Platinum/Palladium Paper and Coating Options
Lesson 37 from: Introduction to Alternative Processing in PhotographyDaniel Gregory
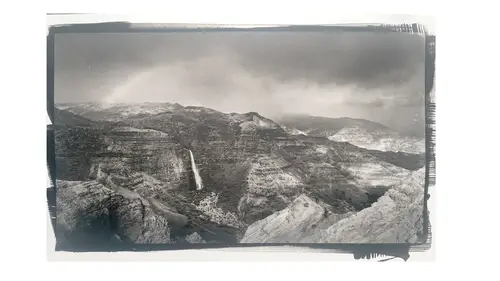
Platinum/Palladium Paper and Coating Options
Lesson 37 from: Introduction to Alternative Processing in PhotographyDaniel Gregory
Lesson Info
37. Platinum/Palladium Paper and Coating Options
Lessons
Class Introduction
03:03 2Overview of the Alternative Process
03:31 3Overview of the Digital Negative Process
10:21 4Working with Black and White Digital: What You Need
09:17 5Working With Black and White Digital Images: Color Settings
08:33 6Working with Black and White Digital Images Lightroom
07:01 7Working With Black and White Digital Images Photoshop
11:57 8Working With Black and White Digital Images 3rd Party Plug-ins
07:29Avoiding Key Artifacts
20:26 10Creating the Step Wedge for Curve Corrections
39:00 11Organizing Your Adobe® Photoshop® Files and Curves
11:20 12Setting Up the Printer
20:24 13Lab Safety and Workspace Set-Up
03:49 14Setting the Maximum Black Time
12:06 15Getting the Initial Curve Test Numbers
20:04 16Correcting the Curve
20:37 17Printing the Curve
06:08 18Sharing Curves
08:50 19Caring for the Digital Negative
12:29 20Intro to Cyanotypes and Safety
07:46 21Paper and Brush Types
05:08 22Coating Process and Cyanotype Chemistry
12:17 23Making the Cyanotype Print
06:41 24Washing the Cyanotype Print
12:29 25Creating Cyanotypes Photograms
14:59 26Toning Cyanotypes and Cleaning Up the Darkroom
18:43 27Introduction to Van Dyke Printing
04:36 28Setting Up the Van Dyke Workstation
05:20 29Van Dyke Paper and Coating
05:10 30Van Dyke Exposure and Developing
32:30 31Van Dyke Troubleshooting and Resources
08:26 32Van Dyke: Split Toning
18:56 33Van Dyke: Wash Cycle and Drying
04:33 34Van Dyke: Clean Up Process
03:51 35Introduction to Platinum / Palladium Printing
14:15 36Platinum/Palladium Coating Chemistry and Safety
09:58 37Platinum/Palladium Paper and Coating Options
22:31 38Platinum/Palladium Exposure and Development
22:31 39Platinum/Palladium: Equipment and Supplies
16:48 40Ink Jet Negative Coating and Exposure
15:25 41Platinum/Palladium Chemistry Options
07:50 42Ink Jet Negative Development
03:45 43Platinum/Palladium Waxing Images
08:40 44Platinum/Palladium Troubleshooting and Resources
27:19 45Sharing Your Work Digitally
14:49 46Archivability
10:39 47Matting and Framing Options
30:22 48Editions and Signing Options
13:54 49Alternative Processes: Further Exploration
07:25Lesson Info
Platinum/Palladium Paper and Coating Options
Okay, so. When we get the paper, one of the other things I like to do is I always like to leave my paper in the original packaging it came in. These papers all look and feel a little different. And so, you get em out, you think, oh I can definitely remember what that paper looks like. I can't remember what that paper looks like. Well you come back in six months, if you pull them out of the package and throw them into the drawer you won't have any idea. So I always like to leave them in the original packaging as much as possible. If they're not gonna be in the packaging, you definitely wanna write down on the back of the paper what it is. The other one is, these, most of the papers will either come in a plastic bag or they'll come in a wrapped up paper like this, so basically I just split it open so that I can get to the paper as easily as possible without having to bend or fold the paper. So I like to get it where I can open this up because then I can fold it back up and keep it from g...
