Setting the Maximum Black Time
Lesson 14 from: Introduction to Alternative Processing in PhotographyDaniel Gregory
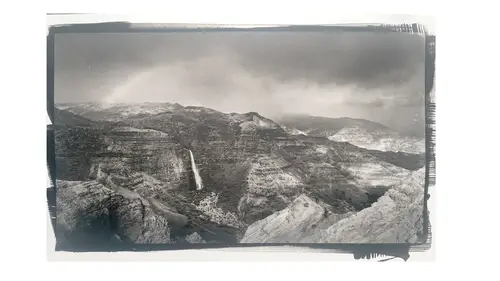
Setting the Maximum Black Time
Lesson 14 from: Introduction to Alternative Processing in PhotographyDaniel Gregory
Lessons
Class Introduction
03:03 2Overview of the Alternative Process
03:31 3Overview of the Digital Negative Process
10:21 4Working with Black and White Digital: What You Need
09:17 5Working With Black and White Digital Images: Color Settings
08:33 6Working with Black and White Digital Images Lightroom
07:01 7Working With Black and White Digital Images Photoshop
11:57 8Working With Black and White Digital Images 3rd Party Plug-ins
07:29Avoiding Key Artifacts
20:26 10Creating the Step Wedge for Curve Corrections
39:00 11Organizing Your Adobe® Photoshop® Files and Curves
11:20 12Setting Up the Printer
20:24 13Lab Safety and Workspace Set-Up
03:49 14Setting the Maximum Black Time
12:06 15Getting the Initial Curve Test Numbers
20:04 16Correcting the Curve
20:37 17Printing the Curve
06:08 18Sharing Curves
08:50 19Caring for the Digital Negative
12:29 20Intro to Cyanotypes and Safety
07:46 21Paper and Brush Types
05:08 22Coating Process and Cyanotype Chemistry
12:17 23Making the Cyanotype Print
06:41 24Washing the Cyanotype Print
12:29 25Creating Cyanotypes Photograms
14:59 26Toning Cyanotypes and Cleaning Up the Darkroom
18:43 27Introduction to Van Dyke Printing
04:36 28Setting Up the Van Dyke Workstation
05:20 29Van Dyke Paper and Coating
05:10 30Van Dyke Exposure and Developing
32:30 31Van Dyke Troubleshooting and Resources
08:26 32Van Dyke: Split Toning
18:56 33Van Dyke: Wash Cycle and Drying
04:33 34Van Dyke: Clean Up Process
03:51 35Introduction to Platinum / Palladium Printing
14:15 36Platinum/Palladium Coating Chemistry and Safety
09:58 37Platinum/Palladium Paper and Coating Options
22:31 38Platinum/Palladium Exposure and Development
22:31 39Platinum/Palladium: Equipment and Supplies
16:48 40Ink Jet Negative Coating and Exposure
15:25 41Platinum/Palladium Chemistry Options
07:50 42Ink Jet Negative Development
03:45 43Platinum/Palladium Waxing Images
08:40 44Platinum/Palladium Troubleshooting and Resources
27:19 45Sharing Your Work Digitally
14:49 46Archivability
10:39 47Matting and Framing Options
30:22 48Editions and Signing Options
13:54 49Alternative Processes: Further Exploration
07:25Lesson Info
Setting the Maximum Black Time
So the required minimum time is the minimum amount of time to get the maximum black in the print through the substrate we're printing on. Which is a very complex way of saying when I print black I want black to show up. (laughing) if I'm not printing black, I don't want it to be black. So that process of trying to get to that is the required minimum time. In the traditional analog darkroom we call this a maximum black test. And, this is one of the things in the book, in any book you see this demoed it looks like oh it's really obvious. You're gonna do this little test which I'm gonna show you how to do here in a second. And it's super, super easy to see. And I'm gonna show you what it actually looks like when you do the test. And it does require a little bit more effort than the initial book makes it seem. But, it's not a hard test to do. But basically what you're gonna have is you're gonna coat a piece of paper. So this is coated cyanotype. And there's no negative. Or nothing's on it.
