Finishing Your Metal: Sealing Brass and Copper to Prevent Tarnish
Lesson 15 from: Foundations in Metalsmithing: Statement EarringsMegan Auman
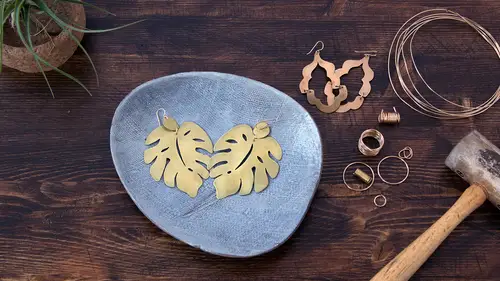
Finishing Your Metal: Sealing Brass and Copper to Prevent Tarnish
Lesson 15 from: Foundations in Metalsmithing: Statement EarringsMegan Auman
Lesson Info
15. Finishing Your Metal: Sealing Brass and Copper to Prevent Tarnish
Lessons
Prerequisite #1: Basic Metalsmithing Tools
18:10 2Project Overview: Statement Earrings
07:55 3Designing Your Statement Earrings
24:03 4Choosing the Right Metal for Your Statement Earrings
16:12 5Transferring Your Earring Design to Your Metal
10:39 6Sawing Basics: Putting the Blade in the Saw Frame
10:54 7Sawing Basics: Bench Pin Setup and Hand/Body Position when Sawing
13:04 8Troubleshooting & Student Hot Seat
10:18Drilling Holes and Cutting Interior Shapes
09:11 10Drilling Holes for Jump Rings and Ear Wires
04:22 11Proper Workflow for Cutting Out Your Statement Earrings
30:02 12Finishing Your Metal: Filing the Edges
09:46 13Finishing Your Metal: Sanding the Surface
18:40 14Finishing Your Metal: Choosing a Finish and Polishing
08:23 15Finishing Your Metal: Sealing Brass and Copper to Prevent Tarnish
05:27 16Making Jump Rings to Connect Your Metal
06:31 17Making Ear Wires
09:05 18Assembling and Evaluating Your Statement Earrings
13:34 19Alternative Step: Soldering a Post onto Your Statement Earrings
14:16 20Adjusting your Workflow for Soldering & Hot Seat
08:46 21Taking Your Earring Design to the Next Level
06:13Lesson Info
Finishing Your Metal: Sealing Brass and Copper to Prevent Tarnish
One last thing in terms of finishing is if you're working with brass, copper, or bronze, you might want to think about sealing it to prevent tarnish. So, oxidation is just a fancy word for tarnish that happens when your metal is exposed to oxygen, which means all the time in the air. And so, any metal that contains copper is going to oxidize or tarnish over time, and there are two solutions to that. One is just to say that's what happens and it gets a nice agey patina, or you can clean it off later, or you can seal it. So, I am a fan of two different solutions when it comes to sealing your metal. One is something called Renaissance wax, and Renaissance wax is literally just a clear wax. Clear, white, that kind of thing. And I always keep just a little rag in here. So you want something kind of soft. And then, the way that this wax is really designed is kind of like, let me move that out of the way, kind of like, wax on, wax off, which none of my students ever laughed at that joke. Whic...
h makes me really sad. So, you're going to put a little bit on, and then you're going to take a cleaner side of your rag and actually buff it off. What's nice about Renaissance wax is that it's not actually a permanent coating, so if for some reason you do have any oxidation on your metal, it's really easy to clean the Ren wax back off, and reapply it latter, so if for some reason you need to get in there. The downside of Renaissance wax is that it doesn't always protect perfectly and because you are buffing something on, if you've got any kind of patina or surface oxidation, it doesn't preserve it perfectly, you may end up rubbing some of that out. So let's say you did a really fancy patina, and you loved it, and then you put the Ren wax on, and you're like, "Well I just took half of it off accidentally." So that's the kind of downside of the Ren wax. Which is why another option that I really like is what I always refer to, because that's what someone else referred to as the bulldog spray, because there is a picture of a bulldog on there, which is actually just a sculpture, it's from a company called Sculpt Nouveau, and it's called Clear Guard. It comes in two finishes. It comes in matte and satin. The matte is pretty matte. The satin has got a little sheen to it. It will not magically make your piece shiny, so you still need to polish. What I like about it is that there's a low VOC version. So, it's like a dollar more, but it's totally worth it. So this is something if you've got a lot of stuff and you want to coat it, it's a nice kind of clear coat that you can just spray on and seal. So I generally recommend if you're going to work with brass, bronze, or copper, when get the finish the way you like it, hit it with one of these things to preserve it. And I would recommend doing that before you add your wires or jump rings, because it's going to be hard to buff this on if we've got our jump ring connection here. Trying to get that on is a little bit tricky. It's a little bit easier to hit with the spray guard, but it still, I would probably spray it once, assemble it, and then spray it again. Any questions about sealing the metal? And again, it's not required, but it's a nice little step. For best practices to your purchasers, how do you recommend they care for their... Yeah, so I always, first of all if you're selling things, I like to make a whole little care card for your customer. The biggest mistake people make with their jewelry, and I always like to tell my customers this is do not store your jewelry in the bathroom, because the humidity in your bathroom is horrible for every piece of jewelry. When people show me their jewelry, and they're like, "Why's it all tarnished?" and I'm like, "Do you keep it in your bathroom?" "Well yeah." "Don't do that." So I generally always tell my customers, don't keep it in your bathroom, so what I would recommend for people is telling them just to keep their pieces in something where they're not going to get scratched or things. So the biggest issue with designs like this is it's a big surface area that wants to rub against things and get scratched, so if you've sealed it properly, they shouldn't have to worry too much about oxidation. So what I would say is recommend to your customers that they actually store their earrings each one in its own little baggie. So instead of putting two together, in one baggie, where they scratch each other, I recommend telling them to store them separately, or store them hanging if they're not traveling with them, tell them to store them hanging. 'Cause that's going to be your biggest issue is things actually things scratching against each other probably more so than surface oxidation. And along with this past content, The Landlocked Sailor would like to know, do pieces get bent up in the tumbler at all? So, if you have something that's really fine, it could, But for the most part, I tumbled these guys that have the little ears on them, and nothing got bent in there, so unless you have something that's really, really tiny, it should be OK there, but if you think about it, you can throw in chain and that's not gonna get it, so they tend to not get bent, the mostly get work hardened.
Class Materials
Free Bonus Material
Bonus Materials with Purchase
Ratings and Reviews
user 1398976626171314
One of the most special things about Megan, is that though she is a creative, she is extremely good at business. Her organized way of thinking and presenting material, and her genuine joy when empowering her students with the tools needed to be successful, is charming and so much fun. Somehow there is such seamlessness and flow to her class structure and explanations, that I can absorb what she says and easily retain it. I really can start a jewelry line just with this class. She is amazing and LOVE her style!!!
user-172aa6
I really enjoyed this class! Megan provides a great foundation for using metal sheets to design/make jewelry and using wire to make unique findings. This was a great class for learning the fundamentals and sparking inspiration for new projects
Vernell Bevelander
I LOVED this class! Megan is such a detailed teacher. She leaves no stone unturned. So much fun! Can't wait for my next class!