Introduction to Platinum / Palladium Printing
Lesson 35 from: Introduction to Alternative Processing in PhotographyDaniel Gregory
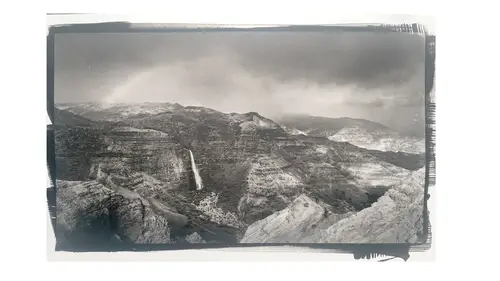
Introduction to Platinum / Palladium Printing
Lesson 35 from: Introduction to Alternative Processing in PhotographyDaniel Gregory
Lesson Info
35. Introduction to Platinum / Palladium Printing
Lessons
Class Introduction
03:03 2Overview of the Alternative Process
03:31 3Overview of the Digital Negative Process
10:21 4Working with Black and White Digital: What You Need
09:17 5Working With Black and White Digital Images: Color Settings
08:33 6Working with Black and White Digital Images Lightroom
07:01 7Working With Black and White Digital Images Photoshop
11:57 8Working With Black and White Digital Images 3rd Party Plug-ins
07:29Avoiding Key Artifacts
20:26 10Creating the Step Wedge for Curve Corrections
39:00 11Organizing Your Adobe® Photoshop® Files and Curves
11:20 12Setting Up the Printer
20:24 13Lab Safety and Workspace Set-Up
03:49 14Setting the Maximum Black Time
12:06 15Getting the Initial Curve Test Numbers
20:04 16Correcting the Curve
20:37 17Printing the Curve
06:08 18Sharing Curves
08:50 19Caring for the Digital Negative
12:29 20Intro to Cyanotypes and Safety
07:46 21Paper and Brush Types
05:08 22Coating Process and Cyanotype Chemistry
12:17 23Making the Cyanotype Print
06:41 24Washing the Cyanotype Print
12:29 25Creating Cyanotypes Photograms
14:59 26Toning Cyanotypes and Cleaning Up the Darkroom
18:43 27Introduction to Van Dyke Printing
04:36 28Setting Up the Van Dyke Workstation
05:20 29Van Dyke Paper and Coating
05:10 30Van Dyke Exposure and Developing
32:30 31Van Dyke Troubleshooting and Resources
08:26 32Van Dyke: Split Toning
18:56 33Van Dyke: Wash Cycle and Drying
04:33 34Van Dyke: Clean Up Process
03:51 35Introduction to Platinum / Palladium Printing
14:15 36Platinum/Palladium Coating Chemistry and Safety
09:58 37Platinum/Palladium Paper and Coating Options
22:31 38Platinum/Palladium Exposure and Development
22:31 39Platinum/Palladium: Equipment and Supplies
16:48 40Ink Jet Negative Coating and Exposure
15:25 41Platinum/Palladium Chemistry Options
07:50 42Ink Jet Negative Development
03:45 43Platinum/Palladium Waxing Images
08:40 44Platinum/Palladium Troubleshooting and Resources
27:19 45Sharing Your Work Digitally
14:49 46Archivability
10:39 47Matting and Framing Options
30:22 48Editions and Signing Options
13:54 49Alternative Processes: Further Exploration
07:25Lesson Info
Introduction to Platinum / Palladium Printing
Platinum plating is one of my, like I said, it's one of my favorite alt-premium processes, and it's a great kind of, I think, pinnacle from what we've had because everything we've practiced to this point on the cyanotypes and the Van Dykes gets applied into the platinum process. But I wanted to cover a couple things, sort of just generically related to the alt-processing thing. I had mentioned a couple of times Christopher James' book on alt-processing and I said it was really thick. So this book has all sorts of details and so if you're looking for a great resource, one great resource. He covers processes that I didn't even know existed until I got the book. But I had just mentioned this, so I just wanted everybody to get a chance to see what that book looked like. For this process, we've been looking at a number of different papers. But this the Hahnemuhle paper we're gonna be using for today's process. So it's a beautiful paper, engineered by Hahnemuhle a while back. Specifically ki...