It's just a coated piece of paper. At this point it's been processed and developed so it'd be easier for you to see. You'll see when we get to the actual coating process it's a really light, light yellow. But I wanted to make sure you'd be able to see this for the test a little easier. So it would normally not look like this. This is a piece of our transparency that we print on. A full sheet, actually for this size, comes as a 8 1/2 by 11. It's, we're using from a company called Pictorico. And it's overhead transparency, premium overhead transparency. Comes in 8 1/2 by 11. 11 by, 11 by 17. 13 by 19. It comes in rolls. So you can get a variety of sizes. There's also Ink Press is another company that makes overhead transparency. But pretty much any overhead transparency. And what's kind of funny about this is I used to, when I was getting my master's degree, and I was teaching at the university, we used to run these through the copier to make transparencies that literally went on the overhead to project at the university. So it's kind of a cool repurposing of this very older technology. They re-engineered it though so it'll actually hold the ink. So there's, one side's a little porus, the other side's a little slick. You can see in this upper corner right here there's a notch. That notch tells you the printable side. So when that notch is in the upper right hand corner the, what's facing you is the printable side. So that's how you know to load the printer. So basically that little notch would go however your printer wants it to go to be loaded. That little notch is your indicator of how to load. If not, it goes on the wrong side. If it goes on the wrong side, yeah, ink does not stick to it. And it gets this kind of swirly, Picassoesque, abstraction going. And you think that's pretty cool. But it won't dry for you to print. So, either way it's, it kind of comes out bad. If that does happen, just get plain copier paper and run it back through your printer and that'll clean up the, kind of the mess. It's not the end of the world. But a few sheets of just paper running through a print cycle will clean the issue up. But you're gonna need a little strip of that. And then you're gonna sensitize your paper. And I'll show you this again when we get to the actual cyanotype so you can actually see when it's coated. You're gonna lay that down so that it's only over half of what you've sensitized, or a part of what you sensitized. And then you can see here, it's marked at five, and then plus one, plus two, plus, or sorry, five, plus one, plus one, plus one, plus one. What that indicates is where these tic marks are, it's gonna get a base time of five minutes. And then we're gonna add a minute to each one of these. And that's gonna give us five, six minute exposure. A seven minute exposure. An eight minute exposure. And what we're gonna be looking for is at the point where this blue and the blue that shows up through this material match and are the same. And what that means is that the, this clear piece of overhead transparency has the ability to block up some level of light. And what we're trying to get to is, at what point does the light coming through here match the light that's not being blocked up by that? And that gives us our minimum required print time. So, if you're thinking about, so you're basically building a test strip, if you're coming out of the analog world, you're building a test strip to find where those two points match. In the old days when you built a contact sheet you were looking for the sprocket hole just disappeared. That would be our maximum black time. And then what happens though to get that process is you're gonna have, this is called a contact frame. On the back are some spring hinges. When we get into the cyanotype I'll talk about the different types of contact frames. And why you would choose one over the other. But basically what would, you'll do, is you will take, and that was louder than expected, (laughing) you'll take that, you'll put it face down. You'll put the contact frame back on. And then this now has my un, what would be my unexposed part. And my transparency. Then I take a piece of cardboard that blocks up light and basically I would start at the five minute mark, I'll go sideways so it's easier to see, and then I come a minute. And after another minute I move it again. After another minute I move it again. And then I would move it again. And I move it again. Now this is gonna be under a UV light box which you'll see, so that's why those tic marks are important. Because that way you can kind of look down underneath and you can pull it, and then come back up, pull, come back up. 'Cause you don't want to look at the ultraviolet light. 'Cause it'll damage your eyes. So it just gives you a quick peek. And for that. For those of you who looked at the eclipse, you'll be able to stare at it as much you want. (laughing) I'm just kidding. Don't stare at the UV light. But you're gonna move that back. And then once that's done, it'll go through the processing. That will then get processed. And you'll end up with the marking of a test strip. This is closer to what they actually look like versus what the book looks like. So you can see right here, this edge, that straight line edge right there that's the edge of the transparency. So this got the least amount of time 'cause it's the brightest. And this got another minute of time. Another minute of time. Another minute of time. And another minute of time. And what we're looking for is somewhere around here, you can see that adding more time, it doesn't get any blacker. But what happens then, if I had a negative up here, the whites would start to get blacker if I started to expose back here. 