Platinum/Palladium Exposure and Development
Lesson 38 from: Introduction to Alternative Processing in PhotographyDaniel Gregory
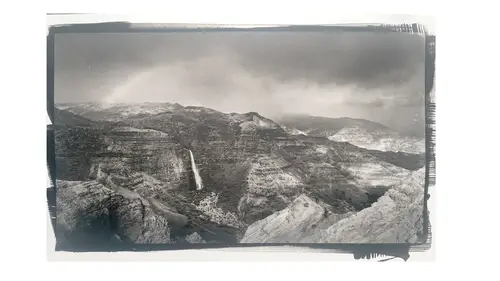
Platinum/Palladium Exposure and Development
Lesson 38 from: Introduction to Alternative Processing in PhotographyDaniel Gregory
Lesson Info
38. Platinum/Palladium Exposure and Development
Lessons
Class Introduction
03:03 2Overview of the Alternative Process
03:31 3Overview of the Digital Negative Process
10:21 4Working with Black and White Digital: What You Need
09:17 5Working With Black and White Digital Images: Color Settings
08:33 6Working with Black and White Digital Images Lightroom
07:01 7Working With Black and White Digital Images Photoshop
11:57 8Working With Black and White Digital Images 3rd Party Plug-ins
07:29Avoiding Key Artifacts
20:26 10Creating the Step Wedge for Curve Corrections
39:00 11Organizing Your Adobe® Photoshop® Files and Curves
11:20 12Setting Up the Printer
20:24 13Lab Safety and Workspace Set-Up
03:49 14Setting the Maximum Black Time
12:06 15Getting the Initial Curve Test Numbers
20:04 16Correcting the Curve
20:37 17Printing the Curve
06:08 18Sharing Curves
08:50 19Caring for the Digital Negative
12:29 20Intro to Cyanotypes and Safety
07:46 21Paper and Brush Types
05:08 22Coating Process and Cyanotype Chemistry
12:17 23Making the Cyanotype Print
06:41 24Washing the Cyanotype Print
12:29 25Creating Cyanotypes Photograms
14:59 26Toning Cyanotypes and Cleaning Up the Darkroom
18:43 27Introduction to Van Dyke Printing
04:36 28Setting Up the Van Dyke Workstation
05:20 29Van Dyke Paper and Coating
05:10 30Van Dyke Exposure and Developing
32:30 31Van Dyke Troubleshooting and Resources
08:26 32Van Dyke: Split Toning
18:56 33Van Dyke: Wash Cycle and Drying
04:33 34Van Dyke: Clean Up Process
03:51 35Introduction to Platinum / Palladium Printing
14:15 36Platinum/Palladium Coating Chemistry and Safety
09:58 37Platinum/Palladium Paper and Coating Options
22:31 38Platinum/Palladium Exposure and Development
22:31 39Platinum/Palladium: Equipment and Supplies
16:48 40Ink Jet Negative Coating and Exposure
15:25 41Platinum/Palladium Chemistry Options
07:50 42Ink Jet Negative Development
03:45 43Platinum/Palladium Waxing Images
08:40 44Platinum/Palladium Troubleshooting and Resources
27:19 45Sharing Your Work Digitally
14:49 46Archivability
10:39 47Matting and Framing Options
30:22 48Editions and Signing Options
13:54 49Alternative Processes: Further Exploration
07:25Lesson Info
Platinum/Palladium Exposure and Development
In terms of developers, your developer is gonna show up, and this is a potassium oxalate, is that what's in here Gina, is potassium oxalate? Yes. Okay. You're gonna have ammonium citrate. This is potassium oxalate. We'll look at ammonium citrate after. This is my normal developer. So this is the one I prefer to use. This gives a little bit warmer tone. So, I like this at a little bit higher temperature. I like this at around 100 to 110 degrees, is my preferred temperature for that. When you get this as your developer, what's gonna be in here is powder down here. You're gonna add a little bit of water, up to about here into there, and then you're gonna shake it, and get most of that to dissolve, and then you'll fill the rest of this bottle with water. And then you'll shake it until it dissolves all the chemistry. And it'll dissolve pretty quickly. And I just use like 70, just warm water. It can be hot water, it'll dissolve faster. But, warm water that you'd wash your hands with. You...