nd of tailored towards platinum printing. It works great for Van Dyke work and it works great for cyanotypes as well. It's a beautiful paper, so we'll be using that paper. The other nice part about this paper is you can coat either side. But I always coat the top. I swear I see a difference. But I think it's just me. But Hahnemuhle is engineered to be coated on both sides. Which not all paper is designed to be coated on both sides. So we'll be using that. So this is the Pictorico. I brought two different sizes. So this is 13 by 19. There is a Pictorico OHP transparency film and there's a premium. I would recommend you get the premium, it's a little bit thicker. Price-wise, it's just a dollar or two more on the overall packaging. But this is kind of what the package looks like. When you get the Pictorico, it will come with a little bit of a sealed, sticky part right there. And it's not like an easy tape, but you can kind of hear it as it rips open, that will actually stick really easily to the digital negative. And it will leave a residual mark that will impact your printing. But what's in here is the negatives are just in there as individual sheets between two pieces of cardboard. I recommend you leave them in the sheet, these are really sensitive to getting wet, they'll actually develop water spots really easily. So if you've got em laying around on a table, not in the protective cellophane, they will build up. There's that edge I talked about when we're talking about putting things into the printer, there's the notched edge to tell you that this front side notch in right hand, facing you, is the correct way to print. The other piece to really watch for with this and the reason I wanna bring it out is it's really easy to pull out multiple sheets of this Pictorico. It builds a static charge really fast and so sometimes you'll pull it out. You wanna make sure you flick the edge really hard just to make sure you're only pulling out one sheet because it will pull two sheets out really easy. But keeping things in a clean and organized with your Pictorico will save you time and money and frustration down the road. For the different sizes, we're gonna pretend like that's going back in. And the big one is to keep it off of that sticky edge because I've actually ruined a number of images where I pull em out and then I lay them down to stick the other pieces back in and they catch the edge of that tape piece. The other piece that's nice about the Pictorico box is you put the things back in, we talked about making that test strip to find your recommended amount of time, you can save the cardboard for that. It's not archival paper. It off-gases a little bit. So I wouldn't necessarily stick my negatives back in here for their storage, long-term. And also, it's pretty easy to flex and you can end up bending the negative. These boxes are a lot thicker, it's an actual cardboard box on the larger size. But it is the exact same piece, just in a bigger box. You'll have the exact same piece and it has the notch in the corner. So everything else is the same on the size. You can get them in roll size for somebody who's interested in printing really big you can get a roll size and work with that. So I just wanna quickly show you the different sizes for that, once we get under that box. Okay, so platinum printing has a really, really rich history and at one point, you could actually buy pre-sensitized platinum paper. It was one of the dominant kind of print methods in the late 1800s. Several companies actually sold it, you'd just go buy a box of paper, like you would silver gelatin paper. And then you could print with it. Silver gelatin came into fashion for a number of reasons. One, it was significantly cheaper, it was a little bit easier to work with and then World War I sort of happened and the biggest platinum mine in the world was in Russia and most of the platinum being used was used for some braking mechanism in tanks that were being built during that time. So most of the platinum got shuttled off for efforts in World War I. So the difference between the cost, the constriction of the supply and the fact that the dominant mine at the time was in Russia put a constraint into the platinum market and so for a number of decades, platinum printing, in a lot of ways, disappeared. Dick Arentz created a book and kind of re-engineered and re-figured out a lot of the platinum printing out of the old journals and wrote a book on platinum plating printing and kind of reintroduced the science behind it and the testing behind it and has in many ways, caused a resurgence. There are a lot of very simple, but subtle differences in the way we print platinum and palladium and overall, the biggest reason that people kind of switched to palladium is cost. So this is a 100 milliliter jar of palladium solution, sodium chloroplatinate, I think is how you pronounce it. I can never say the actual chemical name, but that is 100 milliliters. That's about $320, $330 of palladium. If that's platinum, that's almost $1,000. So from a cost standpoint, that's a lot of the reason people switch to the palladium market. You could still get platinum, you can still work with platinum. I actually have, that's my little jar of platinum. I buy palladium and I buy platinum. They have a completely different and distinct look. So the palladium is gonna have a little bit more of a warmness to it. It has a little bit longer scale. The platinum is a little bit cooler. It has a little bit different contrast, creates a little bit different dmap. So there's a little bit of a look difference between them. They're an interchangeable chemistry because of how they sit on the periodic table. You can use drops of palladium and drops of platinum together and kind of mix the results between the two. And so, my tradition of printing when I was printing before, I always mixed a little palladium and a little platinum together. And so my prints were actually platinum palladium prints. The other thing that most people, I think, when they talk about platinum printing, they're also including palladium printing in there. They just refer to it as platinum printing because that's what we originally used. So you'll hear those words being used interchangeably. Platinum, palladium, it could be palladium, platinum, it could be a combination of the two or it could be one or the other. The process I'm gonna show, the main process we're gonna look at today is a method that actually incorporates platinum and palladium together into the same mixture, through a contrast agent. So we'll be using the mixture you get and the mixture that's included in the kit from Bostick and Sullivan, has a platinum component to it. It's interesting in the art collection community, from a fine art standpoint, there is something about the nature of a platinum print that kind of, I think, has a hallmarkness to the past that people kind of resonate with. So in some ways, it's kind of nice the method we're using for digital negatives. And we'll talk about why we're using that method. It's nice that it actually incorporates the platinum into the