now how you're making these really tiny little strokes. Yeah. Use your whole arm. That what actually Tawny was doing really well. That was making it look easier. But don't force forward. So just nice and up and down. Okay. (sawing) (laughing) (sawing) So you really want me to do this whole thing? Yeah, I want you to turn the corner is what I want you to do. Okay. Yes. Any best practices for clean up? How you handle clean up. Yeah, I just keep a dust pan and brush handy and then all the little sawing, filing. Not filing, sawing bits called the dust. I just sweep it up and throw it away. I usually just do exactly what I was doing here and then I kind of make little piles of my scrap and I just stick them in a little bucket. So the scrap I keep separate and then everything else I just sweep up. You'll also notice that I always wear an apron because otherwise you end up with a lot of little glittery dust all over you. Alright, let's turn this corner. Turning the corner. I got stuck. You did get stuck so what we're gonna do is twist it back to where it was. Now we're to stuck anymore. So now, go ahead and grab that again. So back to your corner so up and down. Just keep moving up and down. Nice long strokes and while you're moving up and down. Yep, spin around like that. Look that was easy. So if you get stuck it's always easy to try to back it out a little. But always try to keep your saw blade moving. That's the most important thing. See you're getting the hang of it. I feel like this is. By side four I'd be. You'd be good, alright. I won't make you cut all four but thank you. Thank you. Alright. See it's helpful to see I think other beginners do it just so you know it doesn't always look so smooth but the more you practice it the easier it gets. And it's also kind of one of those. It's just like riding a bike. You know, I hadn't actually done a lot of sawing until I was prepping for this class and then I was like. This is so fun. I'm just gonna saw the things now. Alright, so any other questions about sawing the metal? Clearly it's very simple. It's really just a practice makes perfect kind of process. Any other questions from our online audience? You knew you were gonna get this question. I keep breaking saw blades as I try to pivot in the metal. Any suggestions? So just like we just did there. It's really about just keeping it moving. The other thing that I found is it's really easy where you want to like. Because you're trying to keep everything moving. You kind of forget to put a little bit of downward pressure on the metal. And when the metal moves. If the metal jumps up from the bench pin that's gonna snap a saw blade. So making sure that you're keeping nice long movements. Nice and spinning and just kind of spin, turn. It's a little bit of patting your head and rubbing your stomach at the same time. Cause you're trying to do these two different things. Right, spin the metal. Spin the metal and move that. So part of it is just practice but make sure I would try to notice. Because I'm guessing your saw blade is breaking because your metal is popping up. So keep a little bit of downward pressure and just keep spinning it. I really just keep practicing. But yeah, really that nice long movement and zero forward pressure on the saw blade. When you're trying to make that pivot. No forward pressure. Just vertical and spin your metal. Let's say someone was to go out and this is just sort of ballpark. Give us a number. If I'm gonna sell one pair of earrings. I'm new, I'm going to the Craft Fair. What's a good starting price for a pair or two of earrings? (laughing) You knew you couldn't have a Megan Allman class without talking about pricing. It's my favorite subject. So I'm gonna answer that question. Not with a specific number but I'm gonna give you guys a little bit of homework if you're thinking about selling. Which is if you're thinking about selling you want to track your time. Because here's the thing. We can say oh well a big earring should be $ or $100 or how ever. But this is a pretty simple design to cut out. Where as those monstera leaf earrings have a lot more intricate piercing. So what I want you to do if you're thinking about selling is track your time. Figure out how long it takes you to cut out your pair of earrings. And then you're gonna take your time and your gonna multiply that time in hourly rate. So let's say you want to get paid $30 an hour. If you guys have taken any of my business classes you know I think about numbers a little low but we'll start there. So let's say it takes you. You know, you want to pay yourself $30 an hour. It takes you half an hour to cut out your two pieces. We're looking at $15 for your time. It might be another $10 in materials. So we're gonna add out materials on there. So we've got time plus materials so we're at $25. Then I like to add a little bit extra for out overhead and out profit. So let's add in another $10 there. So I'm at $35 and that's our wholesale price in case we want to sell to a store. So we're gonna double that and that puts us what? Up there at $70 so just like that. We got to $70 so there's no magic number but I would say it's probably pretty safe that unless you're cutting out something very small and simple. You're not gonna be under $50 for sure. But the best thing is if you know you want to sell track that time and make sure that you are getting paid for what you're doing.
Class Materials
Free Bonus Material
Bonus Materials with Purchase
Ratings and Reviews
user 1398976626171314
One of the most special things about Megan, is that though she is a creative, she is extremely good at business. Her organized way of thinking and presenting material, and her genuine joy when empowering her students with the tools needed to be successful, is charming and so much fun. Somehow there is such seamlessness and flow to her class structure and explanations, that I can absorb what she says and easily retain it. I really can start a jewelry line just with this class. She is amazing and LOVE her style!!!
user-172aa6
I really enjoyed this class! Megan provides a great foundation for using metal sheets to design/make jewelry and using wire to make unique findings. This was a great class for learning the fundamentals and sparking inspiration for new projects
Vernell Bevelander
I LOVED this class! Megan is such a detailed teacher. She leaves no stone unturned. So much fun! Can't wait for my next class!