're gonna shake it, and then it's gonna be perfectly clear. And it will not be this color. And you did not do anything wrong. When you first get that chemistry it's clear. What this is, is it's seasoned. So it's got the history of all the prior platinum prints in it. So every time I've done a print, it goes in there, and it'll start to get darker, and darker, and darker. That's good. I am using, it's kind of like sourdough yeast, is the analogy I like to use. If you go have really great sourdough, and they're like it's from 100 year old starter. So they carve a little bit of that yeast off, and they use it again, and again, and again. Same thing here. We wanna actually have a longevity of our developer. Because it has that richness that's in there. So, it will get darker and darker over time, and then what you do is you mix up another, you'll get another bottle of oxalate, or ammonium citrate. You'll mix it up, it'll be clear, and then as you use the developer, you're just gonna add fresh developer into your old developer. And that's how you replenish the developer. What will happen to it over time though, is it will go through the process of getting kind of sludgy, and these little paper fibers will start to show up. And it's gonna get kind of chunky, for lack of a better ... It's just kind of, yeh. Stuff floats in it. It won't be mold or anything like that, but it's just stuff. So what you do then is, you take a coffee filter. And when you're pouring these back and forth, you'll have a funnel, you're just gonna pour it back in through the coffee filter. The coffee filter will pull out the larger particulate, and then you can go ahead and reuse it without the stuff floating around in there. It doesn't cause any real damage to the print. But that sludge in there will build up over time, and start to cause some issues with the developer. So, keeping it clean, just keeping it filtered, and I don't filter it on a regular basis. It's literally on an as needed basis, as the developer goes along. And that's true for the potassium oxalate developer, as well as the ammonium citrate developer. There are a couple of other developers. There's a cold developer. The cold developer creates a cooler temperature, and it works the same way. It'll come in a one liter size package with the solution so you can work with that one. Three or four different ones. But most people use either ammonium citrate, or they use potassium oxalate. The other thing you can do is kind of like them, because it's all processing, the way the chemicals work. I have a couple of bottles that are half potassium oxalate, half ammonium citrate. Mix them together and kind of see what happens. And it kind of gives you the best of both worlds. You get the contrast, but you get the tonal range. And that just came about because I was just curious of what happened if the two of them were mixed together. That's, to figure out how that answer was solved. When the developer is done, the only other thing to do is just to let it cool, back into 98 degrees before you pour it back into the plastic bottle. If you got it 120, 125, you'll start to weaken the plastic bottle. And it could, I could cause damage. I also like to keep anything that can stain a plastic bottle in a plastic bottle, (thumping) because if it falls for any reason. And there's nothing about this that the ultraviolet light is impacted by. Normal light, nothing, the developer is not impacted by anything. These are in the dark brown bottles, because we don't want them to be exposed to the ultraviolet light. Because that would impact the print for that. So that's kind of the process for that, on the developer. And here comes our piece of paper. So I'll grab the contact frame. When you're working with this, people want to know how to know when it's dry. That's the other question. You can feel the dampness on the back of the paper. And so a lot of times when I'm working in the platinum process, I have a glove on one hand, when it comes to the paper drying time, because then I can feel it. But the other thing I do sometimes is just pull my glove down a little bit, and I can feel on my hand if it feels damp. If the backside of the paper is damp, you're definitely the paper is not dry. And then you'll wanna dry it a little more. The other one when it's dry is it won't have any sheen to it. So you can kind of have it bounce around in the light a little bit, and if there's any sheen, it's damp. And then eventually you can kind of touch it, and you can kind of feel whether or not it's got any dampness to it. You can't overdry it. You can burn it with the hairdryers. So if you hit the hairdryer on high, you'll end up with these really dark splotches where it burned the chemistry. But on a cool setting, you can't overdry the paper, so you don't have to worry about that. So better to err on the side of overdry, but just a little touch of your arm even, if it just feels damp on the back, you want to avoid that. So the negative goes on. In this case, I've got a little extra coating up in that corner, and I was a little short down there, so I'm gonna try to center it. And I've got enough room that I can get the whole negative in there, and avoid that bad corner. Flip it upside down. Contact frame goes in. Pieces get put