'Cause I don't gain anything by adding the additional time. I actually lose contrast. So what I'm looking for is at the point at which it, I can, can't see the difference, but if I go any farther there's nothing there. And then so that's one, two, three, four, between four and five minutes on this one. So I would probably do four-and-a-half minutes as a test. And because I'm highly anal retentive about my time, I would actually then make a four, four 15, four 30, four 45, five, five 15, five 30 test. Because it's cheap to make a little test strip like this. If that time is wrong, you're curve is gonna be wrong. This, people will kind of bypass, they kind of futz around, they kind of, ah, it's around six minutes. You're gonna compress the tones in the curve if you don't get that time right. So this is the test to be the most critical and work on. Here's another one. On this one, the edge of the paper is right here. But I brought it too far down and I didn't leave myself enough of a space so this was a wasted test. 'Cause I didn't leave myself enough of a gap to be able to see the edge. This is one that were in too long. So I didn't know, like I was starting off. I had never done this chemistry before. So I was like, you know, most of these processes are somewhere between four and 15 minutes on the box I have. So I'm like, ah, okay, well I'll start at like five minutes. This process takes about two-and-a-half minutes. So I had just basically started with zero. This is another one. In this one you can barely see, I doubt, I don't even know if you can see it on camera, the line is right here. Right in the middle. And this was three minutes, four minutes, and five minutes. At five minutes it starts to disappear. The other thing that people do where they make a mistake with this, is they start to do things like this, like can I backlight it? Can I put it up under the brightest light possible? They get a flashlight out. No, no, no. The normal viewing conditions you would look at artwork under. So if you've got lights on in your house, go outside. If you're at home, and you're like, I don't have very good art light. Or I only have one 40 watt bulb in my house. Go outside and look at it just in the daylight. The other thing is it can only be judged when it is completely dry. I don't mean like, ah, it's, it's dry enough. No, it needs to be completely dry. Some of these processes will change by over a stop when they dry. So if you're thinking about a doubling of time as a stop they will dry down and almost cause a doubling of time. So if you judge it when it's wet, and then you come back in, your time's gonna be off. So, when I'm doing this kind of work, I usually get the coating done, I make the test, I let it dry over night, and let it just naturally dry, and then I come back in. Some of these processes you can accelerate with a hairdryer. But getting that time, you just, it has to be dry. The big mistake I see is either people look at it in too bright of light or they judge it when it's wet 'cause they're excited to get the print done. But, that time is really critical. So getting that required time is really the key to a successful print for that. Okay. So once you have that required time the cool part about that is for your light source, except for the sun, 'cause the sun changes arcs and times, and I'll talk about how to work with the sun for these processes when we cover 'em, but if you're using a controlled ultraviolet box or LED lights or a metal haloid bulb, you're using something to control your light, which we'll talk about when we get into the cyanotype, that time is never gonna change. That's the beauty of these exposure boxes. So once you know a cyanotype in your light box it gets that maximum black at three minutes, or if it's five minutes, whatever it is, it's always that time. So you're gonna do a cyanotype, six minutes. Five minutes. Every single time. And then occasionally, you're gonna come in and just retest that time. 'Cause light bulbs will diminish over time. So they'll get slower and slower. So you just gotta come in and retest. I replaced the bulbs in my light box recently and my times got cut, like my cyanotype used to be nine minutes and it got cut to three minutes. So the new bulbs are just that much stronger 'cause I had been using 'em for years and years. So, so as you work with that the great part about this process is the time gets very consistent. With traditional negatives the density of the negatives change all the time and so the, you might have, you'll be varying the time a lot more than you would with a digital negative. Completely possible. Completely doable. We'll talk about how to do it. But, that required time is consistent. And each process and paper will be different. So a cyanotype arches and a cyanotype crane paper will have slightly different times. They're gonna be in the, most of the time, they'll be in the ballpark of the same. But some papers are a lot slower. And so you literally might add a couple of minutes or longer to the process. So don't freak out if you're like, well wait a minute, I was four minutes and I got this new paper and it's eight minutes. It is what it is. That's part of the process.
Class Materials
Bonus Materials with Purchase
Ratings and Reviews
Diordna
For a long time, I have read, studied and tried alternative processing, mainly Platinum/Palladium printing. I want to create longest lasting prints and may be share the info at Creative Live. But this presentation saved me many a hours. A few minutes into the lecture, I purchased the class and as the class progressed, I was extremely glad. Thank you Creative Live, thank you Daniel Gregory.
SFX
Excellent class on Alt Process and fantastic bonus materials included with purchase!!! I have extensive digital printing and darkroom experience but haven't done much alt-process to date. This is perfect timing for me as I have several personal projects that I would like to re-visit using some of these techniques. Thank you Daniel!!!
James H Johnson
I have been making platinum/palladium prints for about 1 year. This is the 3rd workshop that I have attended. The first two were one on one. Daniel has done a fantastic job of covering the material and explained the process it detail and easy to understand. This course is fantastic and highly recommend it.