etting dirt on it and keep it from getting dirty. The other thing they will do is sometimes they'll be a cardboard backing, the hahnemuhle does not have that, but sometimes there's a cardboard backing and you'll pull up a piece of paper and you'll be like, "That looks a little weird." Just know that there's a cardboard backing and that's to help it keep stiff during transport and to keep the pages from getting bent. The other piece you wanna be really careful about when you're dealing with the paper, particularly in the hahnemuhle, which is a square cut paper, cause there is no deckled edge. So any bend or fold in the corner is gonna show up and it's sometimes hard to smooth that out. So you're gonna wanna be careful and make sure you treat your paper accordingly. And then I basically fold that up and then I just flip it over so that it's protected like that. I always leave this away from my coating station, away from the chemicals. This actually sits outside my darkroom area and I bring in one sheet at a time. This is just to save money. If I spilled something on this by accident, I just have lost basically the chunk of paper. I mean I might be able to cut it in half or something like that, but I'm trying to save the paper. So I usually leave it outside the darkroom as a part of the process. Okay, I'm gonna get my edges theoretically coat-- taped down here. All right, we're gonna pretend-- Oh, I can get that one. I saved it, there we go. Tape down the edge of my paper, and just like before we're going to grab a platinum negative here and uh, let's make a buffalo. So we've got uh an American Bison Buffalo here. So I'm gonna put my negative down and just like before, I'm gonna kinda try to center it and I'm gonna watch my height top to bottom. I'm gonna try to weight a little bit to the bottom. The reason for that is, we'll see it in practice in uh, later, when we talk about matting and framing but we wanna have that little bit of weight to the bottom. That creates the optical allusion that the print's actually gonna be centered. It's a weird thing, if you actually center the image in the paper and then you hang it on the wall, it will actually appear low. So we raise it just a tiny little bit and then just like before, we're gonna tick our edges. I always mark my corners as well. And one of the questions I often get asked is, "Well what do you do about those pencil marks showing up?" One the print's dry, you can come in and as long as you have a good eraser, not a cheap one that makes little weird black marks on a piece of paper, as long as you have a good eraser you come in and you can erase the pencil mark. The platinum is actually gonna sink right through the pencil mark on the paper and then when you lightly erase it, as long as you don't get crazy-- (grunting) Just lightly erase it, it will take the pencil mark off and leave the platinum coating underneath and nobody will see it. Okay, so I've got my pencil mark. When I'm working with platinum, because, it's expensive, I make my marks, I usually give myself a 20 second distraction, and then I always go back and just double check and make sure that if I coat, that I got the right one. And like I have missed my corner here, I need to actually come up a little higher. So I'll mark that. And then when I erase that I just make sure I've got all of my edges off of there. And I just don't want to inadvertently miss a corner. With this process, if I know I'm gonna complete the edges, I absolutely wanna make sure I get to my edges. So I've got that. I've got my shot glass. It's been completely thoroughly cleaned and washed. I wanna make sure I have absolutely no chemical contamination. And again, I have my brush. It's been soaking. And so the same process, I'm just gonna make sure I get as much of the water out of there as possible. And you can see even with this brush that color watre is, I just didn't get it fully cleaned out last time. So the only thing this brushed gets used for is platinum palladium printing and I don't worry about the contamination between the platinum and the palladium. I guess if I was really anal I would and have two different brushes but since it's platinum and palladium you know, mixed together in our solution I already don't have super control over that so I don't worry about that too much. Okay, so... Now I've got that and then I've gotta think about counting drops again. The most important part of the drop counting process here is that the amount of drops you use for solution number one, which is Ferric Oxalate solution number one, is the same as you use for the palladium solution number three. Those two drop counts need to be the same. So if you're gonna use 14 of this, you're gonna use 14 of this. So those drop counts really need to match. That's the only really critical part in the counting. And then we have to decide on this one how much of the sensitizer we're gonna use. And like I said, there's recommendations in the handout, there's recommendations on Bostick & Sullivan's site, and pretty much anybody who prints in platinum who has this has an opinion about the correct number of drops and it's a little bit of an experimentation but because of the digital negative process, what matters is the consistency. So 10, 10, 4, as long as you're in that kinda ratio it's okay. If for some reason your curve looks good and you notice that, oh when I print it a little smaller it looks like my contrast is a little bit off, it might be you could reduce the drops from four to three and do a little bit of control in the chemistry. That's a little bit of trial and error. I, because of my background in coming from this I do a little bit of the freeform work with the chemistry that if I'm changing sizes and I notice