Van Dyke Paper and Coating
Lesson 29 from: Introduction to Alternative Processing in PhotographyDaniel Gregory
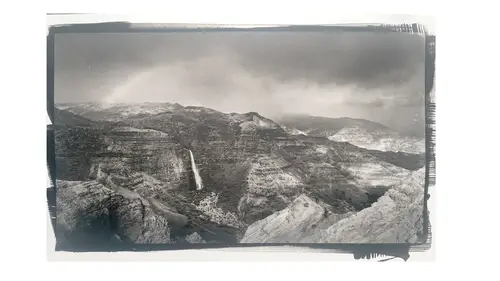
Van Dyke Paper and Coating
Lesson 29 from: Introduction to Alternative Processing in PhotographyDaniel Gregory
Lessons
Class Introduction
03:03 2Overview of the Alternative Process
03:31 3Overview of the Digital Negative Process
10:21 4Working with Black and White Digital: What You Need
09:17 5Working With Black and White Digital Images: Color Settings
08:33 6Working with Black and White Digital Images Lightroom
07:01 7Working With Black and White Digital Images Photoshop
11:57 8Working With Black and White Digital Images 3rd Party Plug-ins
07:29Avoiding Key Artifacts
20:26 10Creating the Step Wedge for Curve Corrections
39:00 11Organizing Your Adobe® Photoshop® Files and Curves
11:20 12Setting Up the Printer
20:24 13Lab Safety and Workspace Set-Up
03:49 14Setting the Maximum Black Time
12:06 15Getting the Initial Curve Test Numbers
20:04 16Correcting the Curve
20:37 17Printing the Curve
06:08 18Sharing Curves
08:50 19Caring for the Digital Negative
12:29 20Intro to Cyanotypes and Safety
07:46 21Paper and Brush Types
05:08 22Coating Process and Cyanotype Chemistry
12:17 23Making the Cyanotype Print
06:41 24Washing the Cyanotype Print
12:29 25Creating Cyanotypes Photograms
14:59 26Toning Cyanotypes and Cleaning Up the Darkroom
18:43 27Introduction to Van Dyke Printing
04:36 28Setting Up the Van Dyke Workstation
05:20 29Van Dyke Paper and Coating
05:10 30Van Dyke Exposure and Developing
32:30 31Van Dyke Troubleshooting and Resources
08:26 32Van Dyke: Split Toning
18:56 33Van Dyke: Wash Cycle and Drying
04:33 34Van Dyke: Clean Up Process
03:51 35Introduction to Platinum / Palladium Printing
14:15 36Platinum/Palladium Coating Chemistry and Safety
09:58 37Platinum/Palladium Paper and Coating Options
22:31 38Platinum/Palladium Exposure and Development
22:31 39Platinum/Palladium: Equipment and Supplies
16:48 40Ink Jet Negative Coating and Exposure
15:25 41Platinum/Palladium Chemistry Options
07:50 42Ink Jet Negative Development
03:45 43Platinum/Palladium Waxing Images
08:40 44Platinum/Palladium Troubleshooting and Resources
27:19 45Sharing Your Work Digitally
14:49 46Archivability
10:39 47Matting and Framing Options
30:22 48Editions and Signing Options
13:54 49Alternative Processes: Further Exploration
07:25Lesson Info
Van Dyke Paper and Coating
Okay so I have my papers ready to go, synthesizing solutions done, I've got my paper marked and now I'm ready to go ahead and start the coating process. So can we go ahead and flip the lights and we'll get into the dark room through the magic of technology; poof, just like that. Okay so we have some red. And what I'm gonna do is just like before, I'm gonna, I want my brush to be damp and but not wet so I've removed the pieces from that and now for a four by five you're gonna need about 12 drops. For a five by seven you need about 25, 30 drops but for an eight by ten about the size we're doing, we're gonna need 40 drops again. So we're gonna count them out. One, two, three, four, five, six, seven, eight, nine, 10, 11, 12, 13, 14, 15, 16, 17. Now to make it fun, eventually you'll be able to guess how many drops you have by how much solution's in the eye dropper; 18, 19, 20, 21, 22, 23, 24, 25, 26, 27, 28, 29, 30, 31, 32, 33. 34, 35, 36, 37, 38, 39, 40. Okay once that's done, I put the ca...