down. The other thing I like to do at this point, is, I wanna make sure that my negative is parallel to my paper. And in this case, you can see I went in, and the negative shifted. So now the edge of the negative, and the edge of the paper are no longer parallel. So that's gonna make a crooked print. So at this point, I'm gonna pull this back out. So that's one of the things I like to check before it goes in. Because if it's off for some reason, I just pull it out, and I can reset it. It's way easier to reset now, and get level and square, then it is to do after the fact where you have to trim the paper. So to keep it level, I'm just gonna keep my hands on both sides. Put it down and I put a finger in the middle, and then I go to the other side. And then that should square it up. The most number of times I've had to do and undo the contact frame to get it straight was six. And I'm very proud of that. And that's close enough that I'm not gonna start my record for seven, and we'll just stick it in there. So that's gonna go in. The time for the platinum printing is six and a half minutes. So I'll go ahead and set for six and a half. Let the clock go. So while that's going on, I've got six and a half minutes. So I start to think to myself, what's the most effective use of my time? Because when that comes out, it's gotta go into the wash cycle. So, in my standard workflow, the next thing I'm gonna do, is I'm gonna use every opportunity I can to coat paper. So I'm gonna grab my next negative. Ooh, let's do this one. I like this one. I like them all, I guess that's why I made prints out of them. But I'm gonna grab the next one, and then, if you're getting to where you're okay speed wise, you'll be able to start to get your prints coated in the amount of time your exposure is. If your exposure's about somewhere over five minutes, once you get practiced, one of the questions I get asked a lot is how fast can you coat? Once you get the rhythm down, you can start to coat pretty quickly and effectively, after you've been practiced. So when you're first going, I don't recommend trying to race the print you have in the ultraviolet light box, but once you get going, it's a really good, effective way to do your time. So I get my brush ready. I'm gonna count out the drops. This is the solution number one. One, two, three, four, five, six, seven, eight, nine, 10, 11, 12. This solution is actually yellow, if you look at it under normal light, and you can see it's kind of a brighter yellow. I'm gonna grab the number three solution. This is the palladium solution, and you can see it's a dark color. That's another way to spot check yourself, when you're doing your chemistry, to make sure you haven't double chemistried the same thing. A light chemistry yellow, and then the darker palladium. One, two, three, four, five, six, seven, eight, nine, 10, 11, 12. Five drops of this. One, two, three, four, five. And then we give it a swirl. That goes in. And then we start the brushing process. I always start from the middle and work my way up, and then I just come back down and pick it up. Some people will pick up the bottom or the top. And then I have a lot of chemistry there. That's just gonna get picked up in that process. So, if the chemistry pools somewhere, don't worry about it. You'll pick it up in the next set of brush strokes. Don't get obsessed and focused on trying to fix one area. And I usually do back and forth a couple of times. Once that chemistry starts to dry, anything beyond that is just a damage to the surface of the print coating. So, that gets done like that. That gets set aside. And, I could literally coat another piece of paper. So I use that UV light box time to stay efficient, by coating over and over again. The other piece I wanted to show you while we're waiting on that print to come out, is this is platinum. This is the palladium. So that color method, you can see that the palladium on this side is darker. Actually Gina, can you come grab a sheet of paper? Just any sheet of paper, or that box of Puerto Rico. Just a piece of paper, I just need to hold this in front of a piece of paper to show the color. Just need something white. Yeah. So you can see the platinum has got a lot lighter color than the palladium does. So in that whirl of keeping yourself organized, and keeping yourself straight, if you see this lighter color, you know you've got platinum. So if you're a person who's got both sets of chemistry going, in keeping yourself organized, that color is a really good indicator of how to keep yourself sane and organized in the dark room, because you're gonna be able to work, and see like wait a minute, I already did yellow. I'm expecting the palladium, a darker color, but I've got this hot pink kind of color. That's because the platinum's been picked up. So, keeping that piece is I think a really important part of the process. Okay. Let's, we're gonna need a development tray, a wash tray, and an EDA tray. So, we're gonna start the process for developing the sink now. So I'm just gonna move this stuff aside, so we can coat here in a little bit. You want me to keep all the coating stuff? Yeah, keep the coating stuff because I'm gonna coat some more. For the actual chemical part to work, you're gonna have a lot of trays. So, we're