a change like, wow the curve it looks different, cause I've gone up in size, I'm gonna let the chemistry control that by adding or reducing the drops. Because rather than go back through the entire calibration process, maybe a one drop change in that NA2 solution gets me my curve back to the right spot. So, what we're gonna do is count out the drops and then I'm gonna make the coating. I have over the years prepared myself for what I call the sacrificial paper and the sacrificial chemistry. For some reason, I don't know if it's cause of my angst, my nerves, but I always feel like the first piece of paper I coat in the platinum process never goes well. Oh, can you bring me a q tip too if you can find one in there? It just never goes well. I either have sucked up too much chemistry into the brush, I have missed the corners, I've gotten distracted and things have rolled weird. So this is gonna be the sacrificial paper. Now that doesn't mean I don't print with it, it just means it doesn't look good. And I've learned to accept that over time, that's just a part of my process. That way I'm not grouchy about it, I just accept it. So, I would encourage you if you find yourself with any process being like, you know the first couple just never really work... That's just setting the tone. And just know that that's gonna be the case. The other piece I get out right before I'm gonna start my coating process, is I get out a q tip. Or a swab, whatever the generic name is. It doesn't have to be a q tip, you just need a little swab like this. One of the things that will happen, in the coating process of platinum, a lot of things get, can go wrong. A lot of things can happen. And we're gonna talk about some of the troubleshooting stuff in a little bit. But one of the early ones you can find is you will occasionally see little black specks or little black flakes appear in the coating surface. It's cause it's gonna be kinda this yellow-y orange look to it. And what you can do is if you see those black specks, because they will develop out as white points in the print, is you can take a q tip, and it's a little roll of the finger. So it's not a dab and mush. It's a little roll of the finger. And what you're trying to do is use the fibers of the q tip to catch that and pull that up off the paper. So as you touch the paper, you're just gonna gently kinda do a little roll and you barely wanna touch the paper. If you have to do it more than about two or three times to get it off the paper, just let it go. Because as you're starting to do that, you're gonna start pulling the fibers of the paper up and you're gonna actually make it worse by having not enough coating in this spot and this weird smudge mark. But you're just gonna go along and what that is just the particulate out of the metal is just starting to settle out. So you're just gonna take that little-- You may coat a hundred sheets of paper and never see that and then you'll see it for a sheet or two and then you won't ever see it again. But it is a common enough problem that you definitely wanna have that out and readily available. Your finger, a gloved finger is not gonna work. All that's gonna do is leave this really weird looking finger print in your print. The other pieces, I talk about in the Cynotype and Van Dyke process, about we coat and then it's all done. That's even more important in the platinum palladium process. Once that chemistry starts to hit that page and move in, it's absorbing deeper into the paper. If we then come back with the brush and we start to then fix what looks a little odd later, you end up with really uneven levels of chemistry across the page, and then all of your tones and stuff don't match properly because you have too much chemistry in one area versus another. There are some people who will do this in all of their processes. You can do it in a Van Dyke, you can do it Cyanotype, you can do it in a platinum print, you can do what's called a double coating process. Creates a little bit deeper black and also allows for sometimes a little bit more even coating. And there's some other things that it can do to help the process. We're not gonna demonstrate a double coating but if you were doing that or you've done that, you basically coat, let it dry, and then you literally just coat right back over the top. So it's gonna use double the amount of chemistry. For the process of using a digital negative, I don't think we're necessarily gonna need that as we experiment. But later on down the road, or if you read about that that's what they mean by a double coating. It actually happens during this part of the process. Okay, so. I get my workstation set up, I've got my brush damp but not wet, I've got my chemistry set up, I've got my negatives marked off, I've got the light table, the light table is turned on. The light box is turned on so that I have the information going there. At this point, I make sure my developer starts to heat up. So there's a... Several developers you can use for developing a platinum print. And we'll talk about the differences in a little bit. But that development of that temperature affects the tonal values, the warmness or coolness, in the actual way the platinum develops. So, if you warm it up we get a little bit warmer print. A little bit colder temperature, we get a cooler print. Certain developers need to be at a higher temperature for you to get the full contrast range. And so the other thing I do is I make sure that my coffee pot or hot plate is turned on at this point. I want that developer for the ammonium citrate, which is the developer we're using for the kit, I want that at about 90 degrees. People who are really anal retentive are like, "Does it have to be exactly 90 degrees?" 