process. Overall, the setup and work for the platinum is very much the same in the coating process and in the exposure process. But, platinum is what's called a development out process. And so before, when we pulled the prints out from cyanotype and we pulled out the Van Dyke prints and we looked at those, those are pretty much done and completed photographs and photographic prints from the time we looked at them. Now they went through subtle changes as they got tone and as they got fixed, they got a little bit darker. But when we pulled the photograph out, we could see the entire photograph. A development out process requires a developer to complete the creation of the print process. This is also one of the reasons I'm so excited. My favorite thing in all of analog photography is to watch a platinum print develop. So this is our very sophisticated development tool. That was the cheapest coffee pot I could get from the supply store. Because the temperature of that developer is important and we'll talk a little bit more about that later. But the coffee pot there, or our hot plate is there to get the temperature of the developer up because we want it to be a certain temperature. But the development of the print is gonna happen when we pour the developer over the print. And the reason I love platinum printing is it's an instantaneous development out process. So if you've worked in the silver gelatin world or in the traditional analog world, or my other analogy is if you print digitally, if you print digitally you do this to watch it print, cause that's what the print head does. If you're in the analog tray with silver gelatin, you move the tray and over the course of about a minute or two minutes, your print slowly emerges. Platinum, it's instantaneous. So when we pour that developer, we'll instantly see the print emerge. So it's a really exciting, kind of cool process. If your print is going well, if you've underexposed or overexposed, you instantaneously know that it might as well go into the trash. So you save yourself some time in that process. So that's the real big, significant change. And that's why also, it's our last process we're gonna look at. Is you're now getting to see the difference between the print out process and the development out process, you'll get the both from the coursework we're doing. Just like with the other processes, this is a gold toning kit. So you can tone platinum prints, they will get a little bit of a coolness to them and then they'll turn in plumy and if you leave them in for too long, they turn almost a purple. But you can get a gold toning kit. Same piece, I've got a little plastic cup. You can see it's labeled gold. It goes in a gold toning kit which goes into my platinum Rubbermaid tin. So like I said, every single process has a Rubbermaid. So all my platinum related stuff just lives in here. Including the runaway gold cup. I'll leave those out because we'll talk about those in a little bit. This I mentioned earlier, was the tween 20. So that tween 20 is just a little bit of a solution, like a little bit of a soap solution mentioned in the cyanotype portion that we could coat the paper in if it needed. Certain papers needed to have that surface tension broke, so you could use tween in your mixture. Or you could use distilled water and lightly coat the area ahead of time. The tween is basically one drop of tween in the amount of solution she uses. It doesn't matter if you're coating four by five with 12 drops or you're using 20 drops, you're just gonna put in a drop of tween, into the solution, that helps break the surface tension. But it comes in a bottle about that size and this will, literally, last longer than you'll probably need it. So everything goes in that kit. Same coating surface. So there's no other significant change, at this point, to how any of the process is gonna work. Hey Dana, can you grab me a paper towel from over there, if we have one? We don't. So, the other piece, as you'll see I have this little wooden tray that I've created and what it has is just a series of holes that have been drilled, that are the size of the bottles. There's more than necessary, because depending on how much of the process I'm using, I can have multiple bottles there. But the bottles are in there because this process chemistry goes in a certain order. And so I wanted the chemistry bottles to be presented in a certain order so I wouldn't forget where I was in my process. Oh, thank you. The other reason I do it is I mentioned the price of the platinum and palladium, that got built when I dropped a bottle of platinum. And so I literally watched about $ hit the floor and spill. And then I thought about, oh my gosh, can I scoop it back up? No. So I then devised this little gizmo for drilling the holes in. But that's all that is, there's nothing special about it. If you're not clumsy like me, you won't need that. But if not, it's just a little fostner bit into the drill for those various pieces. I've thought about building one for the bigger bottles too, 'cause I know at some point I'm gonna drop the really big expensive bottle. That will happen. But that's all that is, so just up there. When we're also working with this, you're gonna wanna use your synthetic brush. So we added the hake brushes when we were using the cyanotype process and we're using the Van Dyke process. And you could've used the synthetic brushes then. But we wanna go ahead and use the synthetic brush and a lot of that is because of the volume of chemistry that would be absorbed by the brush. A cyanotype chemistry kit is gonna cost ya $30, that's gonna cost you $1,000 if you're working in platinum. So you don't want the brush absorbing a bunch of that chemistry. It also gives a much, I think, smoother coating with the chemical process with the platinum and palladium. When I started, I didn't know any different, so I used a hake brush. I mean, the hake brush works fine, it's just gonna take up more of the cost and more of the money.
Class Materials
Bonus Materials with Purchase
Ratings and Reviews
Diordna
For a long time, I have read, studied and tried alternative processing, mainly Platinum/Palladium printing. I want to create longest lasting prints and may be share the info at Creative Live. But this presentation saved me many a hours. A few minutes into the lecture, I purchased the class and as the class progressed, I was extremely glad. Thank you Creative Live, thank you Daniel Gregory.
SFX
Excellent class on Alt Process and fantastic bonus materials included with purchase!!! I have extensive digital printing and darkroom experience but haven't done much alt-process to date. This is perfect timing for me as I have several personal projects that I would like to re-visit using some of these techniques. Thank you Daniel!!!
James H Johnson
I have been making platinum/palladium prints for about 1 year. This is the 3rd workshop that I have attended. The first two were one on one. Daniel has done a fantastic job of covering the material and explained the process it detail and easy to understand. This course is fantastic and highly recommend it.