gonna need a tray for the developer. We're gonna need a tray after the developer, that it's a light washing tray. It's not required but I recommend it, because it'll make your actual chemical baths last longer. Then you're gonna have a bath that's called EDTA. It's a clearing agent. Terasodium EDTA. I have goal in life- To be able to say that. Of eventually being able to pronounce EDTA. It's about that long. It's ethodiochloral ... And it's this crazy long name. And it's a clearing agent. And one of the reasons I like platinum palladium, is I like the safety of the chemicals that are used. There's not a lot of really caustic chemicals. This is the heaviest thing we hit in the clearing bath, and EDTA is used to bond metals out of soluble solutions. So it's actually a food additive. It's used in agriculture. It's used in chemical cleanups. It's used in all sorts of things. It's a pretty safe chemical that gets used. And, it's in powder form. And it gets added in to the water. So it's about two tablespoons per liter of solution. So we basically just take that two tablespoons and we add it into the solution. So you have a two liters there, don't we? I have two liters. So I have one, two. Add that in. That's then gonna make my clearing bath. I have three of these clearing baths of EDTA. That's what's removing the last of the residual metals from the chemistry. Can you agitate and get the EDTA all setup? Okay, so we're gonna pull the print out in a couple seconds here. And then we will, our developer's at 95 degrees, so we're close enough. We pull the print out. And there's our image. So this is why it's called a development out procedure, because there is no image. What we're looking for is, what you're looking for is the slightest hint of the shadows to be there. Because you're seeing the black develop out here. And if you're up close, you can start to see the edge line of our little buffalo starting to come out in the print. So basically we put that in the development tray. We grab our heated developer. You're gonna lift the lid. And this is the part that is the only really thing you gotta get a good motion on. It's kind of like the coating process. It is one fast steady pour across the whole print, as a quick motion. It's not a drizzle part, or it will develop the drizzle line. So it's basically just a nice even pour across the whole image, and then it's a pretty much instant development out. So here we go. We're gonna go across, and it just pours. And there's our buffalo. So at this point, the image is basically done. So we can actually ... Let's flip this upside down. Can you hide that over there? And we can turn on the regular lights now, because we can watch through the regular process. This gets a minute to a minute and a half in the development tray. So, while it's a development out process, and it pretty much instantly appears, we want to let all the tones have a chance to fully develop. And so while you watch it, you'll see the shadows will just get a little bit deeper and deeper, and a little bit richer, and the midtones will start to separate a little bit. So, we've got about 90 seconds in here, to let that fully develop. Two minutes. You read, some people are a minute, some people are two minutes. Hence I'm 90 seconds. I figure, if half the people are too short, and half the people are too long, somewhere in the middle has gotta be okay. So we go for about 90 seconds. It's important again that you have the constant agitation at this point. So you wanna make sure the developer is moving consistently and evenly and randomly, across the entire print. Alright, so while this is going, do you guys have any questions to this point? If you were to get enthusiastic with your brushstrokes, and it went past the edge of the negative, would that create a line? If you got, like you went, you would end up with a line kind of like that, farther out, is that what you're asking? Yeah, would the negative edge create a line. Yeah, so anything, anywhere that chemistry touches the paper, leaves a line. Yeah, a straight line where the negative edge would be, yeah. Can you remind us what the name of the book was that you mentioned, the name of the author Yes, the name of the book is Christopher James is a genius. No. (laughs) Let me get that into the wash. Sorry. The actual full name of the book is, The Book of Alternative Photographic Processes, Third Edition by Christopher James. Thank you. And it really is just an amazingly deep resource. He's got history, and variations, and there's literally processes in there I'd never heard of until I got his book. And really, really good. I'm so glad that he spent the time to do that. So now you can see we've got a really cool buffalo, taken from inside the car, out through the window. Following the rules of Yellowstone. Now, you can see here, there's a white spot. And these little white line marks. Those little contusions are from where the paper didn't get coated. So the brush as it came across, I missed a little gap there. That is a part of the alt process. So, I wouldn't necessarily reject this print, as not being a completed and fine final print, because of that mark. That is in the artistic part of the process. So, this has been in there for a minute. The only reason I use this