85, 95, somewhere in there. But if you make a print at 69 degrees then you make one at 100 degrees, your contrast is gonna be different enough that you'll think your curve is off. So again, what matters is, a little experimentation of what's it look like at 80 degrees, what's it look like at 90 degrees, and where do you kind of like the tonal values to look? And then pick that temperature. For me, with the ammonium citrate, it's around 90 degrees. That's why I've picked that one. I am printing with that. The ammonium citrate is also the least of all least toxic of the developers which is why I like to start off with that one. Don't drink it, but it's not super volatile. It also is the easiest to clear and to wash. That makes the washing cycle a lot easier. So, but I want the light box turned on so I get the UV temperatures up and I want this turned on so it comes to temperature. And I just keep an eye on that to make sure it doesn't run, because once it starts developing heat it goes really fast from 80 degrees to 120 degrees and then I have to wait for it to cool back down. You could use a water bath to cool it or to heat it. So what a water bath is, is you have a pitcher like this, say, and you put your developer in there and then you put that in another pitcher of water or another tub of water, and you heat the outside water to the temperature you want and then it will actually transfer the heat into the pitcher so that it goes to the right temperature. So if you end up with 120 degree water, or developer, you could use a cold water bath into another pitcher and then start to cool it down that way. That's another option, but it's way easier and way faster just to kind of keep an eye on the thermometer. The thermometer I've got is just a... That was almost a really bad idea. I almost used the paper towel for my coating brush which would have put the developer that makes the chemistry go away, on my brush. (audience laughs) Uh, this is literally just a instant read digital thermometer you'd stick in a chicken or meat or whatever at the-- I got from the grocery store. They make em with dials or whatever. I got the instant read out just cause it was instant read out and the price difference was like $2. But there is no fancy thermometer. Don't buy the fancy dark room thermometers, just literally anything that you can stick in and get a temperature on works for figuring out the developer temperature. So, we get that all set up, that gets put on, and now I'm ready to coat. So this process is sensitive to ultra-violet light, not quite as sensitive as the Van Dyke is but we'll go on ahead and we'll drop off and we'll put on to the red light so I can get the coating done. But before we do that, what we're gonna do is... After the coating's done it's gonna sit here for about a minute or two and then, Gina's gonna hit it with a blow dryer on the back side and we'll dry the back side of the paper, that's gonna help the paper dry faster, and we can use the blow dryer. In a well ventilated, well ventilated space we dry the back side of the paper, you hold the paper down away from you, you use the blow dryer, and you can pull it up. Anything that potentially fell off the paper would go the other way. But from a safety standpoint, usually when I'm drying like that I put a mask on. Just to make sure I don't breath in any of the particulate. So we'll dry that paper, so that lets us get into the UV exposure box quicker. Now, if you're working and you just wanna let it air dry you absolutely can do that. And I do in my own belief, in my own experience without measuring it on a sensitometer, I do think there is a subtle difference in how the tones develop by letting it air dry. Not so much that it overrides my patience and I want the paper right away, but there is a subtle difference. So, the, and that subtle difference is just a little bit in how those tones separate and how they pull themselves apart and present themselves in the final image. So I will coat sometimes like three or four sheets, five sheets at once, ten sheets if I'm gonna print for the day, and just set em in the drying rack and just let em air dry and then pull em off one at a time. But the key is they've gotta be dry because just like with any of alt processing, if I grab my negative, whether it's digital or traditional, and the palladium's not dry it will actually start to adhere into the negative and create these weird spots that show up in the print. Once that's done, then everything else is gonna be pretty much the same. So it's the one time we're actually gonna see the blow drying process. You could use that for a cyanotype, but you can't use it for the Van Dyke process. So let's go on ahead and make our sacrificial piece of paper here. And if we can switch the lights here to get back to the dark room lights. (clearing throat) So, for the coating area I have here I need about, uh, 28 drops, 30 drops, total in that range. My ratio's 10, 10, 4. So I'm gonna do 12, 12, 4, and that will hold my contrast there. So I grab the solution number one, and into my shot glass I do 12 drops. One, two, three, four, five, six, seven, eight, nine, ten, eleven, twelve. So close. Just a little bit left over. Like I said, you've gotta keep yourself entertained. So I like to play the suck up the exact amount number. Um... That was three. This is the next solution so, that was the palladium because I put it in the wrong order. Doesn't matter what order it goes in the jar. But this is 12 drops. One, two, three, four, five, six, seven, eight, nine, ten, eleven, twelve. I think thirteen just went in but we'll give it a free pass. Okay. Then I always read my labels no matter what the order is. So I make sure I have my 5% solution here, and