p back on so I don't spill it. Set that aside, just a little swirl for good luck, and then just like with the cyanotype I'm gonna go ahead and pour this towards the center and it's the same exact brush stroke as I had yesterday. It's an arm movement not a wrist movement. I wanna stay on the tips of my bristles so I get a nice even coating and I'm basically just moving the coating around so that it can be absorbed into the chemistry, or into the paper. So I'm gonna pour that and then I'm just gonna start coating and brushing and then as I go back and forth I come down to my mark and then I switch. It takes 30 to 40 seconds for all the chemistry to get pushed around and absorbed in this process and so same thing as before, you don't wanna get too far up into the over coating because you'll end up pulling up the fibers of the paper and it'll have a weird artifact; so once I've kinda made for my timing, it's once this way, once this way, once this way, and once that way, that's about my 40 seconds. If I'm going and I realize I've done this way, this way and this way and I'm at about 30 seconds, I don't worry about going back; I'm just trying to get that nice even coating. At that point my brush goes back into the distilled water so it can rinse out the chemistry that's in there. Set my shot glass and then I just kinda group everything together to try to keep the dark room nice and organized. And then this paper's gonna sit here for a couple of minutes without moving and what I'm doing is letting the paper rest. I wanna have some of that chemistry start to absorb in and the chemistry will actually start to self level itself a little bit into the paper so I wanna give it a chance for all that to kinda go in so if there is anything that is built up at the edges its got a chance to absorb. With the cyanotype we didn't do it yesterday, we'll demonstrate how to do it with a platinum print, but you basically can take that hairdryer I mentioned and you can work the back of a piece of paper and dry the paper more quickly to allow you to work at a faster pace. A Van Dyke process is one where you do not wanna use a hairdryer; the paper needs to dry naturally. The actual hairdryer and the accelerated drying can cause it to burn for lack of a better word. It causes a shift in the way the chemicals will process and the images don't come out correctly. The highlights are off, the shadows are off so it's a process that does require dry time and everybody wants to know well how long does it take to dry? If you live in Arizona, and it's 80 degrees outside in low humidity it's gonna dry faster than if you're in Florida with a high humidity. So in general it's somewhere between 30 minutes and an hour is usually how long it takes to coat, for it to dry. So we're gonna sit here for 60 minutes, no just kidding, we've coated about four or five sheets ahead of time, so that's one of the things with a Van Dyke process that I like to do, is I'll come in and if I know I'm gonna make three or four prints, at least three or four or five prints for the day, I'll come in and coat three or four sheets and then if the sessions going well and I'm moving through my paper at a quicker pace then I can always start coating some paper while image is in the light box. Get that coated, it can come back in and then I can let those papers dry naturally. The key is they can't be exposed to ultraviolet light while they're drying so you're gonna wanna put 'em in a dark corner; if they're just in your room with the chili peppers on, or the bug lights on, you can just set 'em aside and they'll dry as long as they're not exposed to window light or anything like that because it will fog the paper and you'll see it in the highlights.
Class Materials
Bonus Materials with Purchase
Ratings and Reviews
Diordna
For a long time, I have read, studied and tried alternative processing, mainly Platinum/Palladium printing. I want to create longest lasting prints and may be share the info at Creative Live. But this presentation saved me many a hours. A few minutes into the lecture, I purchased the class and as the class progressed, I was extremely glad. Thank you Creative Live, thank you Daniel Gregory.
SFX
Excellent class on Alt Process and fantastic bonus materials included with purchase!!! I have extensive digital printing and darkroom experience but haven't done much alt-process to date. This is perfect timing for me as I have several personal projects that I would like to re-visit using some of these techniques. Thank you Daniel!!!
James H Johnson
I have been making platinum/palladium prints for about 1 year. This is the 3rd workshop that I have attended. The first two were one on one. Daniel has done a fantastic job of covering the material and explained the process it detail and easy to understand. This course is fantastic and highly recommend it.