water bath right here, it's not required for anything else. It just it helps wash off some of the residual developer, and it makes my bath where the chemicals are, the thing that I've actually paid for, last a little bit longer. So this is gonna sit in here, and agitate for about five minutes. This first bath gets very consistent, constant agitation. And what we're doing is clearing off the last of the residual salt. So that paper has got a yellow, orange, amber quality to it. And it's starting to wash off the residuals of that. And it's hard to see, because the print's actually developed, but there is a little bit left in there. Over time, this bathwater will start to turn yellow. So, I've got the white paper, and you start to move it back and forth, and then you'll notice there's this yellow color moving back and forth across the print. That means it's about time to change this bath out of there. So what happens is, you're gonna take, this is your number one wash bath. Then here is another tray of EDTA. And then here is another tray of EDTA. You're then gonna take bath number one, and dump it. Bath number two gets promoted to bath number one. Bath number three gets promoted to bath number two. And brand new bath number three gets developed. In theory, after bath number one, the print has been completely cleared of any residual salts that need to be removed. The last ones are gonna make sure it's completely removed and archival. That's why having that last bath be your new one, makes sure that that's got the highest concentration of the EDTA in it, and it's able to remove anything that's left. After that, it goes into another wash, and that wash is gonna last 20 to 30 minutes. And then that completes the processing cycle. So that's why this takes a little bit of time. You've got coating, time in the light box, developer, awesome cool, minute, five minutes, five minutes, five minutes, and then 20 minutes. And in the wash, they don't need agitation unless you don't continually running water. And then you'd need to agitate the prints. But, a little movement back and forth. And this print is done. This is where it's at in its state. It's ready to go. It's not gonna get any darker. It's not gonna get any lighter. There's no real perceived change in this, except one of the things Gina and I are gonna show you how to actually increase the blacks a little bit with some cool little stuff in the next segment. The thing I really watch for, in the platinum print, is I look in my deepest shadows, and I like to make sure I still hold a little of texture and a little bit of detail, and then I make sure I've got the details and the highlights. The range of a platinum, if you think about a silver gelatin negative, having about 10 zones, the ability of a platinum print to hold about 12 to 14 zones, in that range. That's why we have a higher contrast negative. So the curve's got a little bit more steepness in it than some of the other alt processes, is to help hold that. Do you have an estimate cost per eight by 10? Just ballpark. So, many years ago, I had dreams of owning a car. (laughter) And instead what I own are stacks of platinum prints. That's a great ... So, the price varies a little bit, because of the type of chemistry you use, and we'll talk about that a little bit more in the next segment. In general, I figure it's about between five and seven dollars to do a eight by 10 platinum print. And that includes the cost of the paper, cost of the chemistry, cost of the actual, amortized cost of all the other chemistry. I run a business. I'm a photographer, I have a business, that's how I make my living. So, I literally could tell you down to the penny, amortized out based on the square inch what everything costs, but in general it's gonna be somewhere between seven and 10 dollars, is what I'm paying, but, my palladium I bought, was when people freaked out in the economy, and heavy metals went up, and that happened to be when I needed platinum. So I was paying literally 200 dollars more a bottle for the platinum, because the raw chemistry cost was higher. So as the movement cost of the chemicals changes, the price changes.
Class Materials
Bonus Materials with Purchase
Ratings and Reviews
Diordna
For a long time, I have read, studied and tried alternative processing, mainly Platinum/Palladium printing. I want to create longest lasting prints and may be share the info at Creative Live. But this presentation saved me many a hours. A few minutes into the lecture, I purchased the class and as the class progressed, I was extremely glad. Thank you Creative Live, thank you Daniel Gregory.
SFX
Excellent class on Alt Process and fantastic bonus materials included with purchase!!! I have extensive digital printing and darkroom experience but haven't done much alt-process to date. This is perfect timing for me as I have several personal projects that I would like to re-visit using some of these techniques. Thank you Daniel!!!
James H Johnson
I have been making platinum/palladium prints for about 1 year. This is the 3rd workshop that I have attended. The first two were one on one. Daniel has done a fantastic job of covering the material and explained the process it detail and easy to understand. This course is fantastic and highly recommend it.