then, one, two, three, four. Okay. So. I'm now gonna swirl that around because I wanna make sure that the two solutions mix. Actually I guess it's three solutions, mix. And then I'm gonna pour this into the uh, kinda the center of the piece, and then I wanna start working the exact same process I worked before. And then given the size, I have estimated how much I think I need for that size negative. So if it ends up I can't get all the way to the edge, then the next time we coat for that negative I would know I would need just a few more drops. So, I pour into the middle there. And then just like before, I start moving the chemistry. And you can see it starts to pool at the edges and I'm just gonna slowly move back and forth. Then I start going north to south and just again I'm up as far up under that edge of that brush as possible in the coating. Back and forth. Now I can see, I can see cause I'm close enough, where I'm starting to get a little bit to the... Edges didn't get quite developed enough but at that point I've gone back and forth enough that I'm gonna stop. And then, to see those black spots it's a lot easier sometimes to get down lower and it does not look like we have any black spots in the coating surface. But if you look... Uh, let's see what that is. That was a flick of paper, flick of paper. One of the things you will occasionally see at the edge is as you've transferred your brush it will drip. Let's see if I can get it to do it. Yep. It's held the chemistry. It will drop little drops at the edge and you'll be like, "Oh man!" (grunting) And then you'll... If the sensitizer touches the paper, it's on the paper. There's some things we can do after the fact if it's light enough we could try to like use an X-Acto knife and maybe cut it, nope. If it's on there you just leave it. It's a part of the artwork and it's one of the reasons you will print sometimes the same negative three times because something falls on the edge, you don't quite get the brush marks the way you like... In this case I've got a really nice brush mark that's gonna be right here. There's a nice feather end of a brush mark right here so that's kinda cool. I've got a nice little weird kinda edge down here. I didn't quite get to the full corner here. So this'll be an interesting spot for the negative to see what's down there and how that look is affected by the image. So I'm gonna kinda keep an eye and watch that. But now this is just gonna kinda sit here. This'll actually have a deep yellow. So when we looked at the cyanotype coating and we looked at the Van Dyke coating, that was kind of a lighter yellow. This has a deep, deep yellow. Almost a light amber, orangish color to it if it's, if the solutions are okay. So we're gonna go ahead and then we're gonna just let that sit. At this point in my normal process what I do is I come back, I make sure that there is nothing weird on the contact frame, so I would double check the cleaning on the glass cause if it sits here, the longer it sits here to dry the better. So I make sure my contact frame is clear. The other thing I do that is a, it's a little bit on the OCD side, but I flip up the light box, and you don't wanna stare at the light in there cause it's direct UV light it could damage your eyes, but I do take a quick peak in there just to make sure all the bulbs are still on. It is weird how sometimes a UV bulb will start to flicker, or not a UV bulb, a fluorescent tube bulb will start to flicker, and sometimes just reseeding it will fix that. But I wanna make sure I have a really even lighting source in there. So I'm doing that. I make sure my brush goes back into the distilled water because I don't want the chemistry to dry in the brush. So I make sure that that's back in there. Double check my time for my developer. And so now, I'm gonna pull this off and uh, we'll have Gina run a little bit of a blow dryer here. Do you want me to do it up here or do you want me to show em? You can do it over there if you've got an outlet. Yeah, I do. If not, you can come back over here. Okay, while she's drying that, before she brings it back for it to work... The other thing I do when that print's drying is I go back and I make sure all the caps are on and I take a paper towel and I clean out the shot glass or the plastic cup. Because I don't want any residual chemistry to dry in here so I make sure that that's just wiped out. If I've used the q tip, I throw the q tip away because it's gonna have dried chemistry in it now and I don't want that to pick up later. So in that drying process, I'm basically cleaning my coating station for the next part of the process.
Class Materials
Bonus Materials with Purchase
Ratings and Reviews
Diordna
For a long time, I have read, studied and tried alternative processing, mainly Platinum/Palladium printing. I want to create longest lasting prints and may be share the info at Creative Live. But this presentation saved me many a hours. A few minutes into the lecture, I purchased the class and as the class progressed, I was extremely glad. Thank you Creative Live, thank you Daniel Gregory.
SFX
Excellent class on Alt Process and fantastic bonus materials included with purchase!!! I have extensive digital printing and darkroom experience but haven't done much alt-process to date. This is perfect timing for me as I have several personal projects that I would like to re-visit using some of these techniques. Thank you Daniel!!!
James H Johnson
I have been making platinum/palladium prints for about 1 year. This is the 3rd workshop that I have attended. The first two were one on one. Daniel has done a fantastic job of covering the material and explained the process it detail and easy to understand. This course is fantastic and highly recommend it.